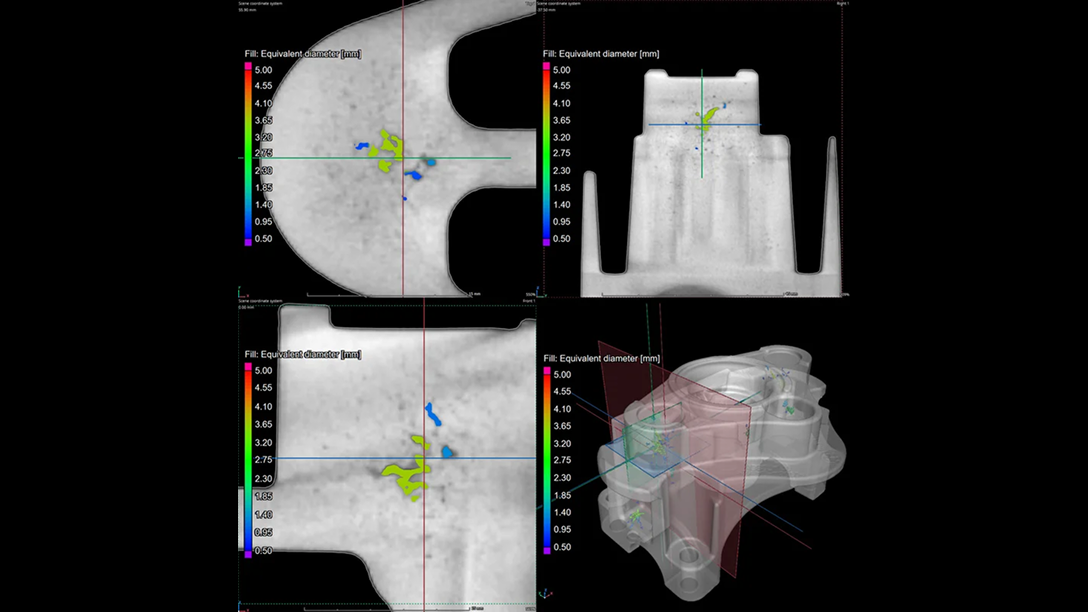
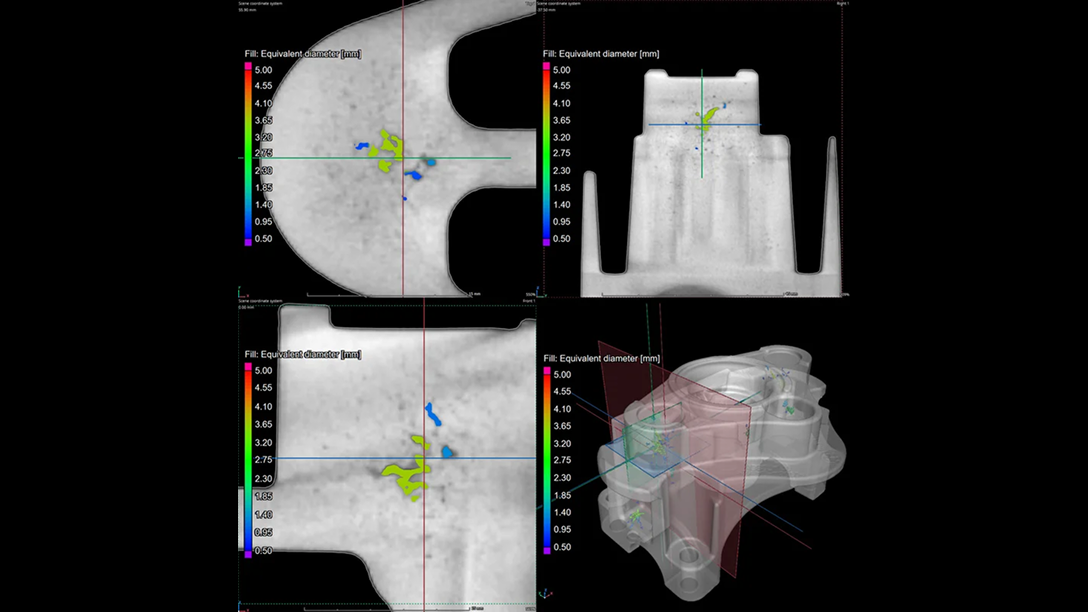
孔隙/夹杂物分析功能
找出零件内部的孔、洞和夹杂物,并详细了解有关这些缺陷的详细信息:
- 使用计算机层析成像技术在 2D 和 3D 中检测、表征和可视化孔隙
- 区分气孔、缩孔、裂纹和异物夹杂物
- 结合壁厚分析和后续加工步骤
- 遵循 BDG P 201/P 202 准则,自动量化 2D CT 切片图图像中间缺陷的表面尺寸
- 遵循 BDG P 203 准则,针对零件功能区域中最关键的孔隙度参数进行 3D 评估
- 获取结果,以便用于后续模拟
- 在统计评估软件(例如 Q-DAS 的 qs-STAT)中使用数据
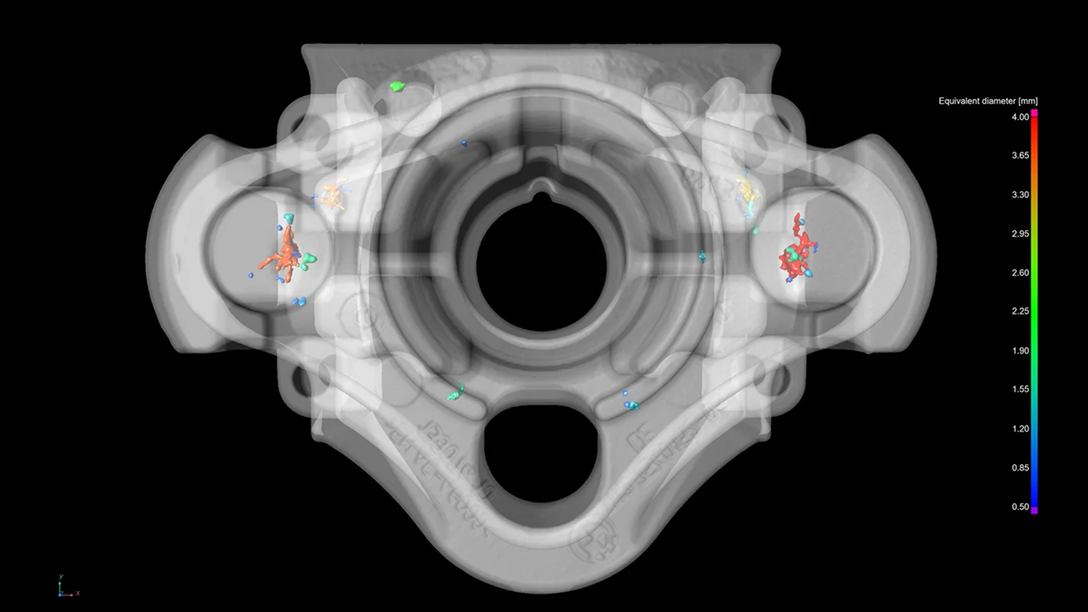
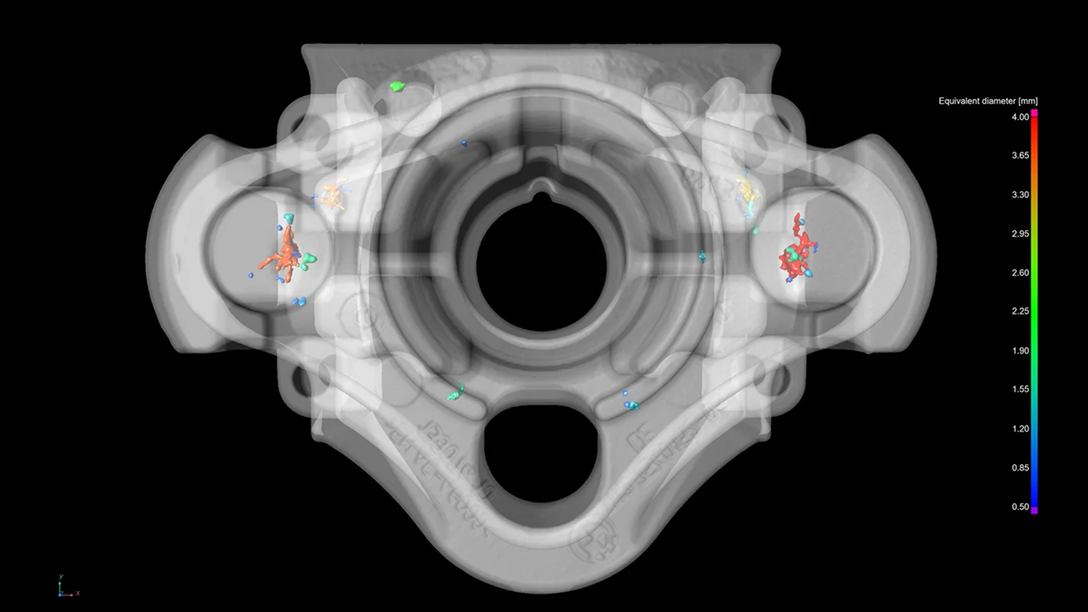
全局孔隙度参数
可以确定整个分量的这些全局孔隙度参数:
- 孔总体积
- 材料总体积
- 总孔隙度
- 孔总面积
- 在任何空间方向上所有孔的总投影面积
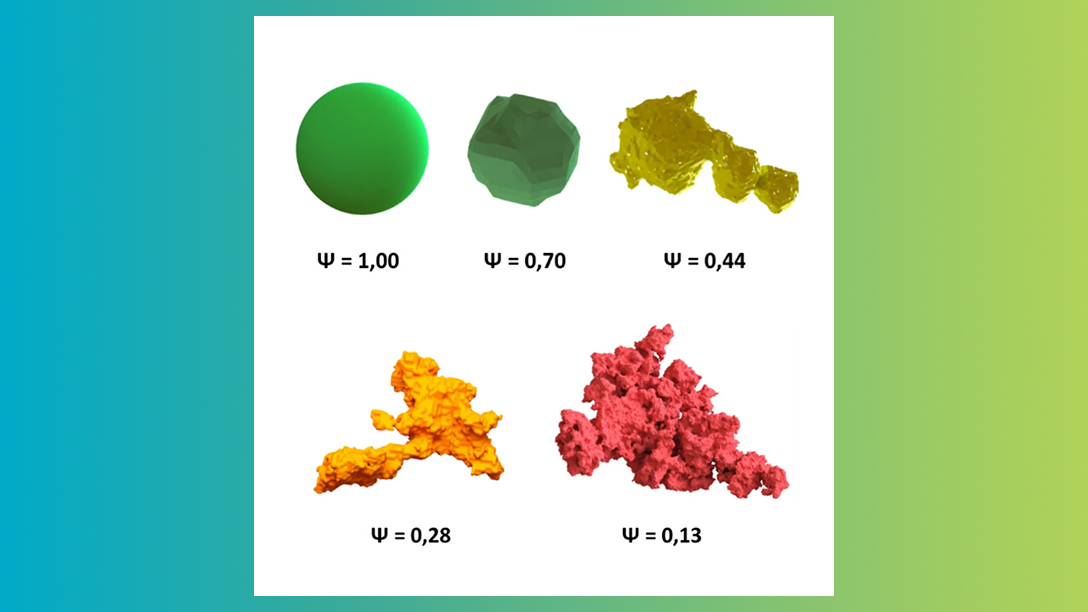
球度(来源:BDG – P 203 / www.bdguss.de)
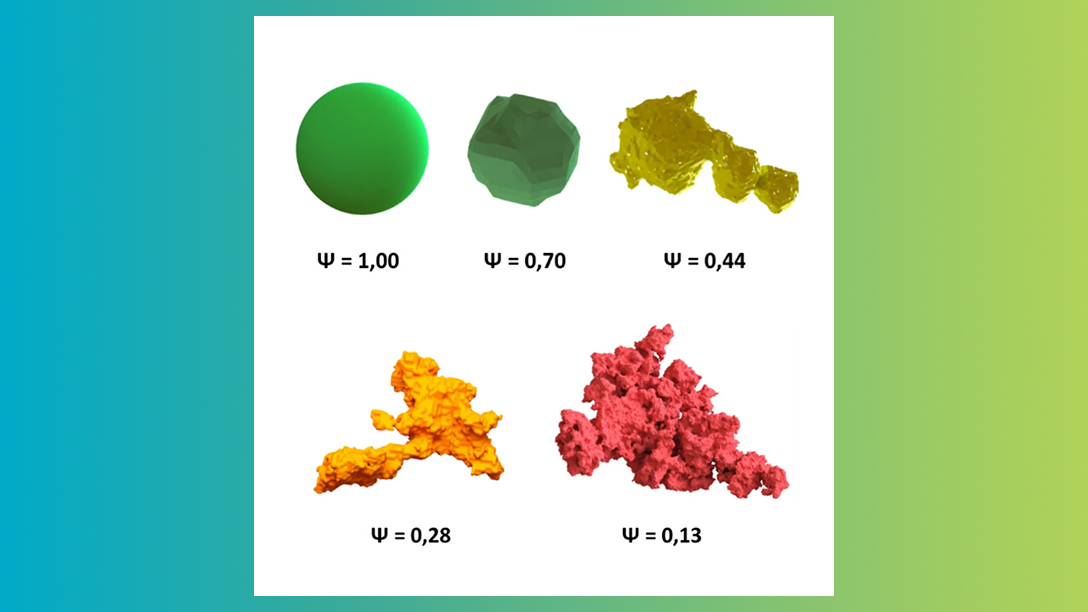
球度(来源:BDG – P 203 / www.bdguss.de)
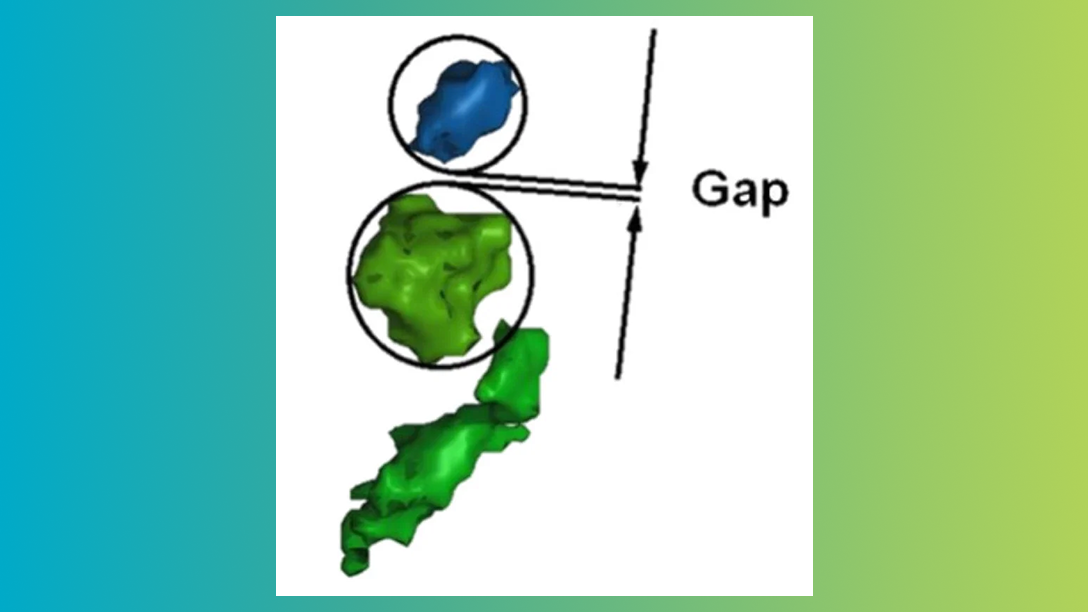
到下一个孔的距离(来源:BDG – P 203 / www.bdguss.de)
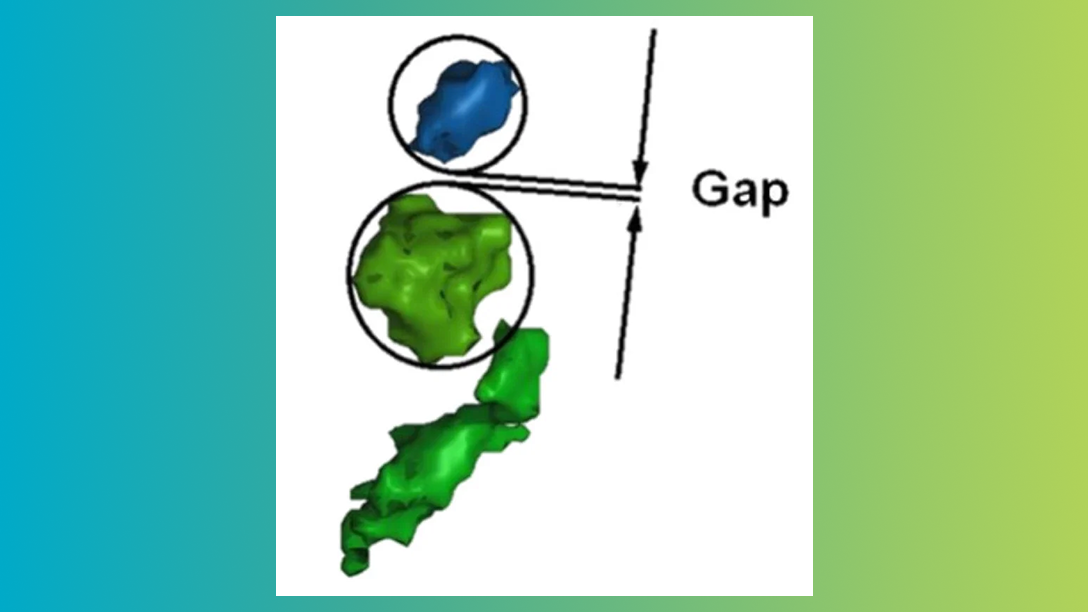
