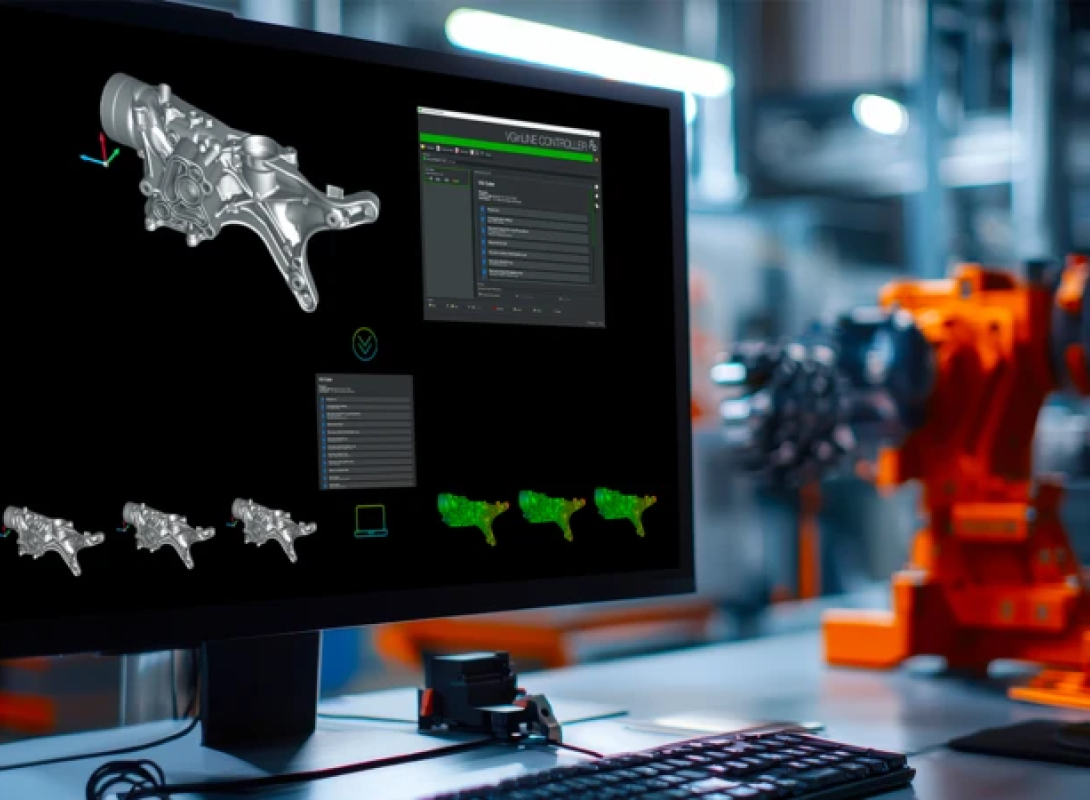
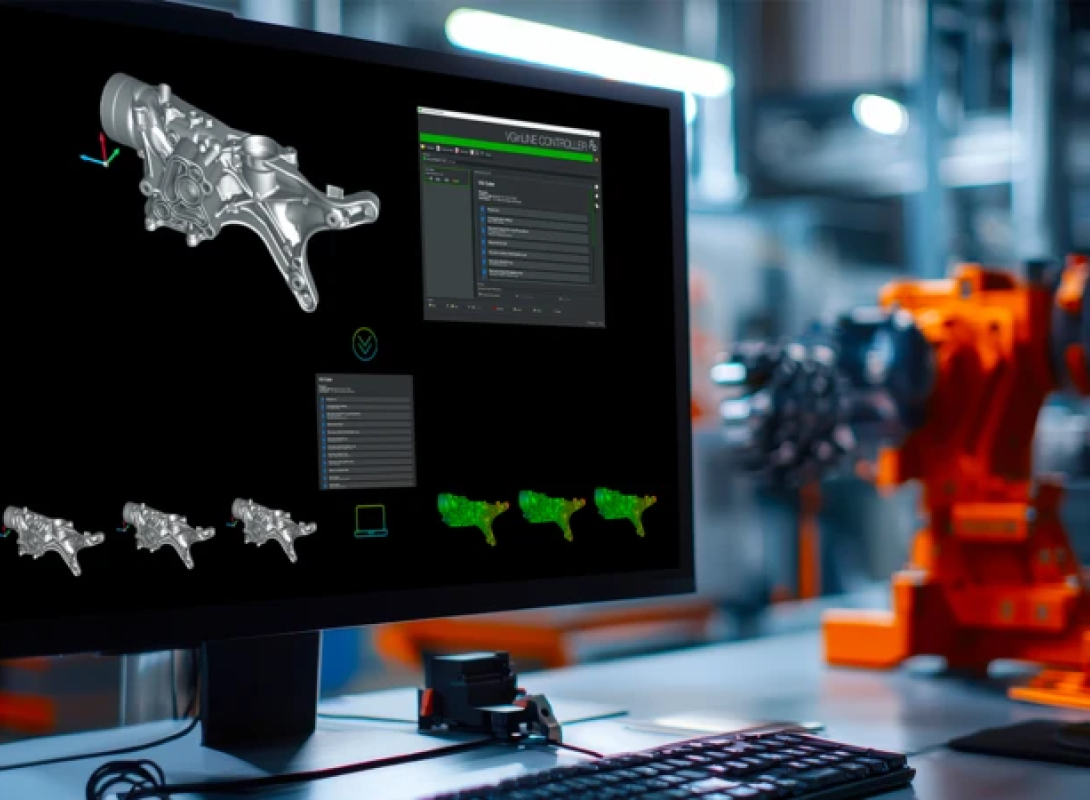
産業用CTとVGのソフトウェアでパーツの自動非破壊検査を可能にします。VGSTUDIO MAXによる自動化はセットアップが簡単で、ほぼ全てのCTシステムで利用できます。
VGソフトウェアを使用すると、迅速で柔軟性が高く、すぐに使用できるソリューションが実現します。パーツを繰り返し解析する必要がある場合にも、常に強力な自動化機能によって作業をスピードアップします。
スキャンしたオブジェクトがめったに繰り返されない場合でも、あらゆるタイプのオブジェクトに適用できるため、一般的なワークフローの反復部分を自動化する価値が十分に得られます。
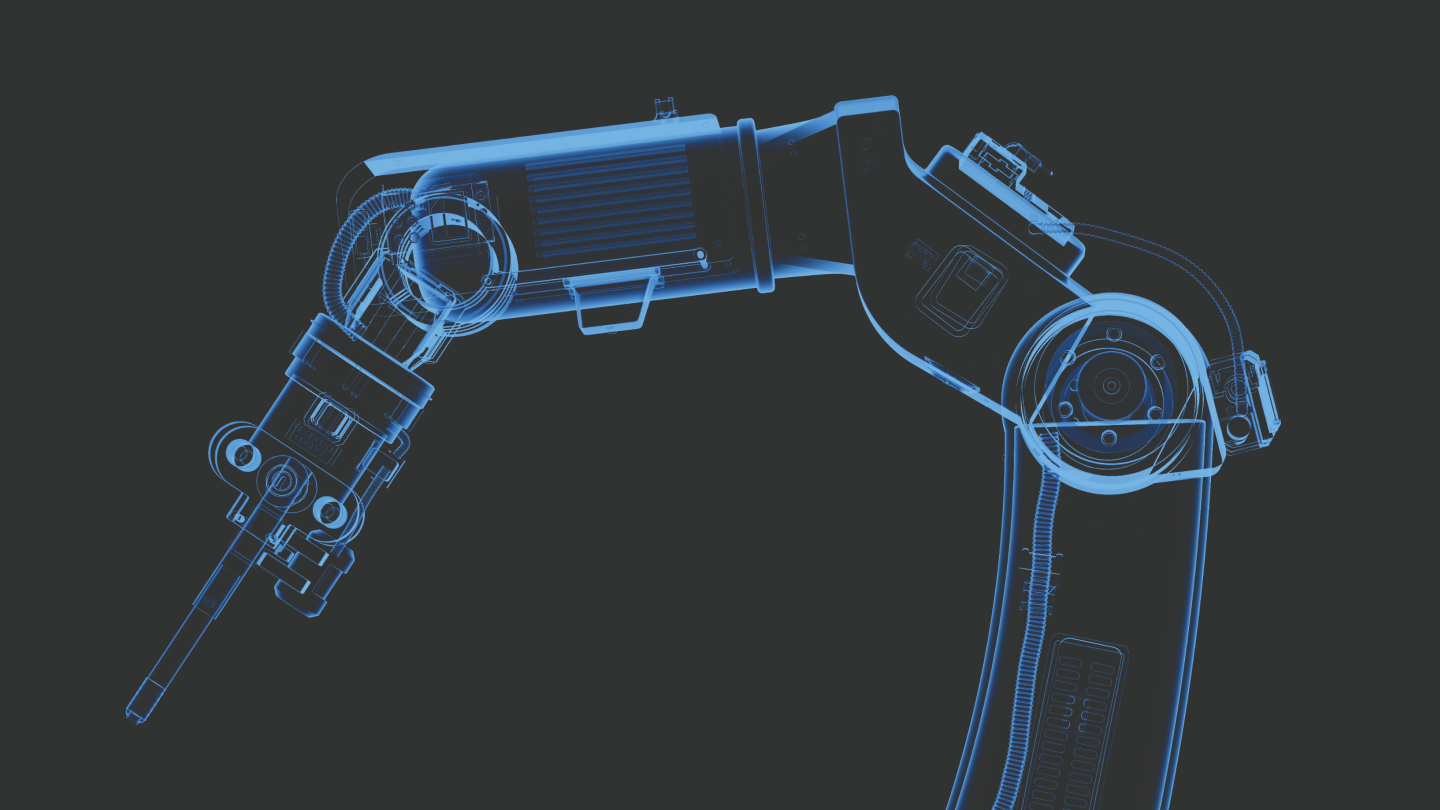
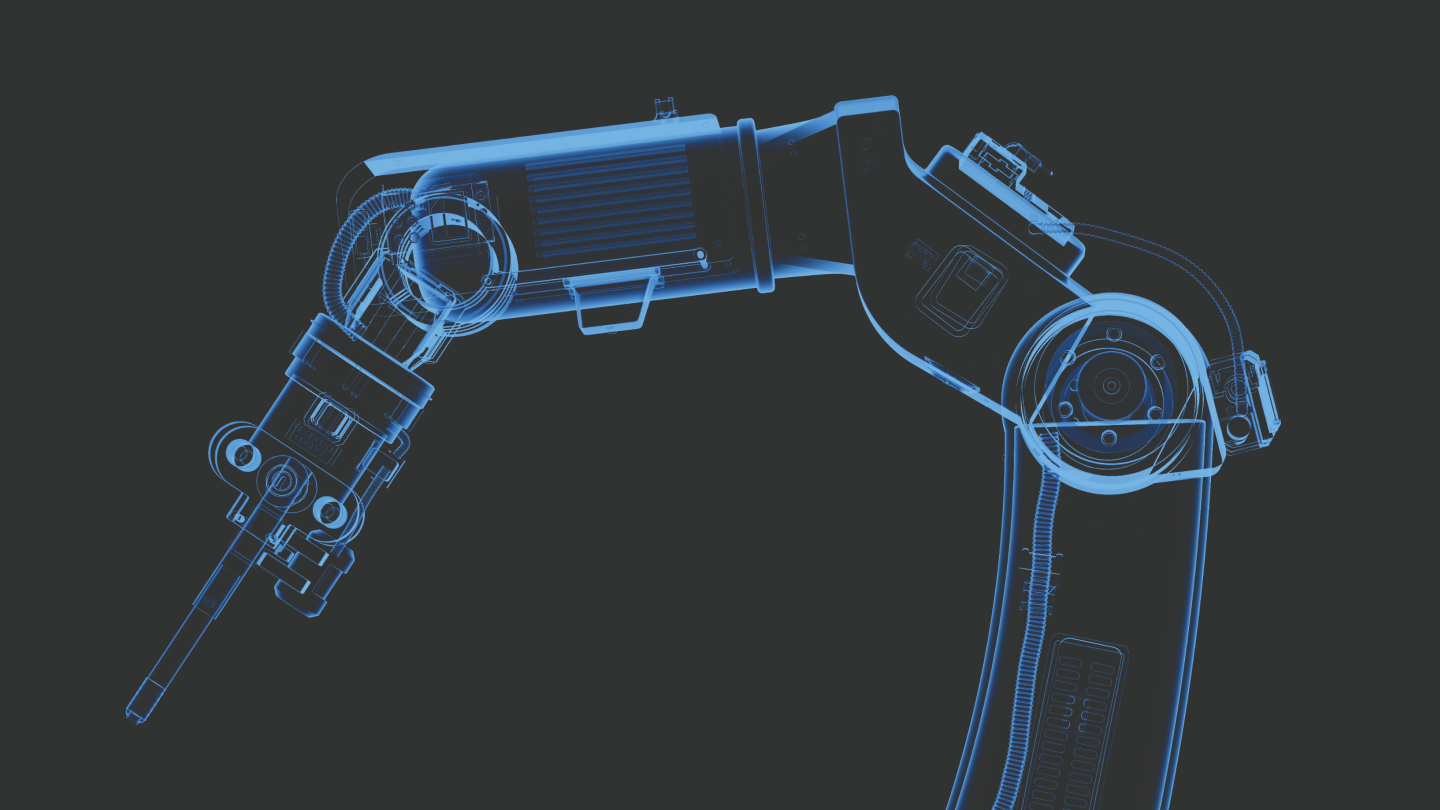
VGSTUDIO MAXの自動化機能:
- 一連のパーツのスキャン、または一度に複数のパーツを含むスキャンにきわめて有用です。
- エラー発生の可能性を減らします。
- 様々なパーツの検査結果を比較することが可能となります。
- オブジェクトの最初のスキャンから、オブジェクトから生成する必要のある結果に至るまでに必要な時間を短縮します。
