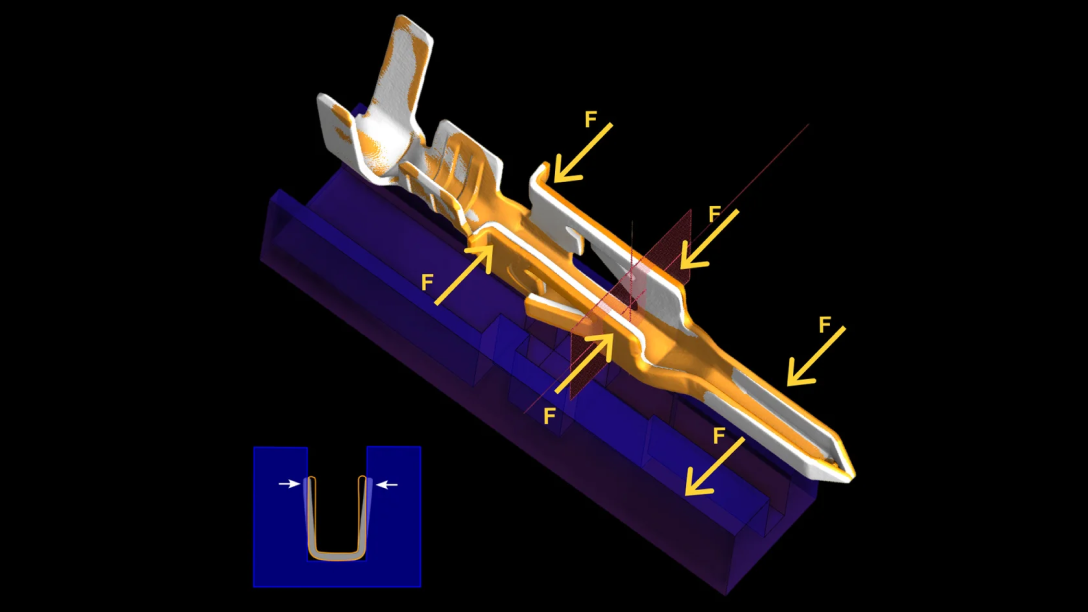
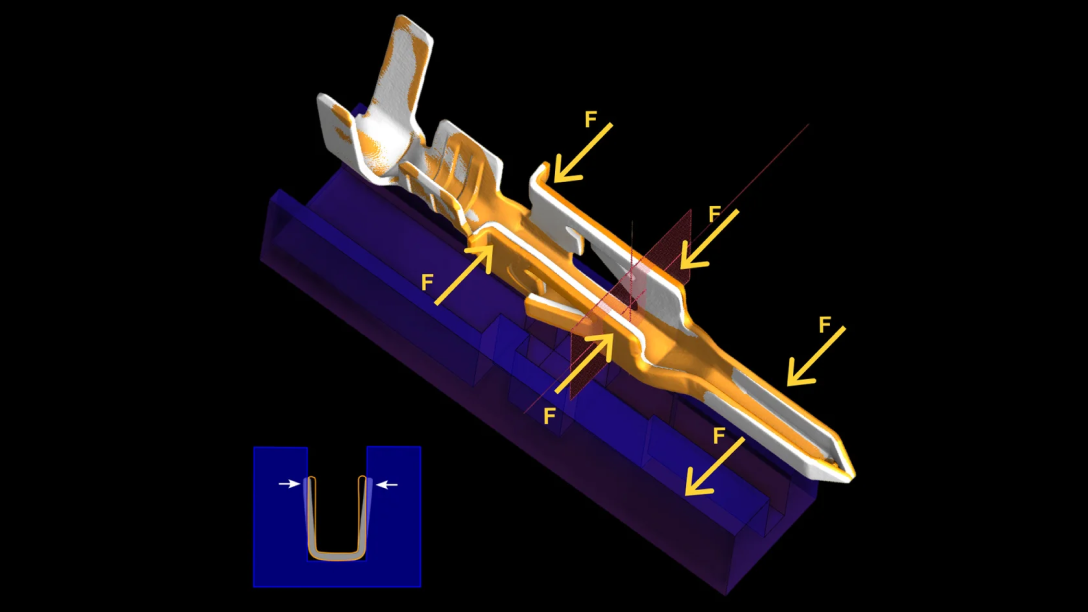
Fixture simulation of a deformed, non-rigid part
- Simulate the fixturing of a deformed, non-rigid part within minutes
- Save time and money: no custom-made fixture gear required
- All you need is the CT scan of the force-free part and the related CAD model
- Define the fixture conditions and perform a fixture simulation directly in VGSTUDIO MAX
- Obtain a surface mesh of the simulated part