到下一个孔的距离(来源:BDG – P 203 / www.bdguss.de)
单个孔的属性
可以为单个孔确定这些参数:
- 常规:
- 位置
- 灰度值偏差
- 最小、最大和平均灰度值
- 尺寸:
- 体积
- 表面积
- 当量直径(体积相等的球体的直径)
- 半径或直径
- 形状:
- 紧密度
- 球度
- 拟合椭圆体的形状(来自主分量分析(PCA))
- 投影尺寸:
- 任意空间取向上的投影长度
- 任意空间取向上的投影面积
- 其他特征:
- 分类(在加工的表面内部、外部或被加工表面剪切)
- 最小和最大边距离
- 带有分量表面的切割面
- 到下一个孔的距离(间隙)
- 孔位置处的壁厚
- 相对直径(即相对于局部壁厚的孔的直径)
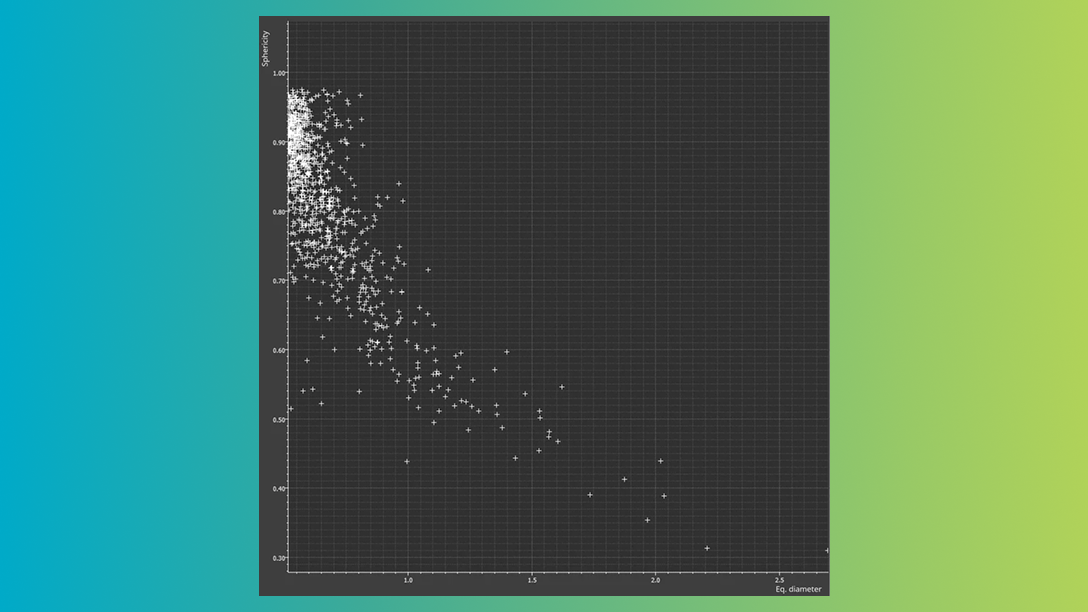
球度与当量直径的关系图
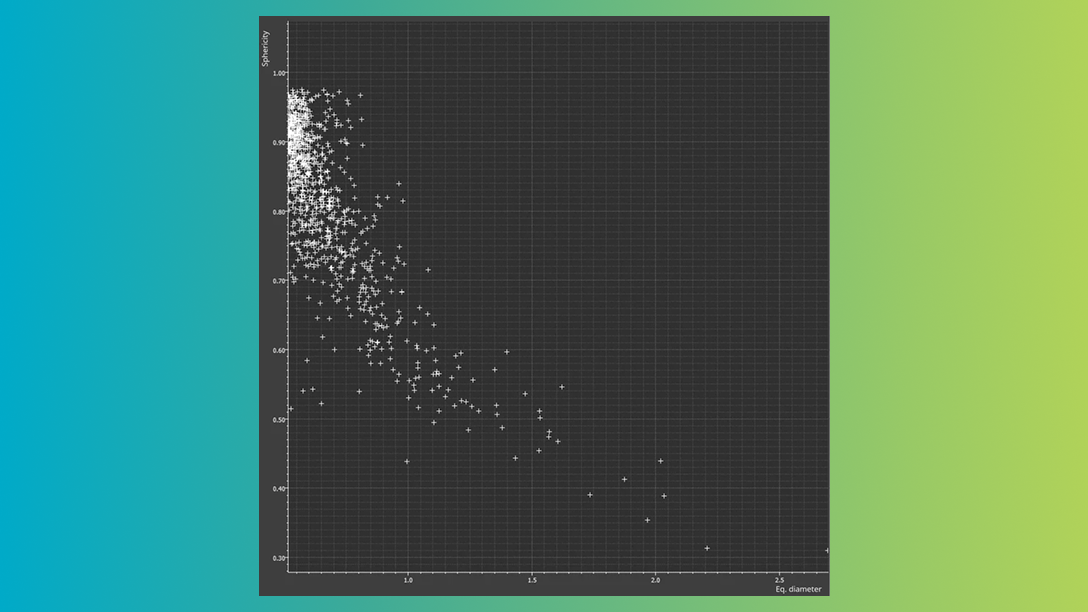
球度与当量直径的关系图
孔隙度参数之间的依存关系
除了对孔隙度参数进行计算和设置公差外,你还可以使用 y-x 图中合适的图形显示孔隙度变量之间的依存关系。例如,球度与当量直径的关系图可以显示出较大的孔为缩孔(通过较低的球度来识别)。
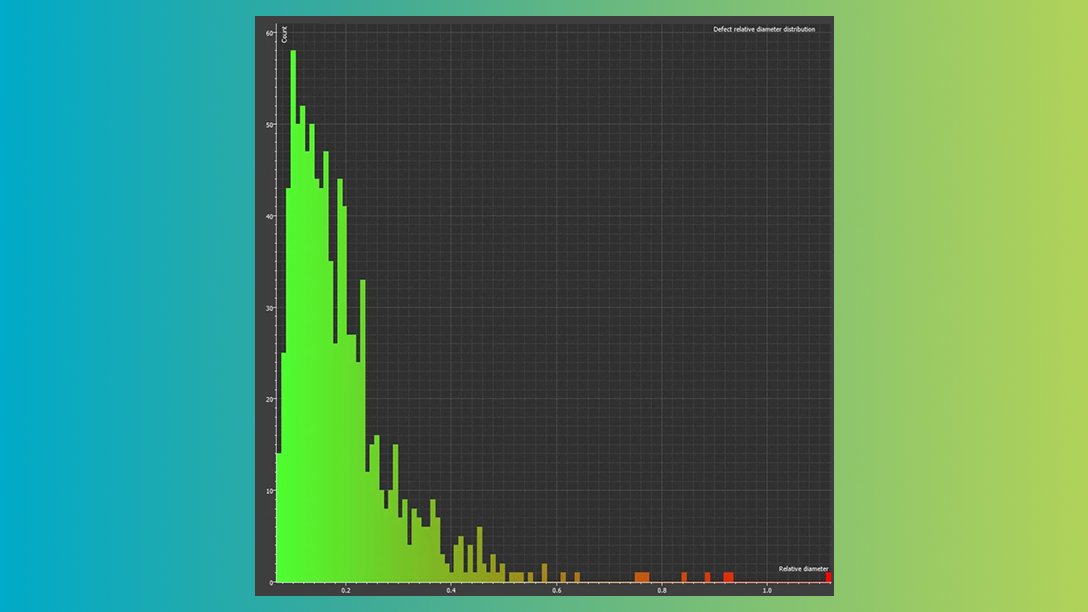
相对直径直方图
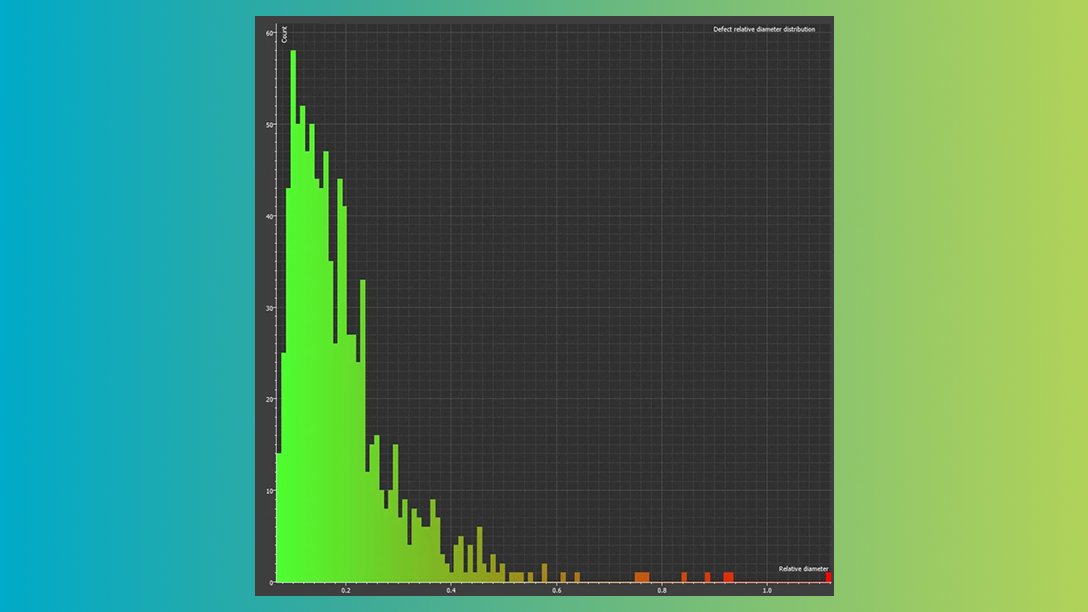
相对直径直方图
直方图
使用直方图可以显示相应参数值的分布。该示例表明,大多数缺陷的特征是相对直径较小。那些相对直径接近 1 的将被认为是至关重要的,因为孔区域中的空间范围和最小壁厚处于相同的数量级。
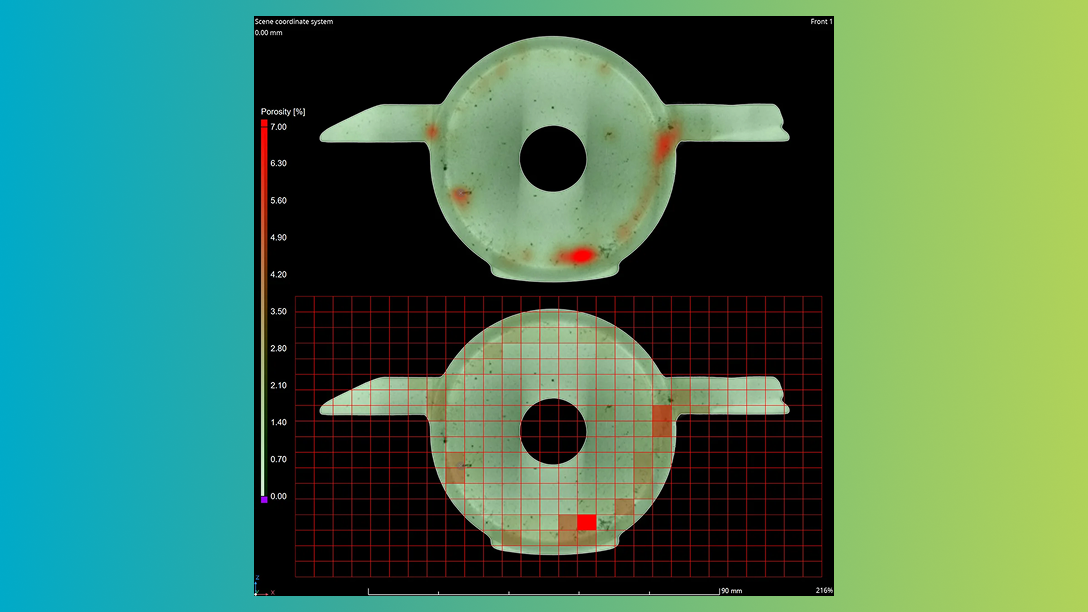
局部孔隙度(上图)和体积网格中的局部孔隙度(下图)
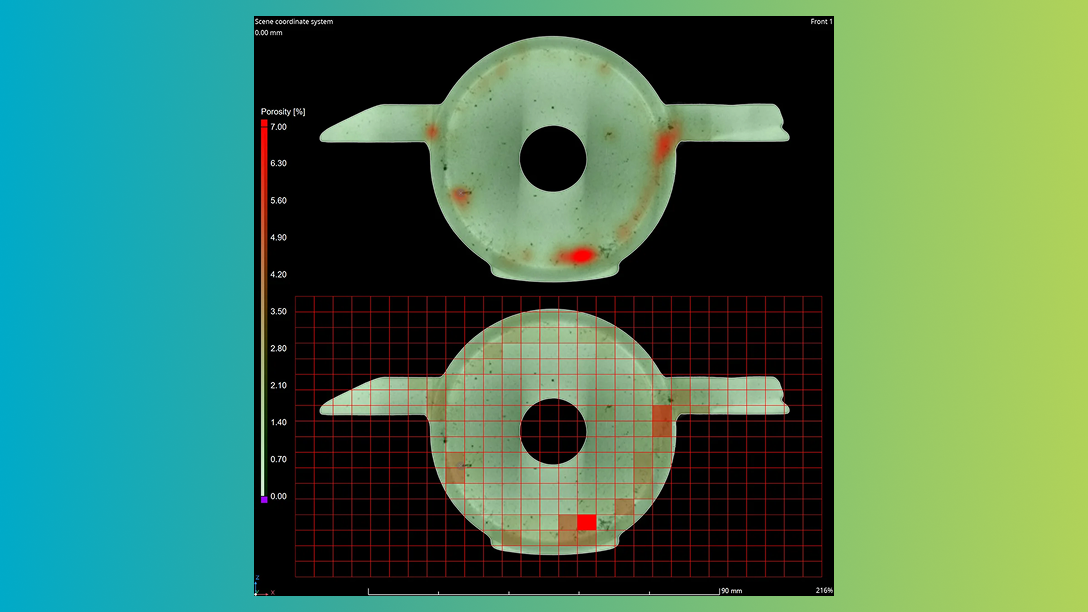