- 手動のワークフローに含めるか、完全な検査を処理することができます。
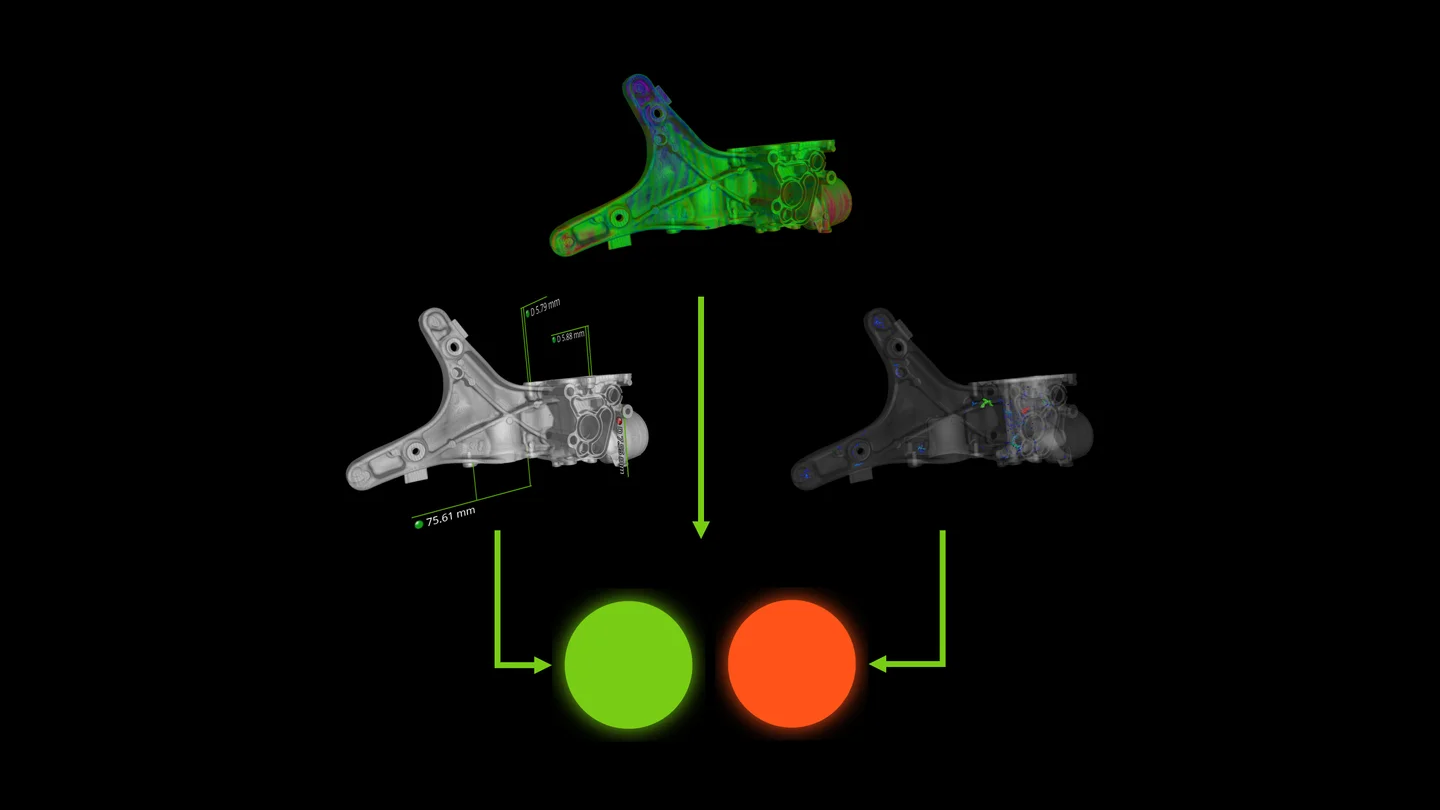
テンプレートには、個々の解析と測定の許容値の結果について、検査対象のパーツの品質を説明する単一の状態に組み合わせる方法に関するルールが含まれています。
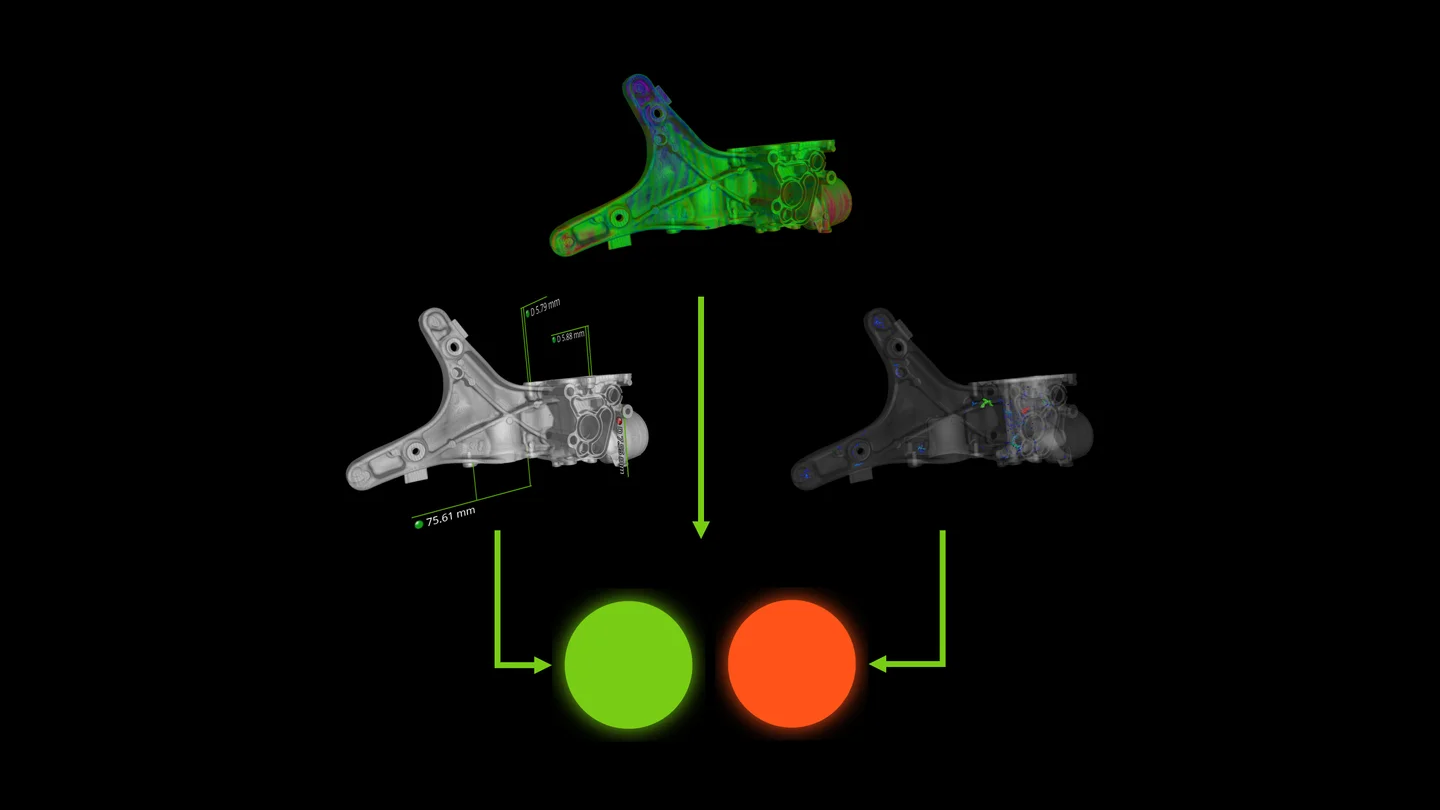
テンプレートには、個々の解析と測定の許容値の結果について、検査対象のパーツの品質を説明する単一の状態に組み合わせる方法に関するルールが含まれています。
解析と測定は、VGSTUDIO MAXのパーツ検査の中心的な作業となります。解析は主に、、設定した特定のパラメータ、実行するパーツの領域、結果値に適用する許容誤差によって定義されます。座標計測の結果は、スキャンしたパーツに参照ジオメトリをフィッティングし、ジオメトリの寸法と許容誤差を導出することによって定義されます。解析および測定データを再利用可能にするため、パラメーター、許容誤差、その他の設定などをテンプレートに組み合わせることができます。
テンプレート:
- 定義された解析と測定値を書き出して 再利用できます。