- Apply your established metrology workflow to the surface mesh of the simulated part in the virtually fixtured state
- Requires no simulation expertise
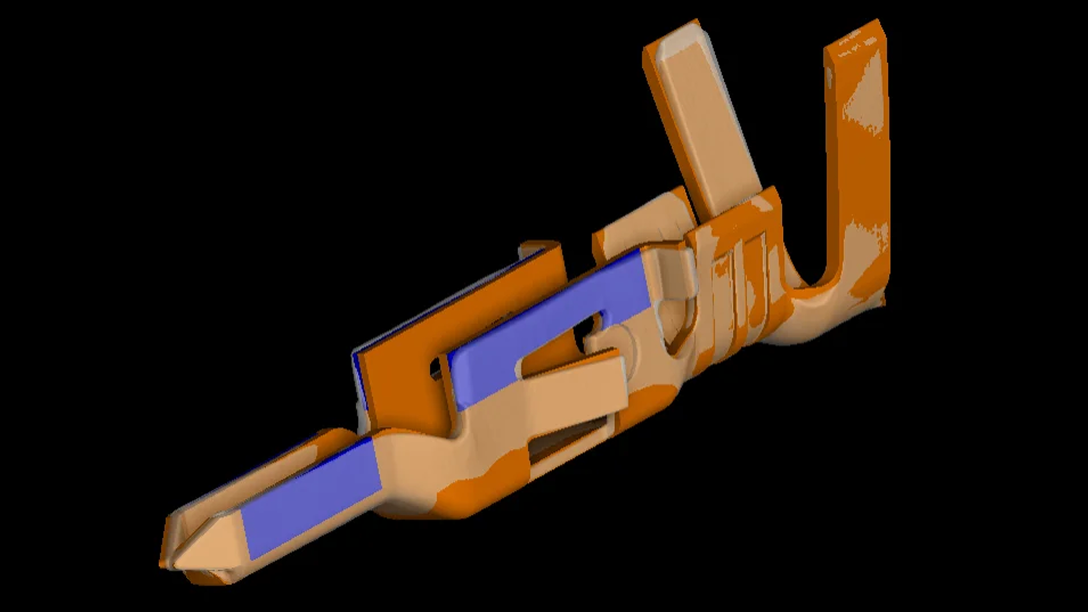
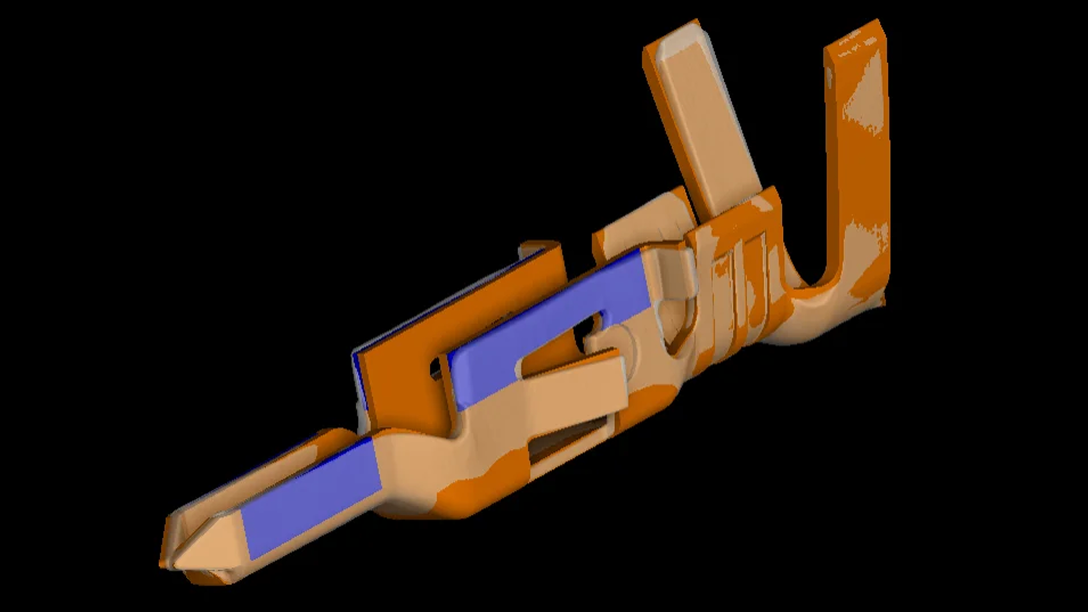
Defining the fixture conditions
- Defining the fixture conditions is as easy as drawing ROIs in VGSTUDIO MAX
- Mark the contact areas that would touch the fixture device on the CAD model or on the CT scan, using ROIs (blue)