局部孔隙度(上图)和体积网格中的局部孔隙度(下图)
局部孔隙度计算
由于不仅仅是单一的缺陷对于零件的稳定性至关重要,因此使用我们的软件还可以更详细地研究孔隙度累积的情况及其影响。
除了计算局部孔隙度和局部热点,还可以将孔隙度映射到体积网格的单元格中。也可以使用常规网格以及适用于 CAD 或实际表面的体积网格。
实际相关的结果
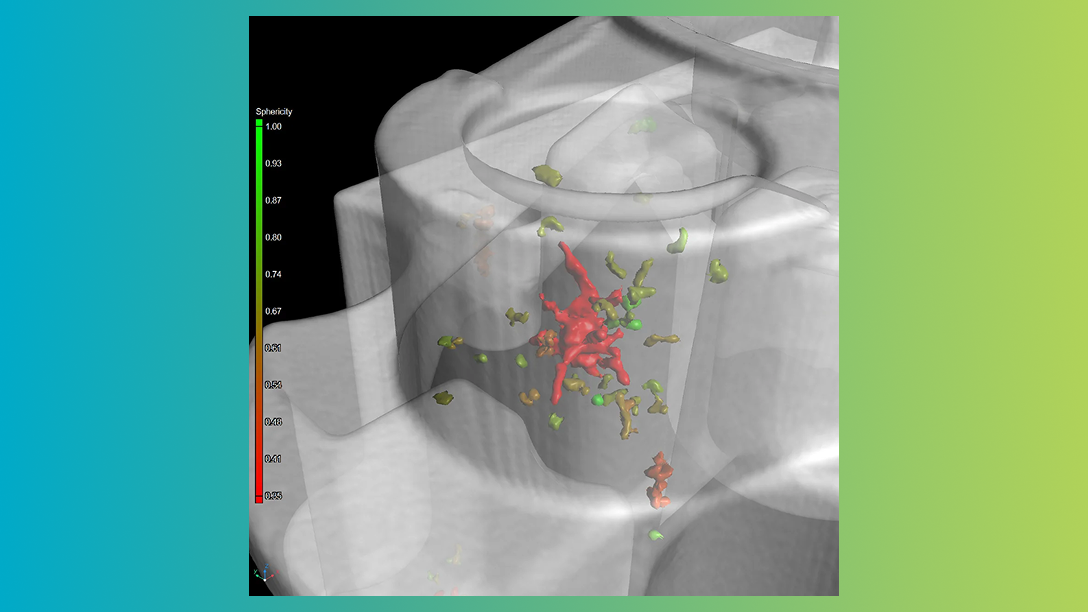
球度
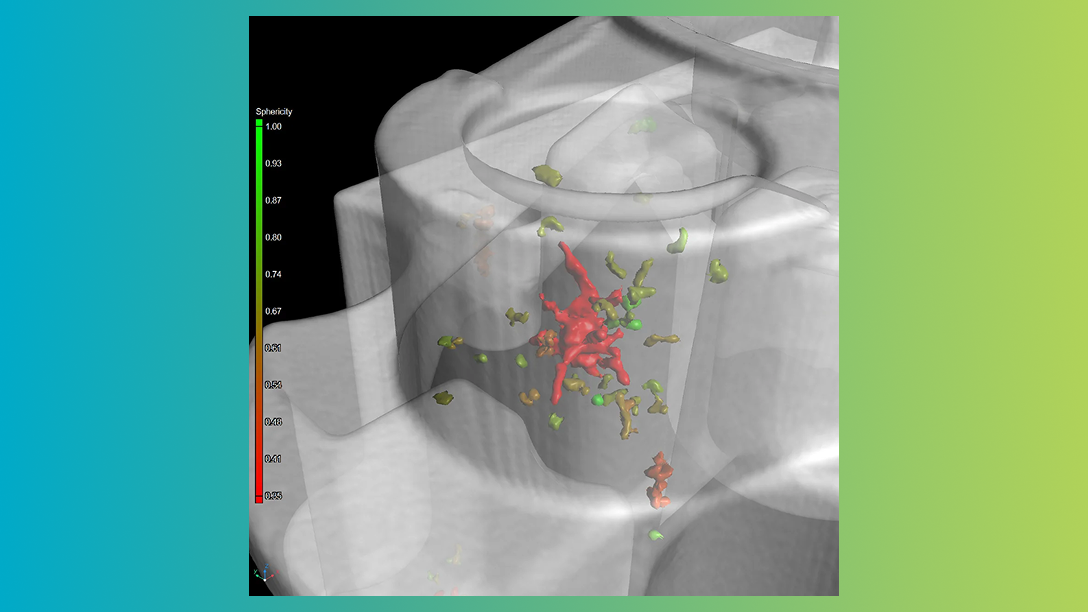
球度
相关孔隙度参数示例
根据某些孔隙度参数的结果,可以得出以下结论:
- 总孔隙度:通过长时间监测总孔隙度,可以轻松识别生产过程中的波动。如果该值呈上升的趋势,则表明浇铸速度不正确或模具型腔排气不良。
- 球度:球度值:通过根据孔体积和孔表面积计算出的球度值,可以区分气孔(具有较高的球度值)和缩孔(具有较低的球度值)。通过对缺陷形状的了解,不仅可以帮助优化工艺,还能提供有关部件耐用性方面的信息。
- 与表面的距离:通过计算与任意表面的距离,您可以在加工之前验证封闭表面和螺纹表面是否合适。孔隙度分析会模拟待加工的表面。可以计算出并可视化加工区域中剩余孔隙的深度。这对于封闭表面很重要,因为开放孔中的空气夹杂物会在热应力的作用下置换封闭材料。
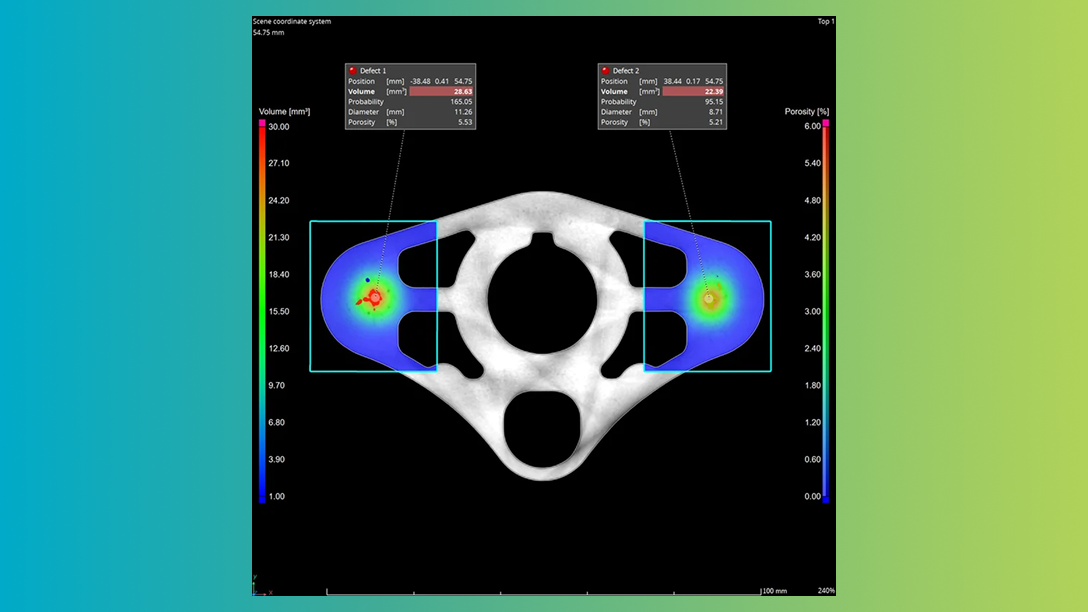
孔隙度分析可应用于零件上用户所定义的感兴趣区(ROI),并使用特定于该区域的公差标准
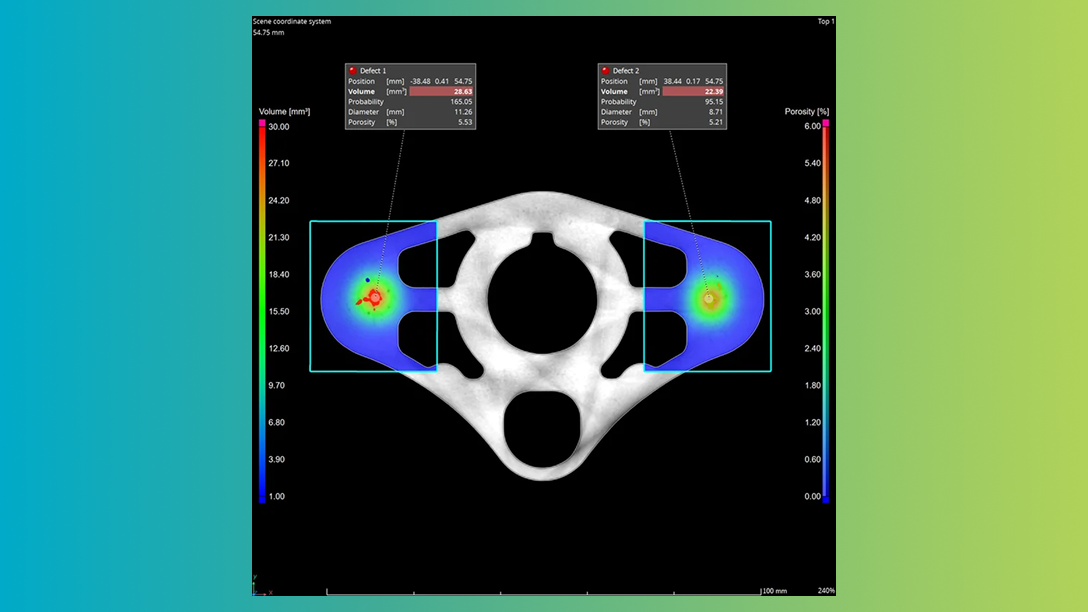
孔隙度分析可应用于零件上用户所定义的感兴趣区(ROI),并使用特定于该区域的公差标准
专注于功能区域
将分析限制在相关区域:
- 感兴趣区(ROI):您可以使用不同的滤波器和公差设置将孔隙度分析应用于零件的特定区域。例如,如果目标是检查铸件表皮表面附近的气孔,则可以将孔隙度分析限制在铸件表皮的区域。
- 缺陷可与壁厚结合起来。
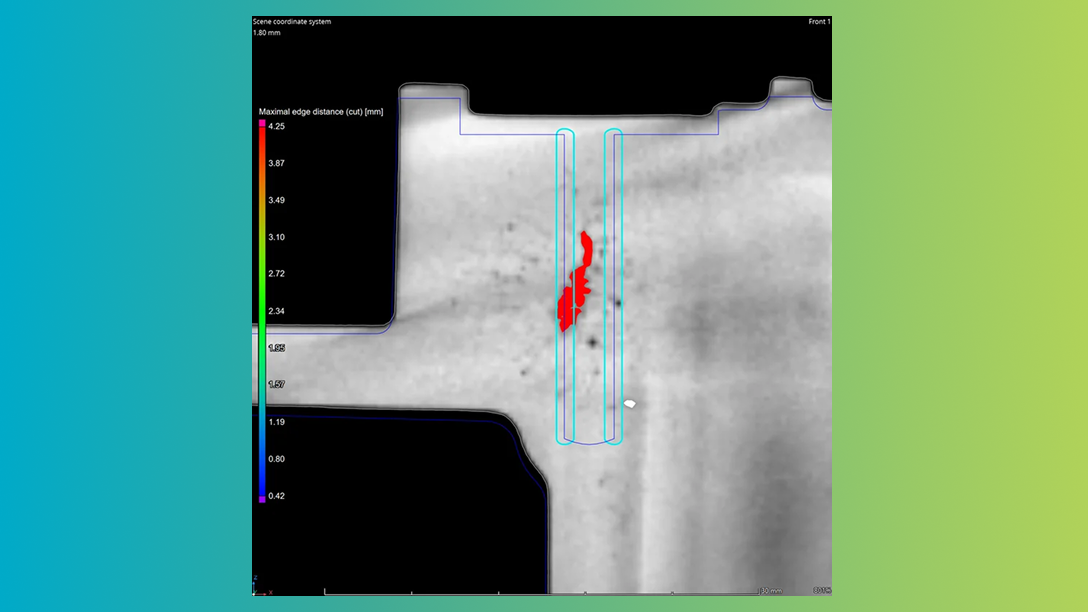
可以在分析中包括加工公差,作为与表面的绝对距离的参数
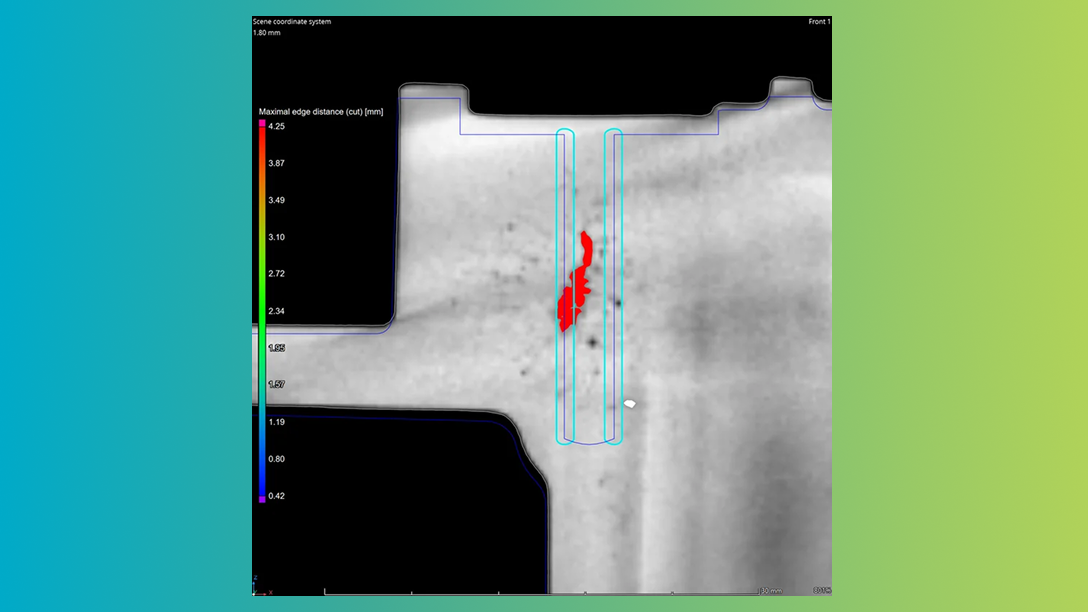
可以在分析中包括加工公差,作为与表面的绝对距离的参数
虚拟加工
可以看到孔是否会在加工过程中被切割,以及如何被切割:
- 不仅可以相对于当前零件表面计算孔位置和尺寸,也可以相对于任何其他表面计算孔位置和尺寸。
- 因此,您可以在孔隙度分析中模拟零件的后续加工(例如钻孔),并确定孔到加工表面的距离。特别是,您可以检查孔是否会被切割,而使加工过的表面被破坏。这样,您就可以在进行高成本加工之前对零件进行分类。
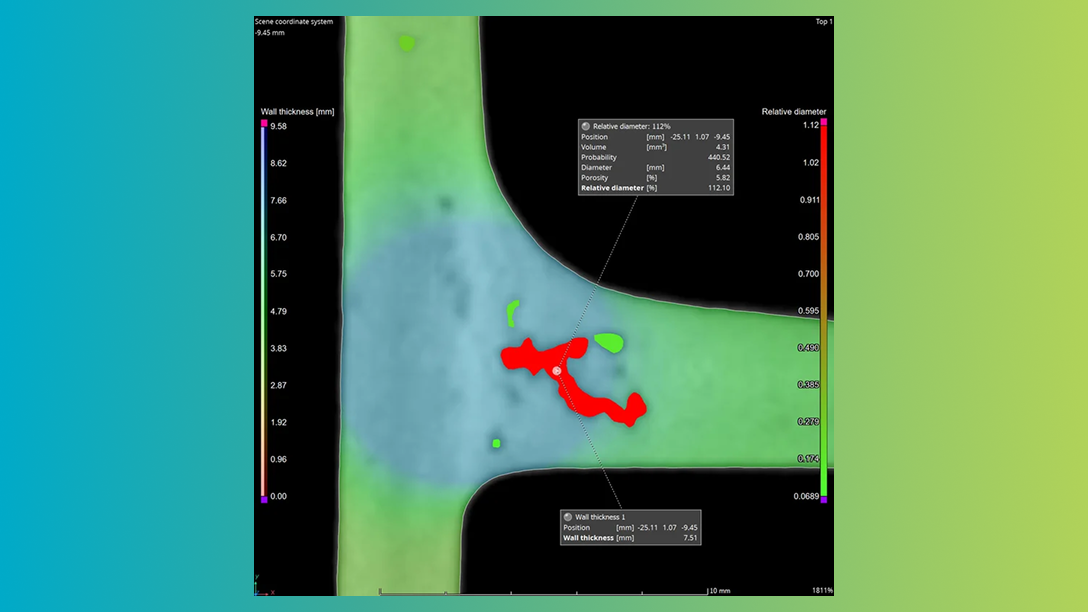
缺陷可与壁厚结合起来
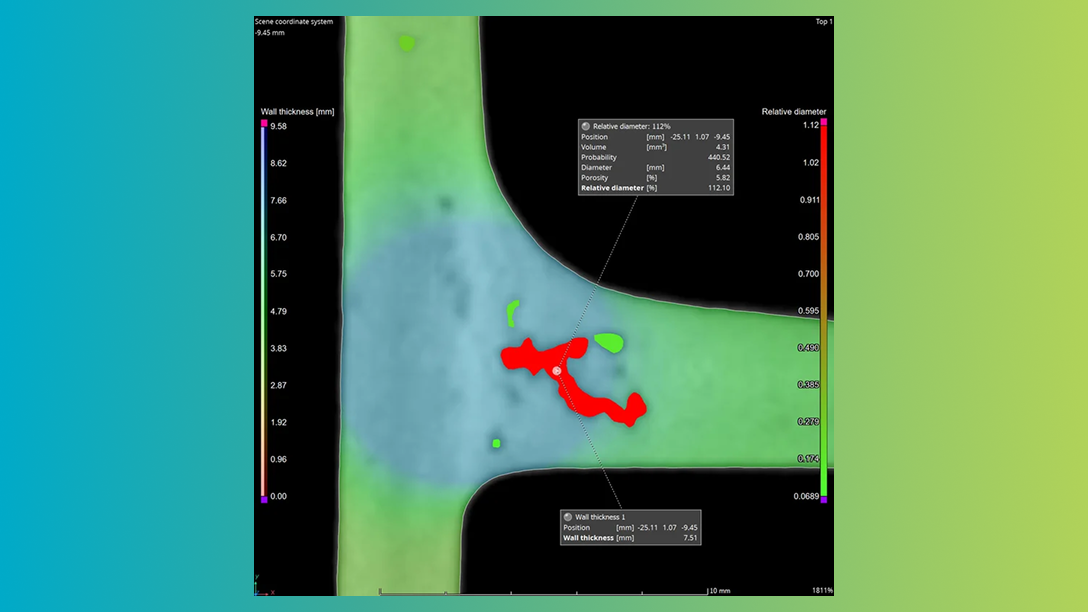
缺陷可与壁厚结合起来
多重公差标准的逻辑组合
使用决策树进行公差处理:
- 可以全自动检测铸件,方法是通过定义功能相关区域(特殊属性)的单个孔隙度参数的公差(例如单个孔的数量、尺寸和位置)来自动化检测铸件,同时将整个铸件的公差定义为全局孔隙度参数 (例如,最大总孔隙度(%))。
- 通过组合单个分析的公差状态来映射更复杂的问题,这在自动化在线检测场景中特别有用。例如,如果已经超出特定的孔隙,并且在铸件表皮区域存在大量的孔隙,则铸件可以被分类为“不合格”。如果不超过任何一个参数,则零件被标记为“合格”。
符合标准
孔隙/夹杂物分析模块支持三种最重要的孔隙分析准则,可对铸件进行简便且可重复的评估:BDG P 201、P 202 和 P 203。