- セットアップされたパーツでまったく同じ結果を再現するために必要なすべてのものが含まれており、同様のパーツの様々なスキャンに適用して、比較可能な結果データを作成できます。
- 個々の解析と測定の許容値の結果について、検査対象のパーツの品質を説明する単一の状態に組み合わせる方法に関するルールが含まれています。
- 自動生成された画像または注釈マーカーを介して結果のどの部分を強調表示する必要があるかどうかなど、結果を可視化する方法のルールを含めることが可能です。
- 単一パーツ内の同様の領域にコピーすることで、パターンを用いて反復する特徴を評価できます。
- マクロまたは検査計画の一部として、手動または自動によって適用することが可能ます。
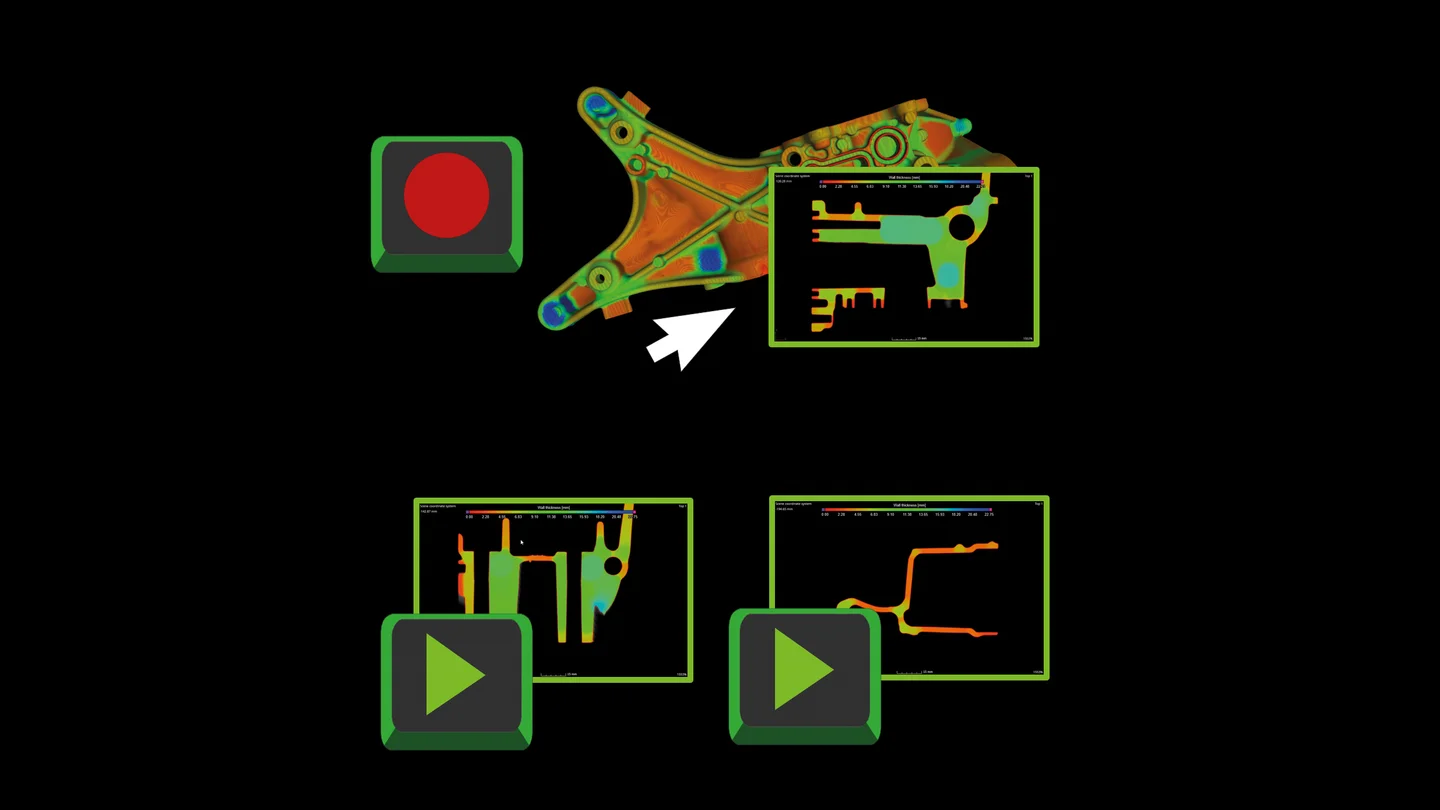
マクロでVGSTUDIO MAXが提供する機能をおおむね自動化できます。
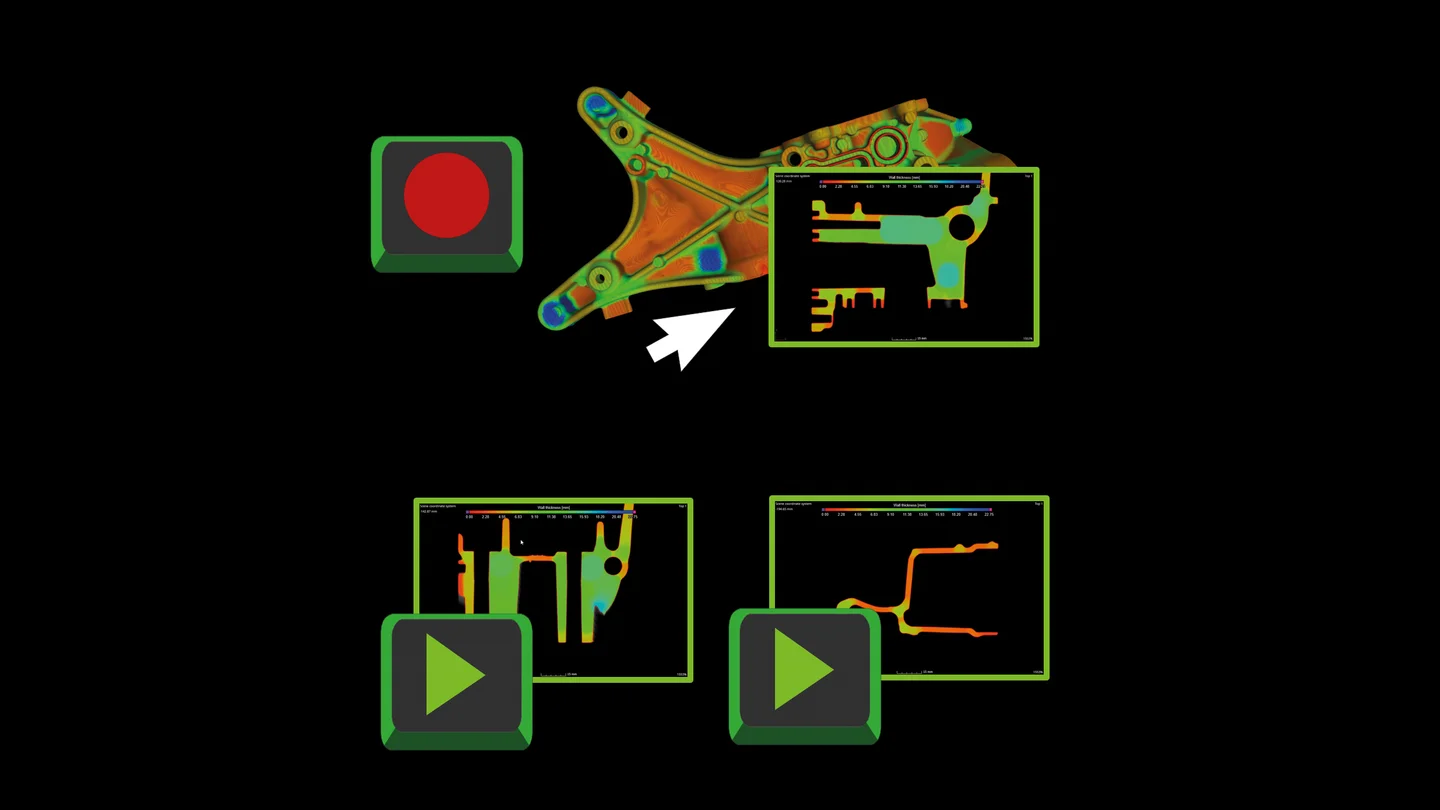
マクロでVGSTUDIO MAXが提供する機能をおおむね自動化できます。
同じ手順を同じ順序で異なる時間に繰り返すような場合は、マクロ機能がとても有用となるでしょう。面の測定、解析、または別の形式への変換についても、一度設定すればVGSTUDIO MAXの起動毎に便利なマクロ機能をご利用いただけます。マクロでは、ソフトウェアにて各操作を記録、保存できるため、さまざまなプロジェクトにそのデータを適用できるほか、アプリケーションの再起動後でもデータ利用が可能となります