- Lock or unlock degrees of freedom for the most realistic simulation (modeling of contact slip)
- The part will be clamped at the contact areas, while the rest of the object will deform according to a finite element simulation
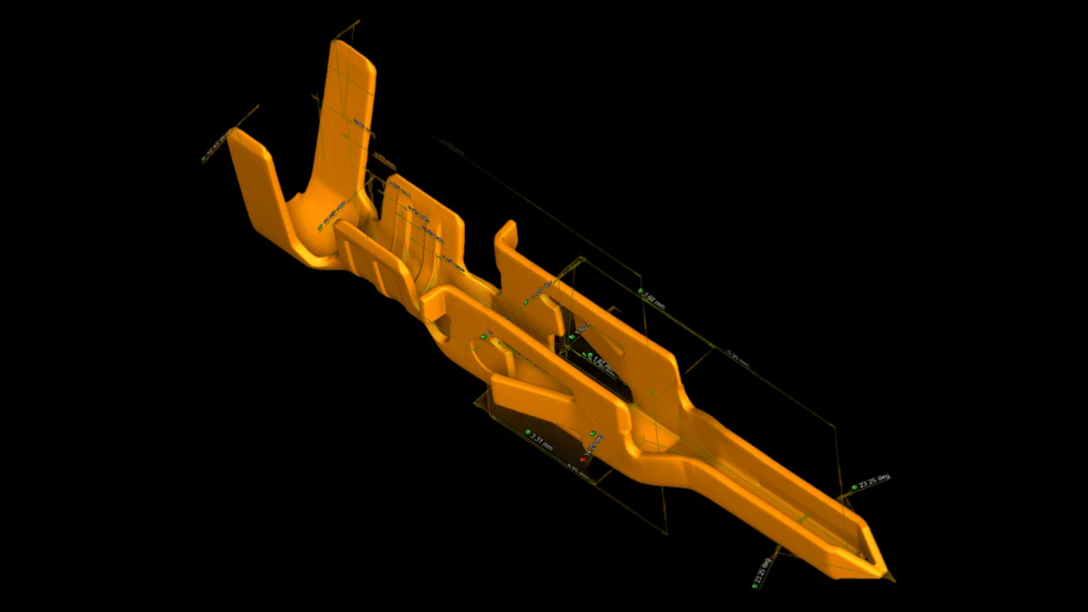
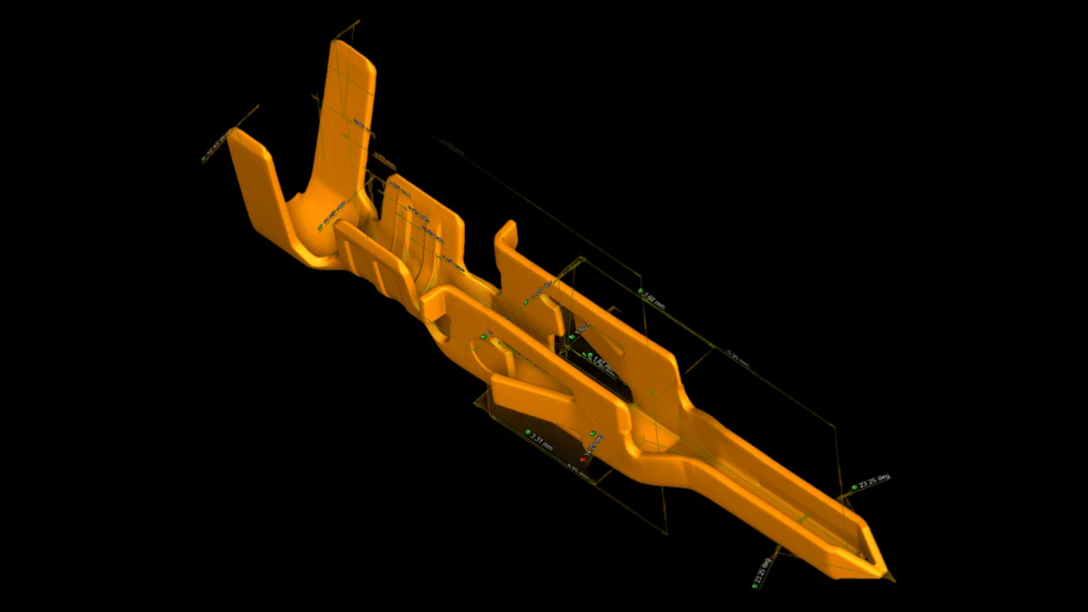
Quality assurance of the virtually fixtured part
- The virtually fixtured part is available as high-resolution surface mesh