P 201 和 P 202
为了对切片图图像中的孔隙度参数进行分类,软件使用了 VDG P201 (VW 50097) 和 BDG P202 (VW 50093) 准则。这些分析为经典的显微照片分析提供了一种数字化的、完全无损的方法,而在过去,这种经典的方法是通过锯开零件来实现的。
通过根据 VDG P 201 和 BDG P 202 进行的分析,您可以使用孔隙度秘钥对在任何方向的数字零件截面中的以下参数设置公差:
- 最大表面孔隙度
- 最大孔直径(等面积圆的直径 [ØF])
- 最大孔长度(“最大弗雷特直径”;类比直径 [ØL])
- 相邻孔之间的最小归一化距离
- 最大孔数
评估会在整个截面和用户设置的参照区域(正方形、矩形、三角形、圆形)中进行。
P 203
BDG P 203 不仅使 VDG P 201 和 BDG P 202 可以应用于 3D,而且还可以通过使用自由造型区域,额外对零件的功能区域进行特定评估。
VG 软件通过集成遵循 BDG P 203 的必要准则来定义用于孔隙评估的体积和定义体积内部缺陷的三维特征。通过直观的输入功能,可以使用孔隙度秘钥(遵循 BDG P 203)轻松地定义孔隙度准则。
VG 软件可以自动测出 BDG P 203 准则中提出的所谓“Q 因子”。Q 因子是一种简单、与用户无关的方法,用于验证灰度值体积的质量,并可直接在 P 203 分析中记录您的 CT 扫描数据的质量。
使用我们的软件,您还可以根据 BDG-P 203 对添加了参照表面的原始零件(例如 3D CAD 加工零件)执行孔隙度分析。这样,您可以预先评估待加工表面上的孔隙度。
可以在 3D 和 2D 窗口中自动显示相应的 BDG P 203 孔隙度秘钥和每个自由造型局部体积(ROI)经分析后得出的结果。这不仅有利于评估孔隙度分析,也有利于检查数据集中的方向。可以做出快速的 OK/NOK(“超出了该参数公差范围”)决定并记录下来。