マクロ:
- VGSTUDIO MAXが提供する機能をおおむね自動化することができます。
- 一定の操作のほか、その操作が適用されたオブジェクト、またはその操作で作成されたオブジェクト、さらには実行中に読み取りまたは書き込みされたファイル情報などを保存することが可能です。
- ソフトウェアとのユーザーインタラクションを記録するだけで、直感的に作成できます。また、ボタンを押すだけで再生も可能です。
- 半自動または完全自動ワークフローの構成要素となります。
- 個々のプロジェクトから独立しており、アプリケーションの再起動後もデータが保持されます。
- 専用のツールで管理され、マクロの結合、短縮、追加も可能です。
- 標準化のために同僚スタッフとデータ共有することができます。
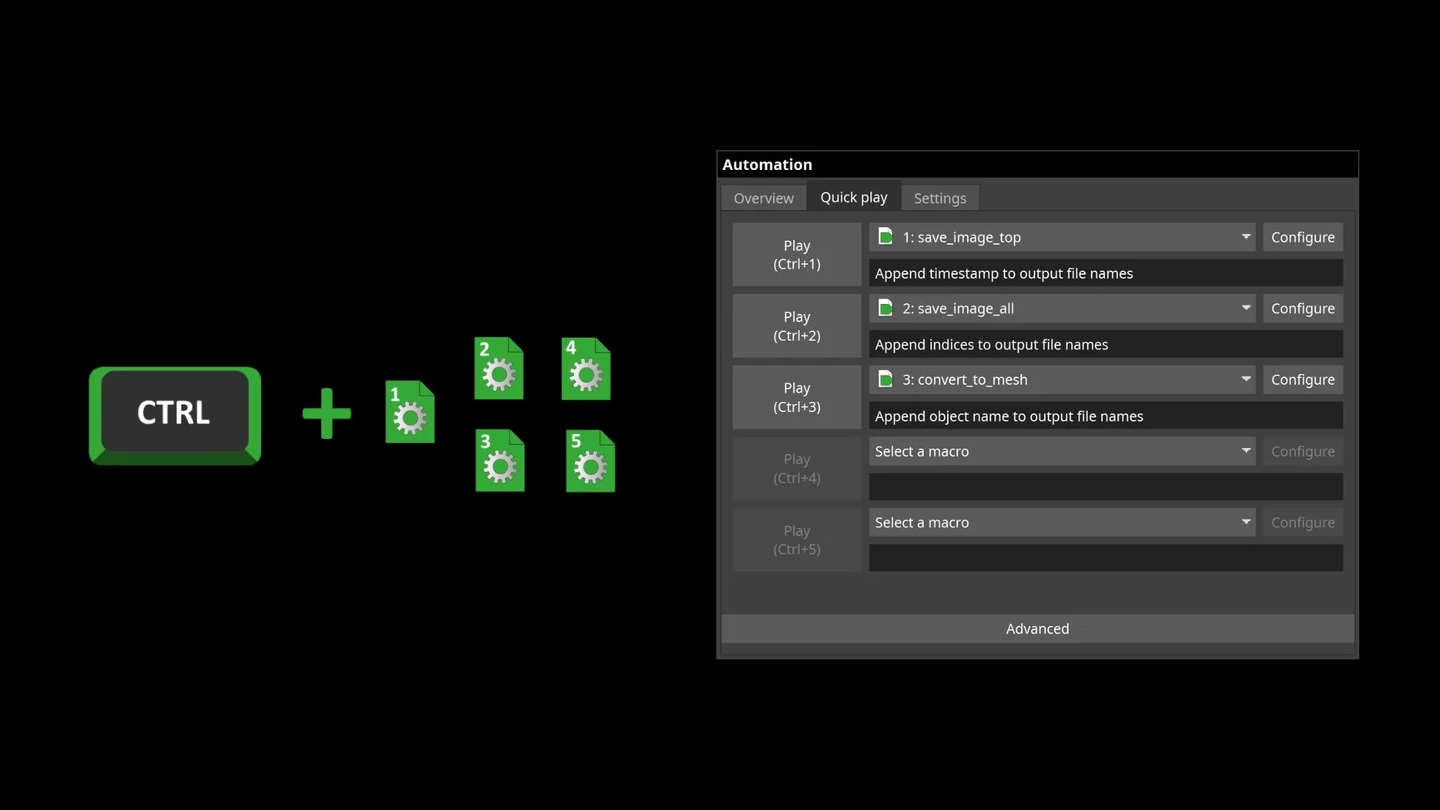
マクロのクイック再生では、ボタンを押すだけでいつでも記録した任意の機能にアクセスできます。
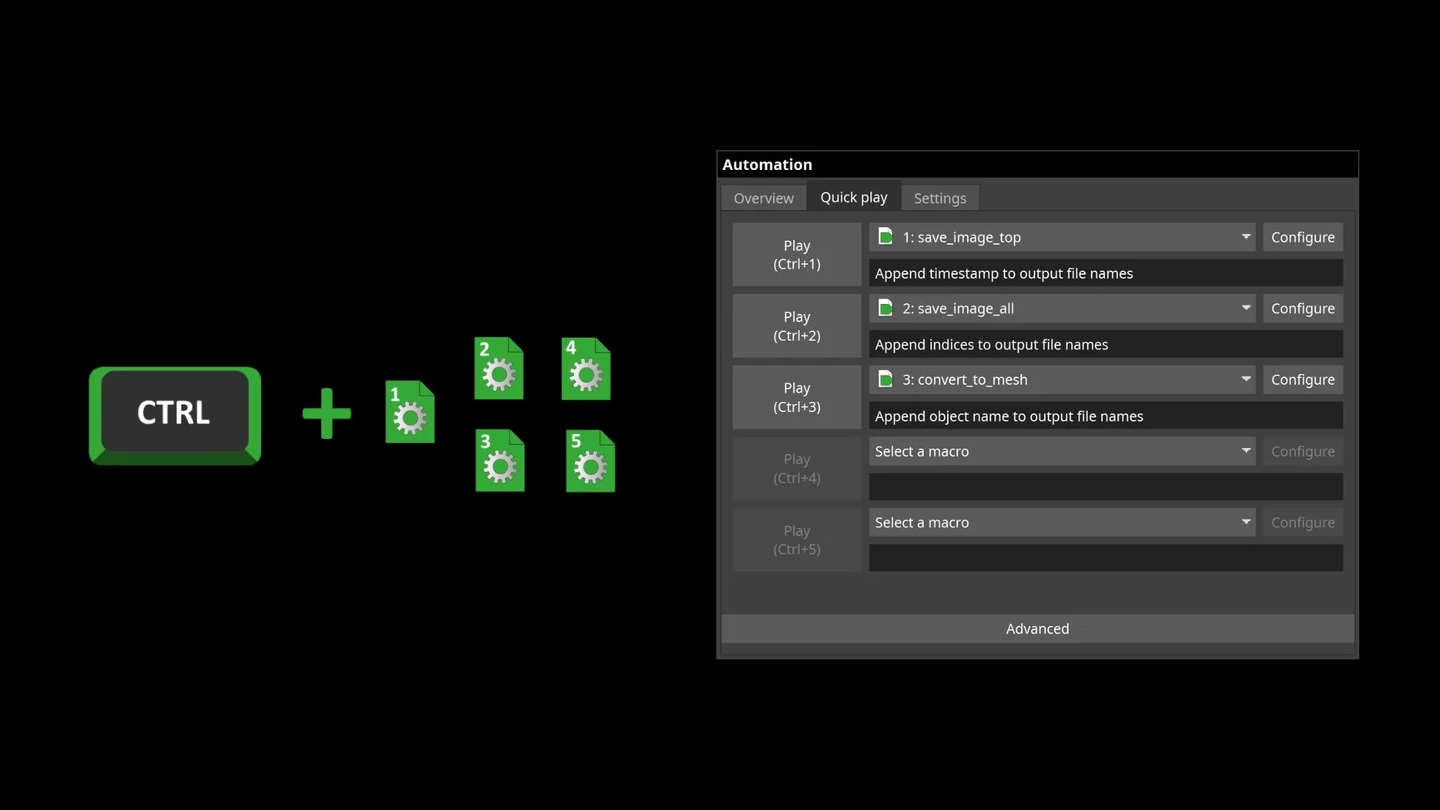
マクロのクイック再生では、ボタンを押すだけでいつでも記録した任意の機能にアクセスできます。