- Perform QA tasks on it like on a native scan
- Apply the full range of VGSTUDIO MAX metrology features and analyses to qualify the simulated part
- If required, export the resulting high-resolution surface mesh as an STL mesh for further analysis in third-party software
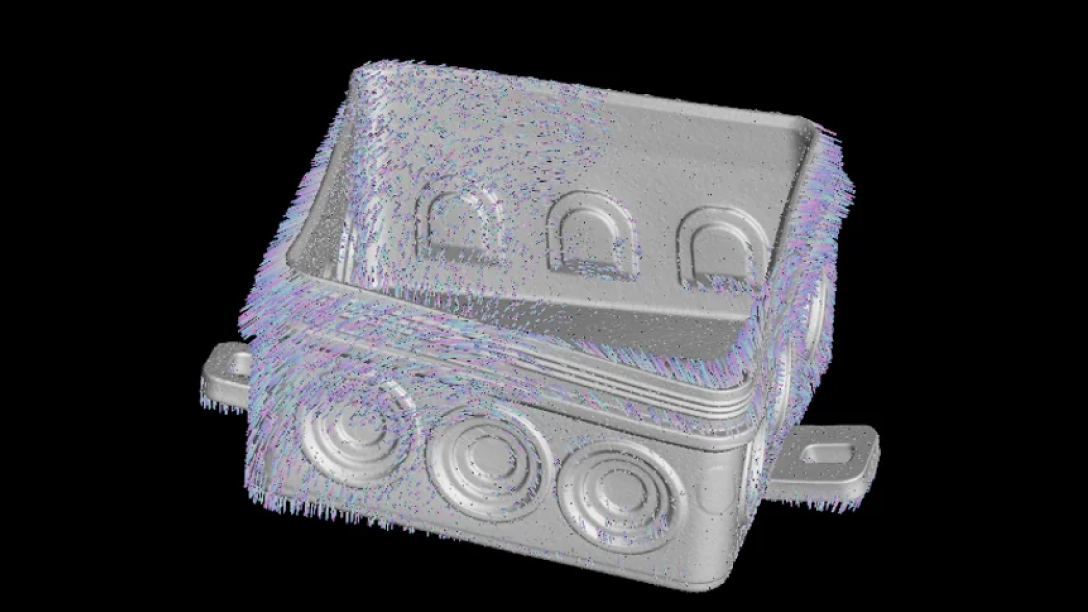
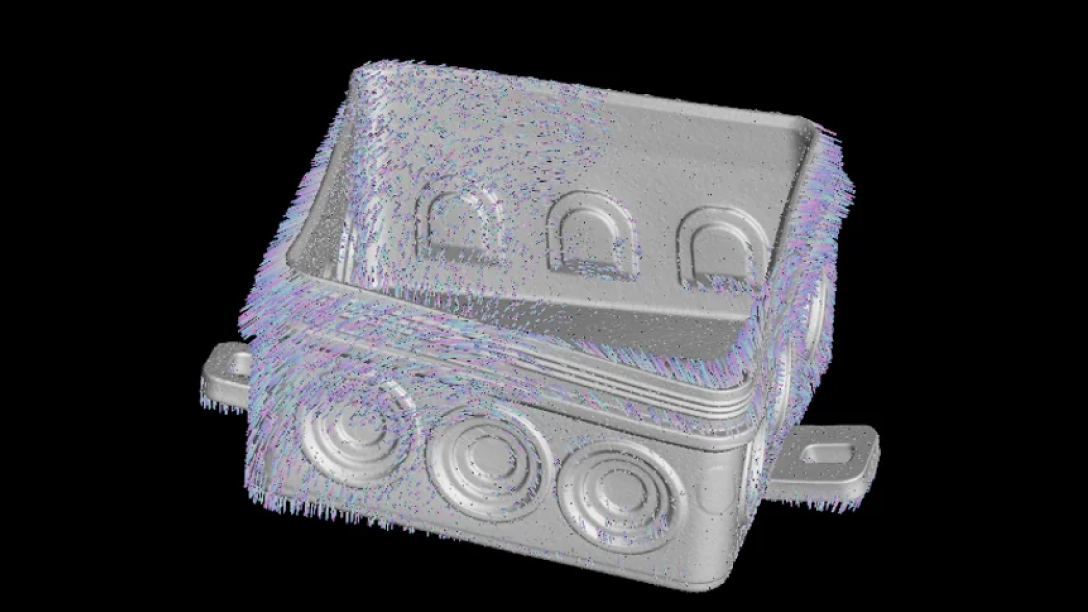
How it works
- A point-to-point correlation between CT scan and CAD model is the basis of the finite element simulation and will be established automatically