针对所选的孔隙度参数,您也能够获取在全局体积内或自由造型局部体积(ROI)内超出公差范围的 NOK(“超出了该参数公差范围”)孔数。这使您能够区分异常值和系统性生产问题,从而实现更好的过程控制。
此外,遵循 BDG P 203 的孔隙度秘钥还允许在评估过程中排除特定的缺陷,依据是其孔隙参数,例如:最大直径不超过 0.6 mm 的气孔和微孔。
工作流程和界面
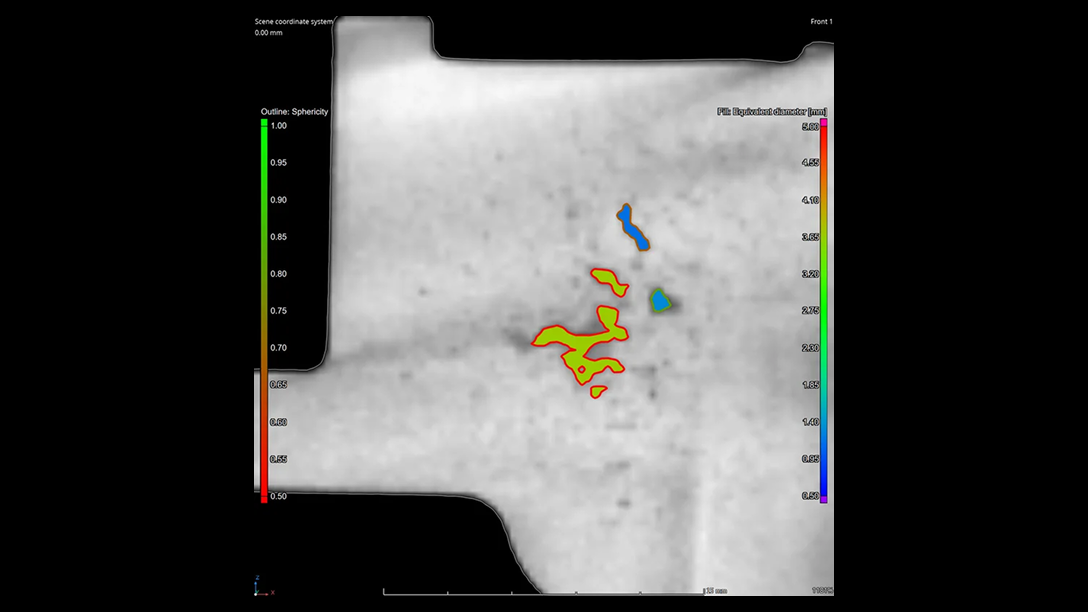
可以根据所选参数对缺陷进行上色
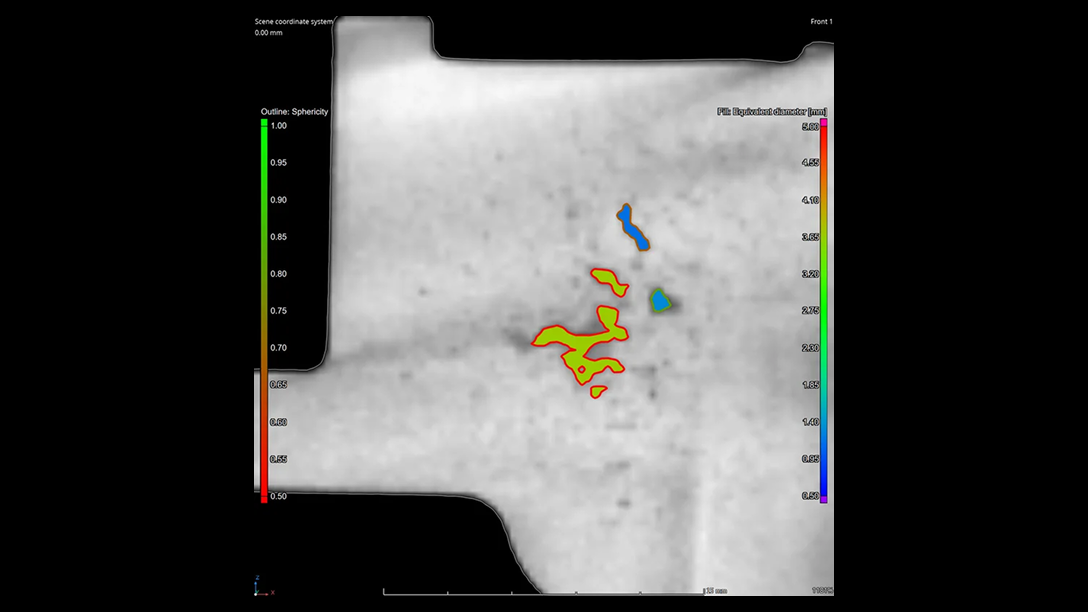
可以根据所选参数对缺陷进行上色
便捷的可视化操作
通过功能齐全且易操作的可视化功能,您可以解锁结果的真正价值。
导航单个零件和一系列零件:
- 可以根据所选参数对缺陷进行上色
- 缺陷以 2D 和 3D 视图的组合显示
- 可以手动和自动创建分析注解
- 可以在 VGinLINE APPROVER 中审阅一系列零件
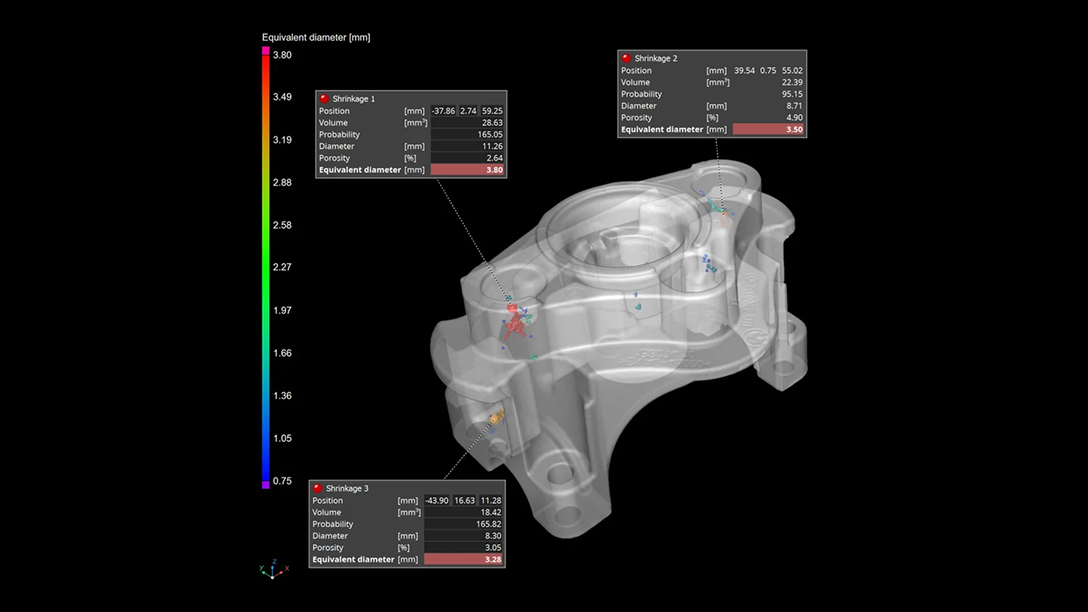
图像除了显示缺陷在零件中的位置之外,还可以通过分析注解直接在图像中显示所有孔隙度参数
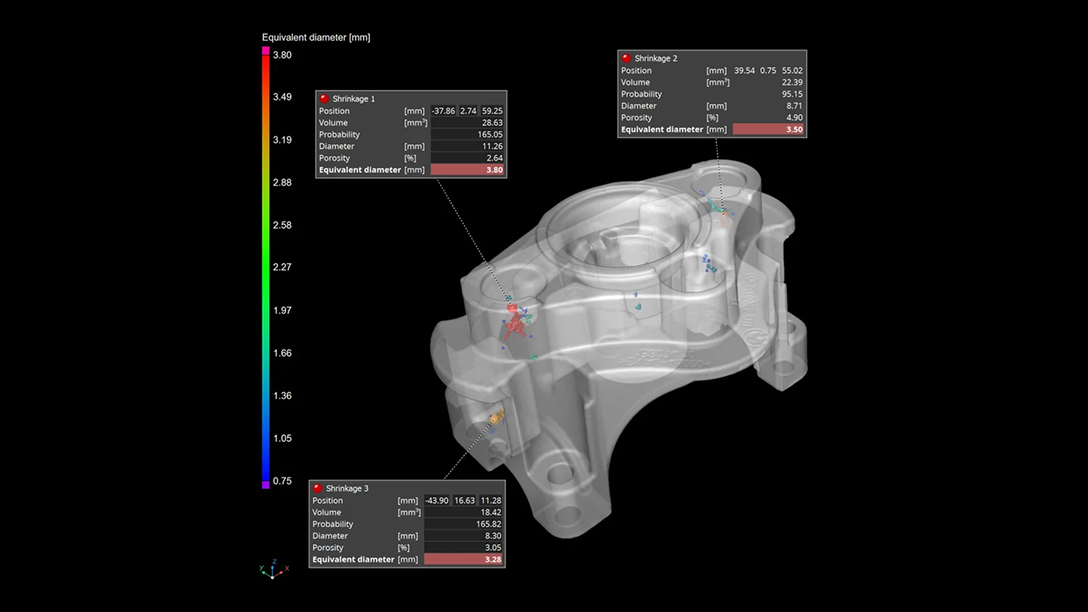
图像除了显示缺陷在零件中的位置之外,还可以通过分析注解直接在图像中显示所有孔隙度参数
手动和自动生成图像
- VG 软件提供了各种为区域和缺陷生成图像的功能。
- 如果需要,这些图像除了显示缺陷在零件中的位置之外,还可以通过分析注解直接在图像中显示所有孔隙度参数。
- 标准视图(例如具有检测到的孔的铸件的正交视图)可以提供零件的清晰概览。