ワークフローをさらに合理化するために、マクロを特定のキーボードショートカットに割り当て、マクロが出力する可能性のあるデータのルールを設定できます。
マクロのクイック再生:
- ボタンを押すだけで、いつでも記録した任意の機能にアクセス可能です。
- アプリケーションの再起動後も構成が保持されるため、すぐに日常のワークフローとして利用できます。
- オプション選択により、出力ファイルに適切な名前を付けることで、以前に作成したデータとの競合を回避することができます。例えば、変換および書き出されたメッシュでは、ディスクに保存した際に元のボリュームの名前が自動的に付けられますが、保存画像にタイムスタンプを追加するだけでオブジェクトの一連の異なるビューを簡単に作成することが可能です。
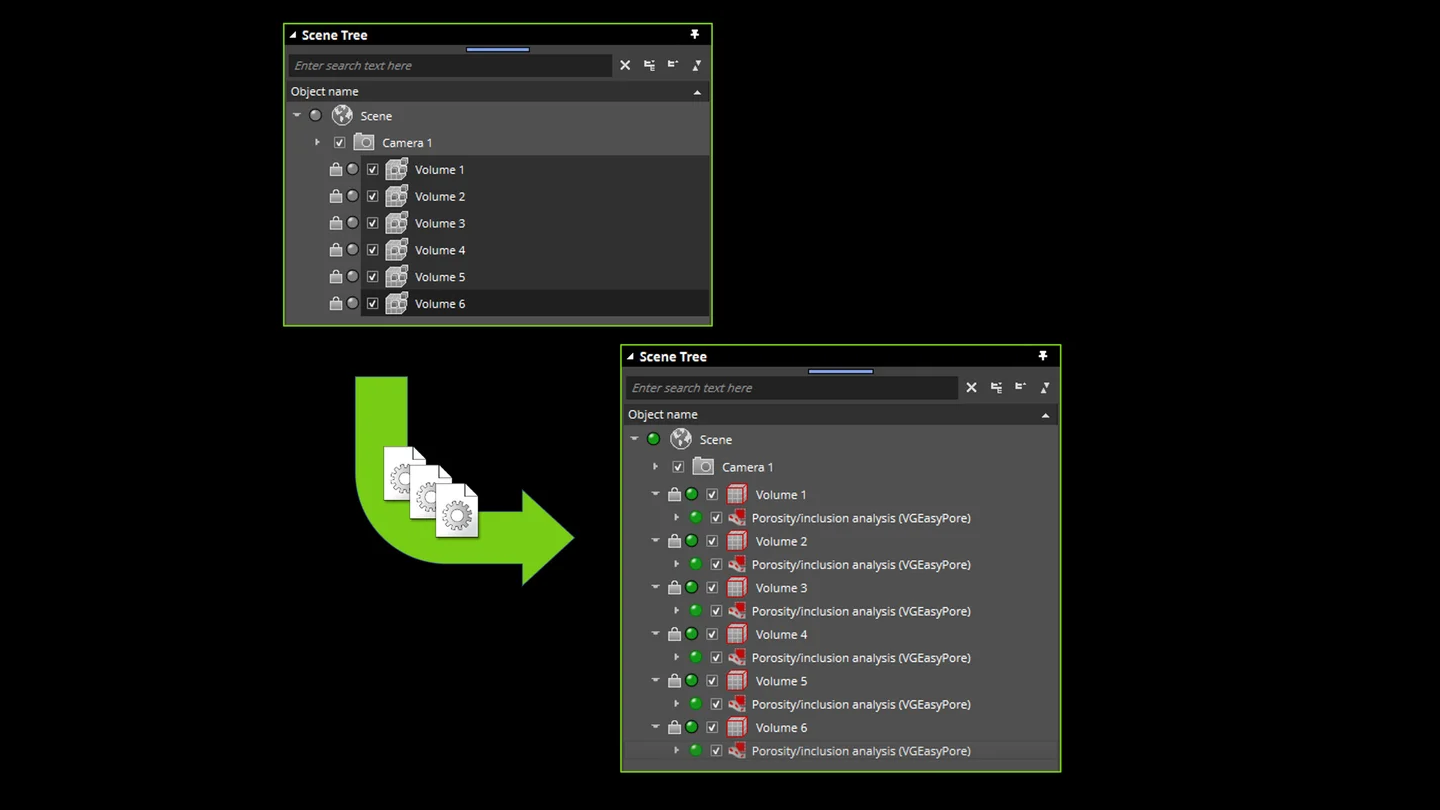
マクロのマルチ適用により、同じスキャンの一部であった同様の部分を同じ方法で処理できます。
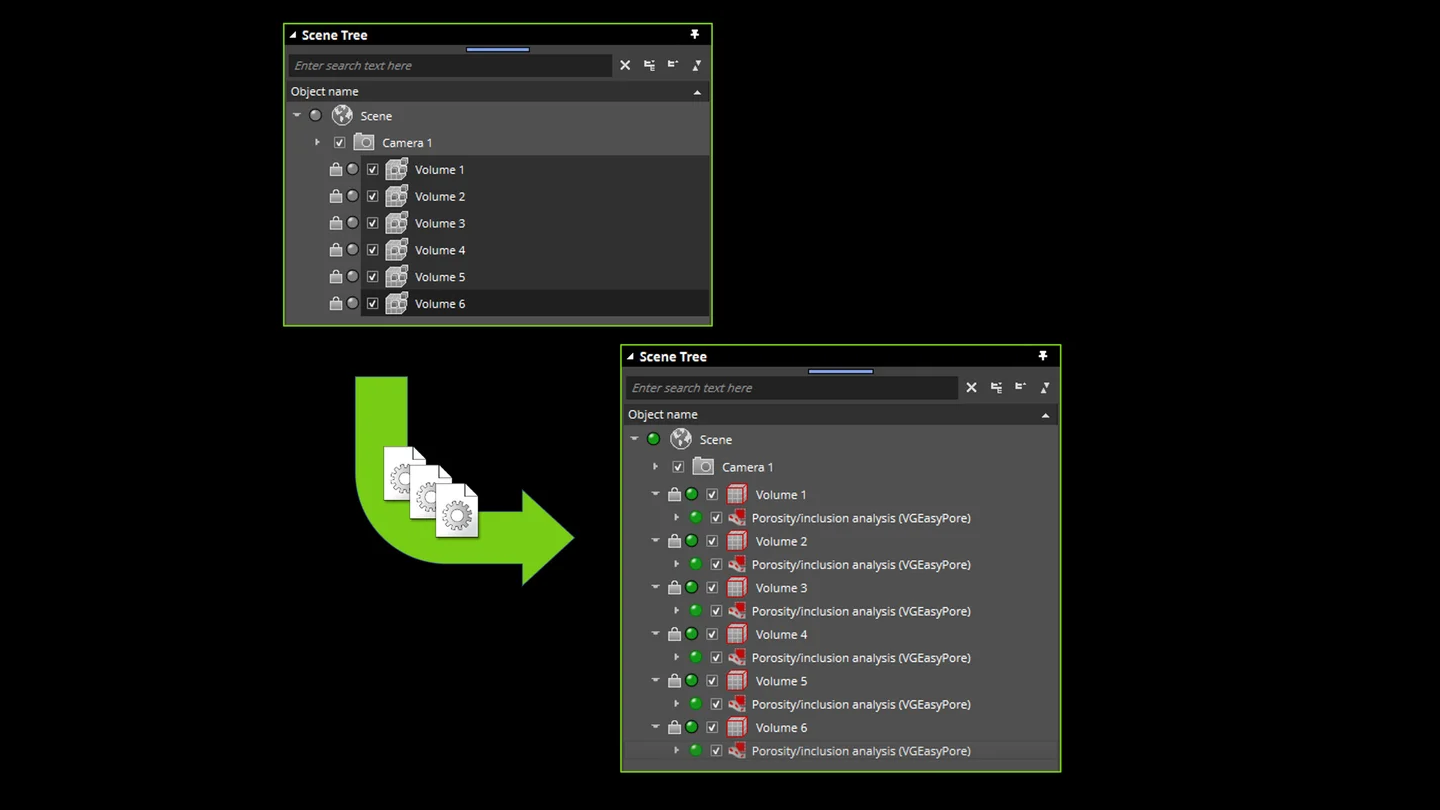
マクロのマルチ適用により、同じスキャンの一部であった同様の部分を同じ方法で処理できます。
特に小さなオブジェクトを扱う際に、プロジェクト内に同じタイプのオブジェクトが複数ある場合があります。通常、1つに適用される操作を他のすべてに適用するなど、これらの異なる部分を同じように扱うことは理にかなっています。