- The correlation is only relevant at the contact areas, where the part will be virtually clamped to the corresponding CAD surfaces through predefined displacement boundary conditions
- The rest of the part will deform according to the physical laws of elasticity
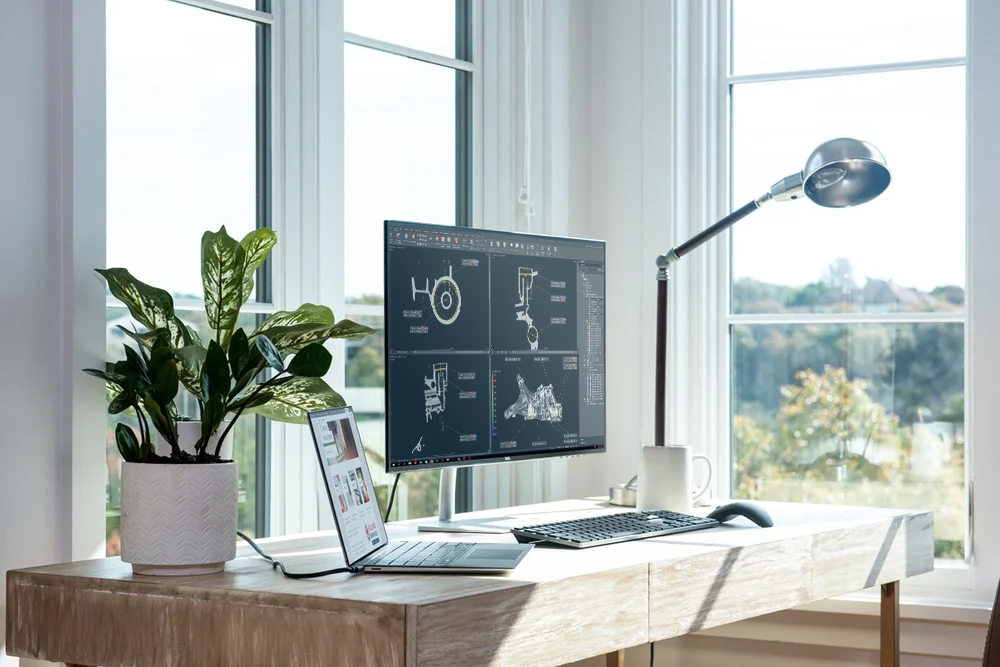
ADD-ON MODULES
Ready to expand your capabilities?
Contact us today—our team is ready to assist!
Request a quote