- 基于规则的图像生成使您可以在特定情况下(例如,超出公差值时)自动生成图像。
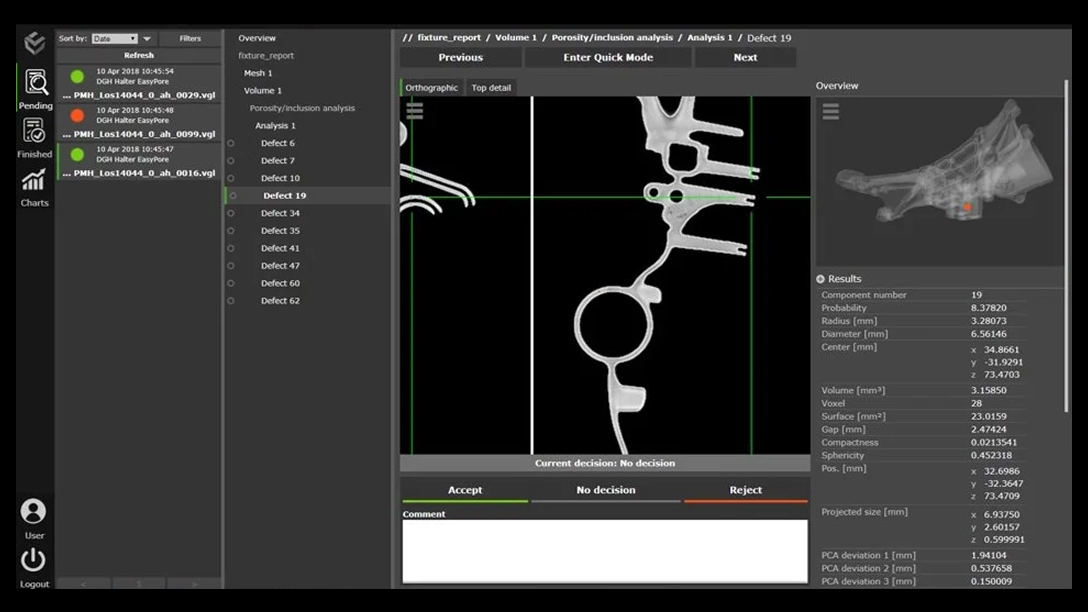
在 VGinLINE APPROVER 中对全自动检测的部件进行手动重新评估
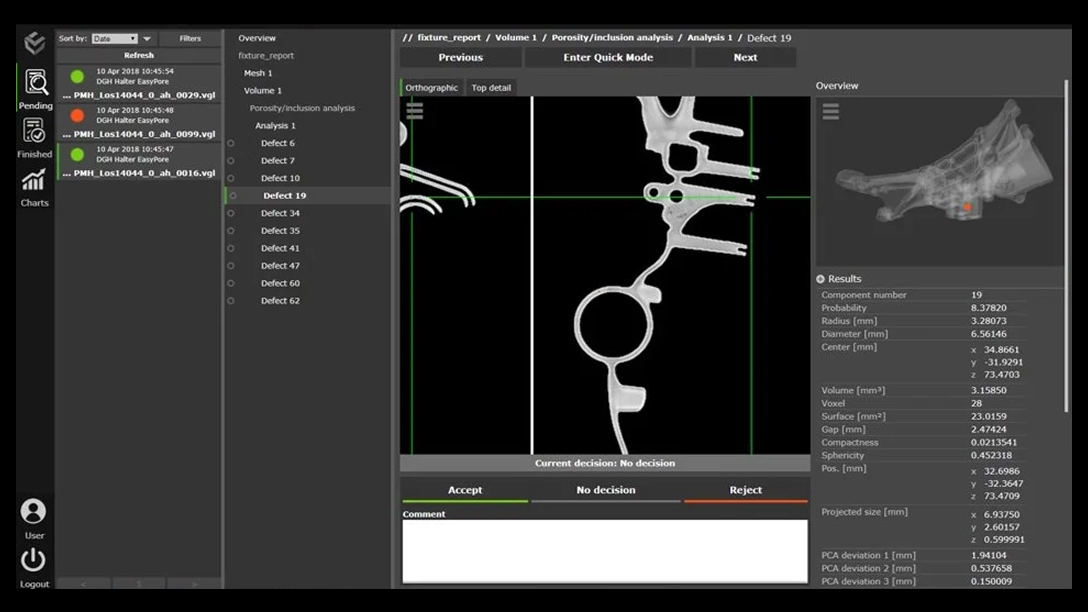
在 VGinLINE APPROVER 中对全自动检测的部件进行手动重新评估
自动化
使用 VG 软件,您只需点击几下鼠标即可部分或完全自动化您的手动工作流程。这样,您不仅可以在日常工作中节省时间,而且可以选择将自动化工作流程导出到 VGinLINE,以便在在线 CT 环境中使用。
特别是孔隙率分析,通过考虑到与生产有关的变化,即使在连续检测中也能提供始终如一的高标准检测能力。
借助高级的报告功能、统计评估功能(Q-DAS)和可对全自动检测部件进行手动重新评估的平台(VGinLINE APPROVER),您现在就能完全应对未来无损检测的挑战。
报告
使用全面的报告功能,您可以与不同的受众共享结果,即使他们没有使用 VG 软件。
借助 VG 软件中的报告功能,您可以:
- 报告结果,也可以记录评估过程本身。
- 创建高度可定制的报告。
- 以行业标准的 Q-DAS 格式导出结果,以可视化生产参数调整与零件质量变化之间的依存关系。
应用结果于模拟中
可以在随后的模拟中使用孔隙度分析的结果来进一步研究缺陷的影响。
通过以下方式,VG 软件的模拟功能将孔隙/夹杂物分析与模拟世界联系了起来:
- 将孔隙度值导出到体积网格(Abaqus、Patran 和 Nastran)。
- 对带有大孔隙的体积进行网格化。
- 直接在 VGSTUDIO MAX 中使用模拟(例如使用结构力学模拟模块) 。
夹杂物分析
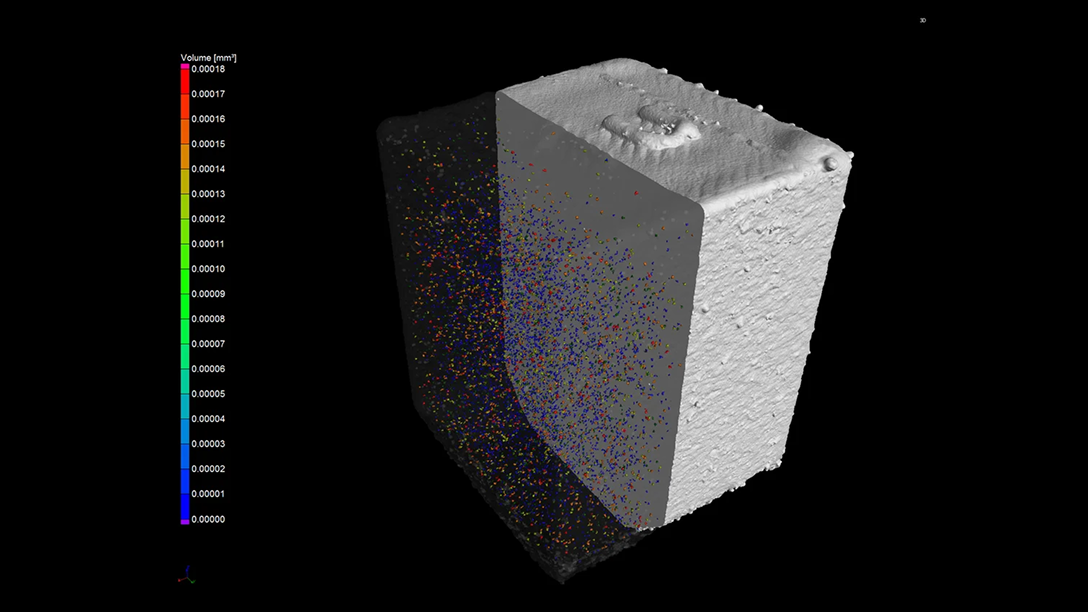