マクロのマルチ適用:
- 同じスキャンの一部であった同様の部分を同じ方法で処理できます。
- 単一のピースに対して実行する操作を記録し、それらをシーン内の残りのピースに自動的に適用できるようにします。
- 適切な命名戦略を提供することにより、生成される出力が以前に作成されたファイルと競合しないことを確認できます。
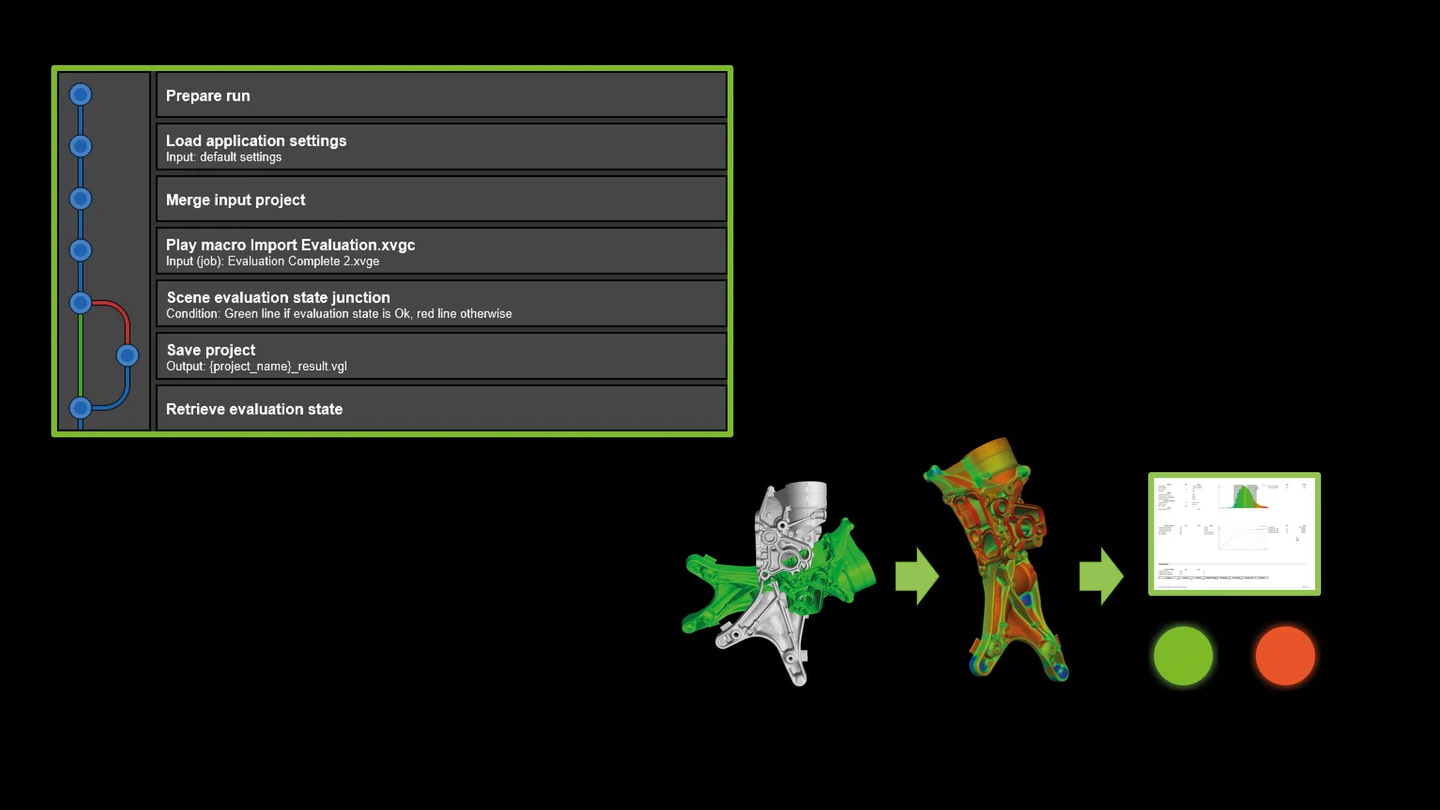
検査計画 では、入力スキャンからパーツの最終許容値ステータス、レポート、その他の種類の結果までの完全なパスが書き込まれます。
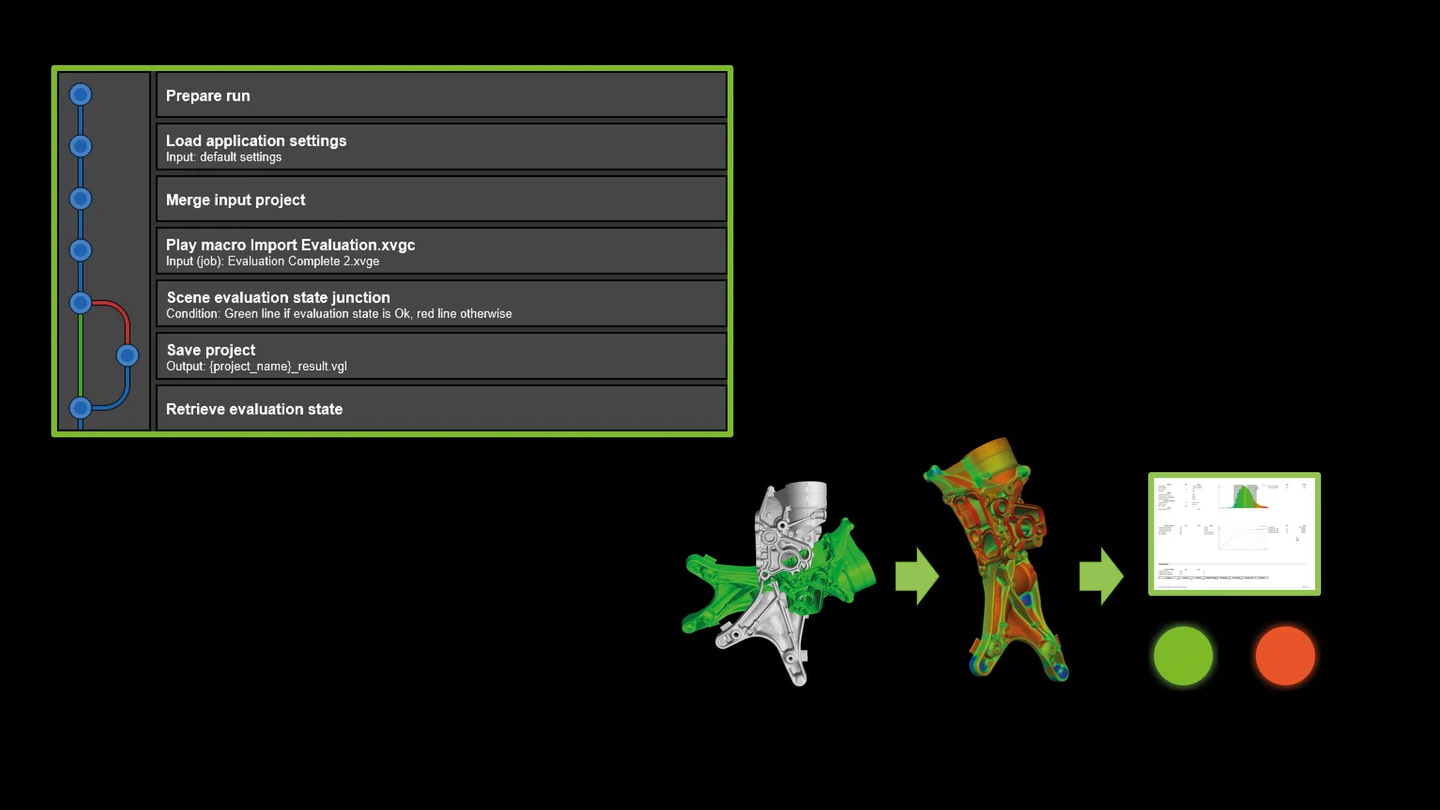
検査計画 では、入力スキャンからパーツの最終許容値ステータス、レポート、その他の種類の結果までの完全なパスが書き込まれます。
マクロ、解析、測定計画、および参照メッシュやレポートレイアウトなどの追加の依存関係を組み合わせて、自動化に利用できるスタンドアロンの検査計画を作成できます。
検査計画:
- 入力スキャンからパーツの最終許容値ステータス、レポート、またはその他の種類の結果までの完全なパスを記述します。
- プロジェクトのバッチに計画を適用することにより、一連のパーツを簡単に検査できます。