夹杂物分析
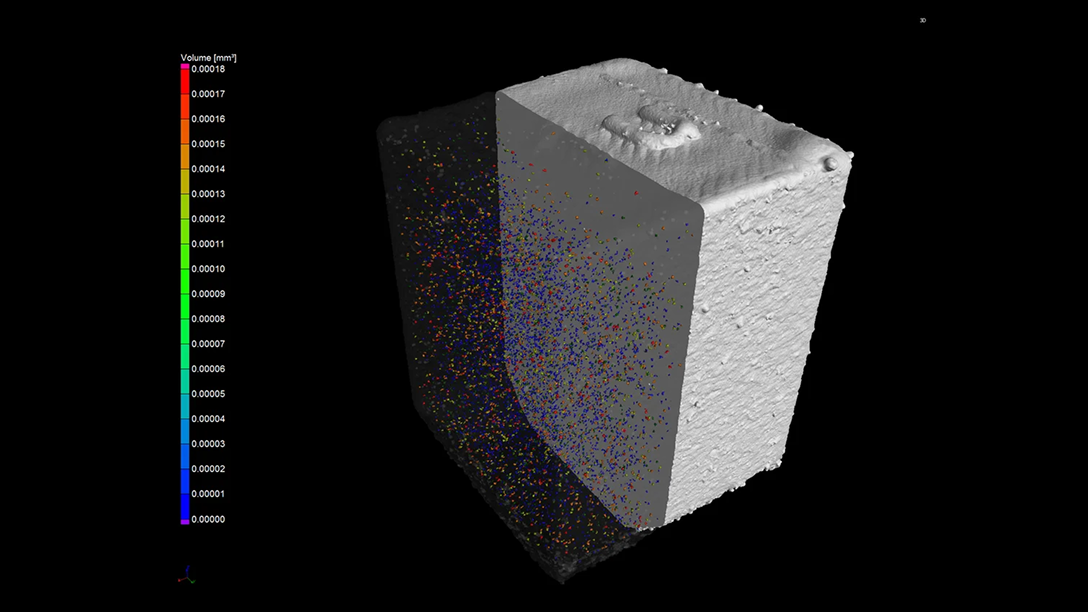
夹杂物分析
为您的零件探测内部颗粒
对缺陷的分析可以分为缺少材料(经典的孔隙分析),以及存在异物。
您可以用 VG 软件探测多余的杂质(例如在机器磨损的情况下产生的杂质),或者研究添加的功能颗粒(例如绝缘物里的金属碎片)的预期累积量。所有提到的与孔隙度有关的参数也可以用于描述夹杂物。
孔隙/夹杂物分析算法
VGSTUDIO MAX 提供各种孔隙/夹杂物分析算法,以确保针对每个零件和场景进行最佳孔隙度检测。为什么?因为在使用工业 CT 进行 3D 成像时,图像质量会受到许多因素的影响。例如,日常工业使用中的采集时间短,以及大型零件和多材料场景,都可能导致图像质量下降。噪声、条纹伪影、对比度和灰度值差异,以及金属伪影是可能影响图像质量的其他因素。
VG 软件已获得铸造和注塑行业的数百位用户的信赖,能够可靠地检测出诸如孔和裂纹等关键性缺陷,即使是在质量较低的数据中也能准确识别,确保不会遗漏任何关键瑕疵。我们对于 BDG P 201、P 202 和 P 203 准则的实施,获得了大众汽车等行业领导者的认可,这充分彰显了我们对品质与可靠性的不懈追求。
可通过用户自定义过滤功能对相关缺陷进行筛选,确保聚焦最重要的问题。可针对不同的 ROI 调整公差标准,从而实现精准的质量控制。 借助 VG 软件,您将获得有洞察力的分析结果,助您做出明智决策,提升产品完整性。
通过无缝缺陷检测和分析区域复制功能实现评估流程自动化,确保评估结果始终如一、准确可靠。即使是大型数据集,也能实现快速处理,生成详尽报告,确保评估过程全程透明。我们的工作流程实现了完全自动化,同时支持人工审阅,为您提供更高的灵活性与控制力。
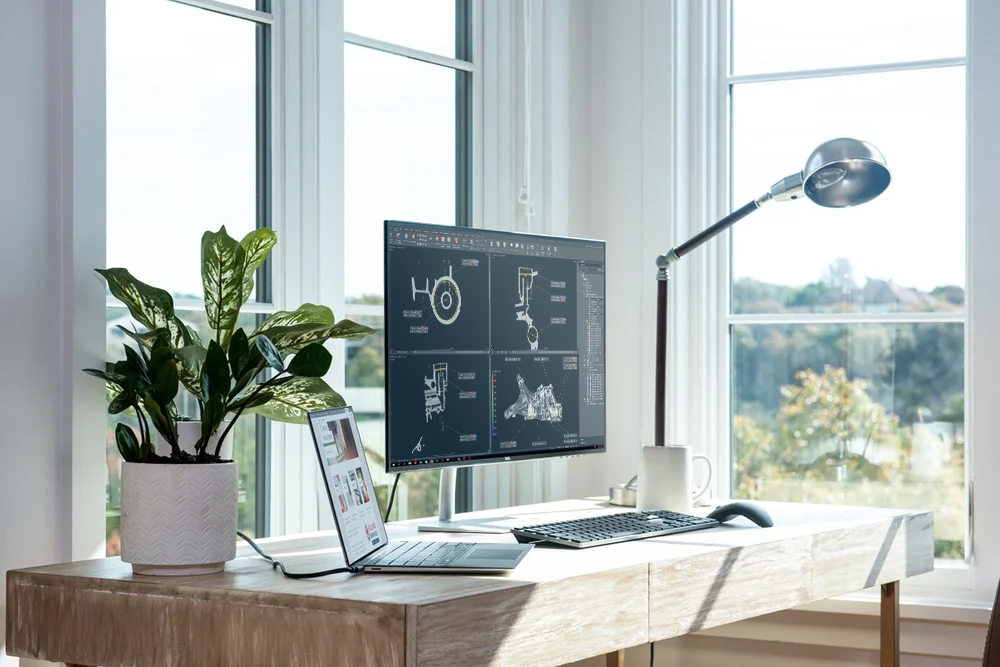