- 検査対象パーツのメタ情報に応じて入力ファイルを選択できるため、検査プロセスによってパーツの詳細に対応可能となります。例えば、ツールの様々な穴に由来するパーツは、様々な参照ジオメトリを基に登録または解析される場合があります。
- 中間結果に応じて操作を実行できます。例えば、検査に合格したパーツはレポートのみを保存し、不合格のパーツは後で詳細な解析を行うために完全なスキャンを保存できます。
- 自己完結型のVGinLINEジョブとして保存され、VGSTUDIO MAXで簡単にアーカイブ、共有、および適切な入力スキャンに適用できます。
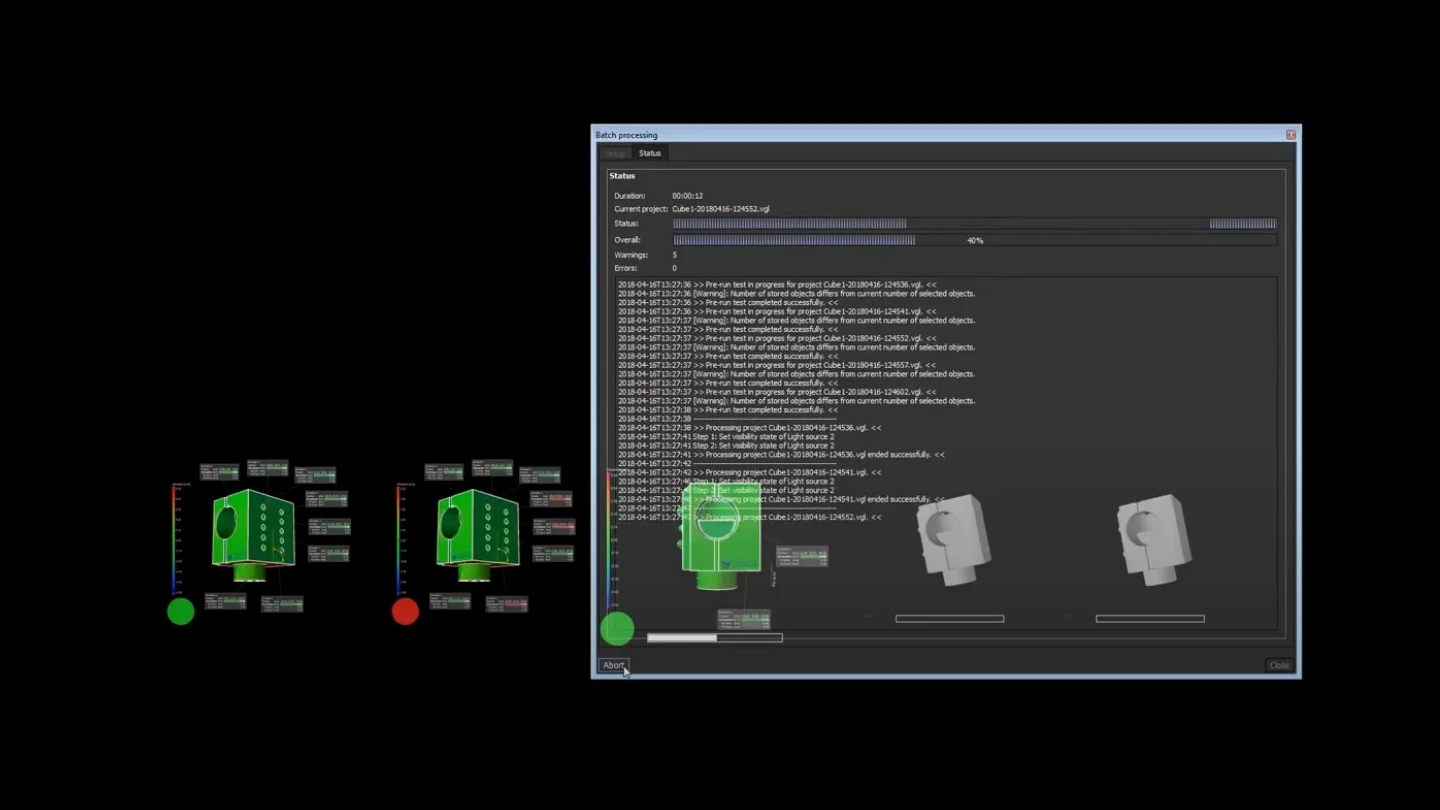
バッチ処理を用いれば、ユーザーが介入せずに、マクロまたはVGinLINEジョブを多数の入力プロジェクトに適用できます。
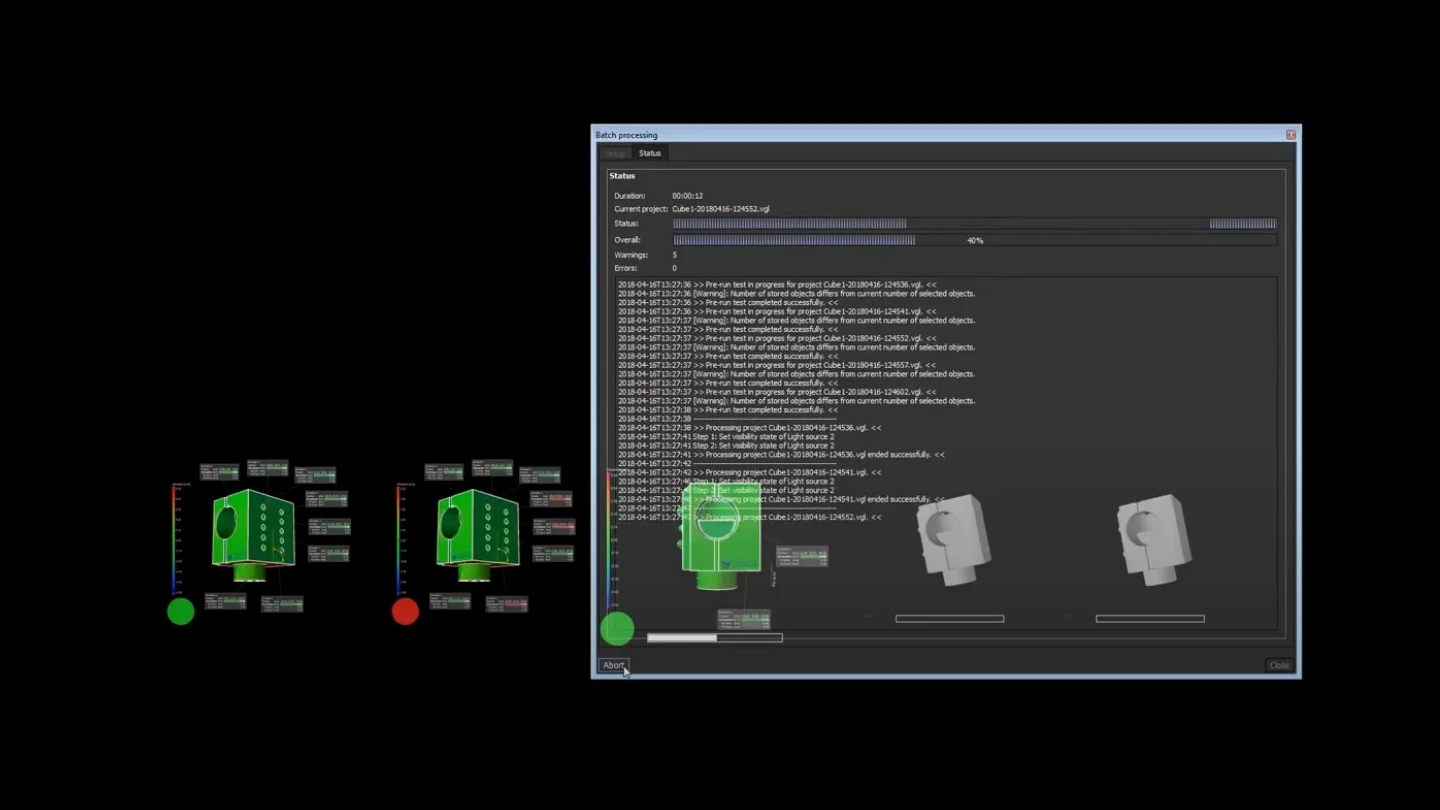
バッチ処理を用いれば、ユーザーが介入せずに、マクロまたはVGinLINEジョブを多数の入力プロジェクトに適用できます。
一連のスキャンを行う場合はバッチ処理による自動化が役立ちます。
バッチ処理で次のことが可能です。
- ユーザーの介入なしで、マクロまたはVGinLINEジョブを多数の入力プロジェクトに適用する。
- 便利で再現性のある方法でその後の手動処理のために、一連のパーツを準備する。
- 一連のパーツを完全に検査する。
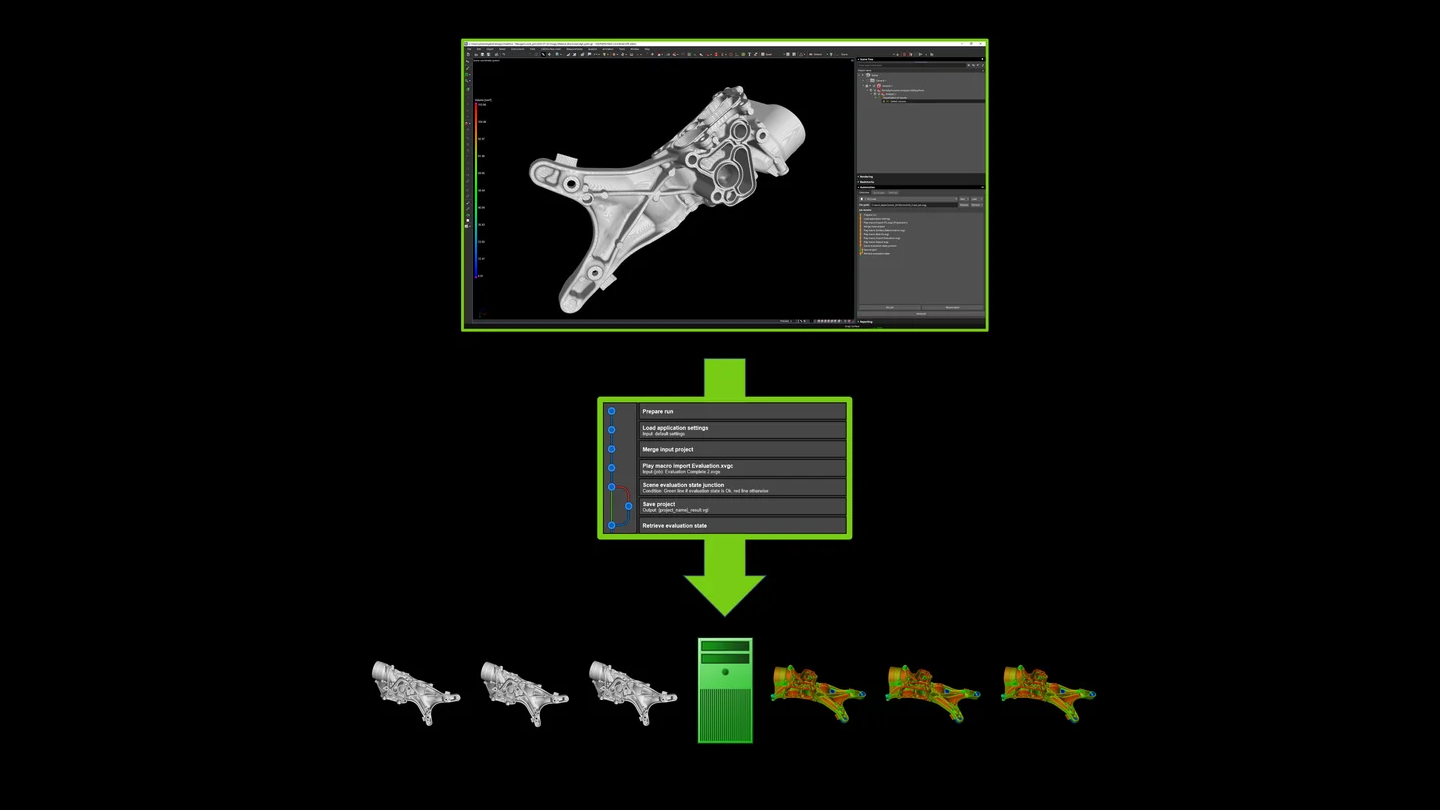
VGinLINEでの受信CTデータ検査を完全に自動化できます。
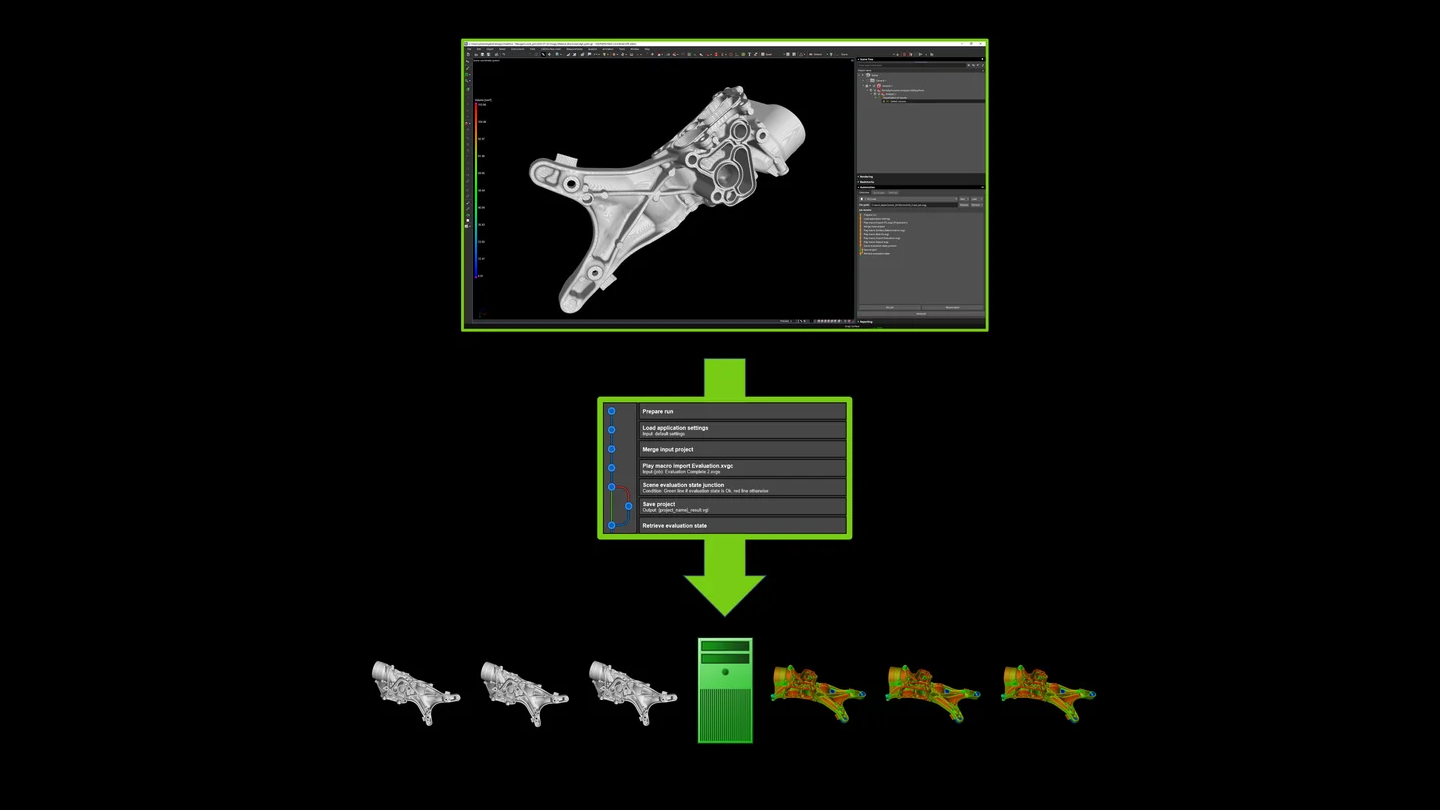
VGinLINEでの受信CTデータ検査を完全に自動化できます。
検査計画は、VGSTUDIO MAXで再現可能な結果を自動的に作成することを容易にするだけでなく、自律検査のためのボリュームグラフィックスのソリューションであるVGinLINEで検査プロセスを完全に自動化するための足がかりとなります。
VGinLINEで次のことができます。
- 着信CTデータの検査を完全に自動化できます。
- VGSTUDIO MAXで設定して使用した検査計画をシームレス に再利用できます。
- 入力または生成した出力データを自動的に処理できます。
- 合格/不合格の決定、完全な結果、または統計的プロセス制御のためのデータを渡すことにより、後続のシステムに接続できます。
同じパーツの反復検査で時間を節約し、エラー発生の可能性を抑制
1つのパーツ、1つのプロジェクトの複数のパーツ、または複数のプロジェクトにおける反復オペレーション時間を短縮
手動から半自動および完全自動の検査シナリオに簡単に移行