Generation of tetrahedral meshes
Volume meshes are widely used in simulations for mechanical, fluid, thermal, electrical, and other applications.
This module is:
- An easy-to-use tool to create accurate and high-quality tetrahedral volume meshes directly from CT scans for use in third-party FEM simulation software
- Based on subvoxel-accurate, locally adaptive surface determination*
- Based on algorithms that work directly on the volumetric data of the CT scan without creating an intermediate surface mesh, thus maintaining maximum geometrical accuracy
- Suitable for scans of mono-material and multi-material components or material probes
*Coordinate Measurement module required
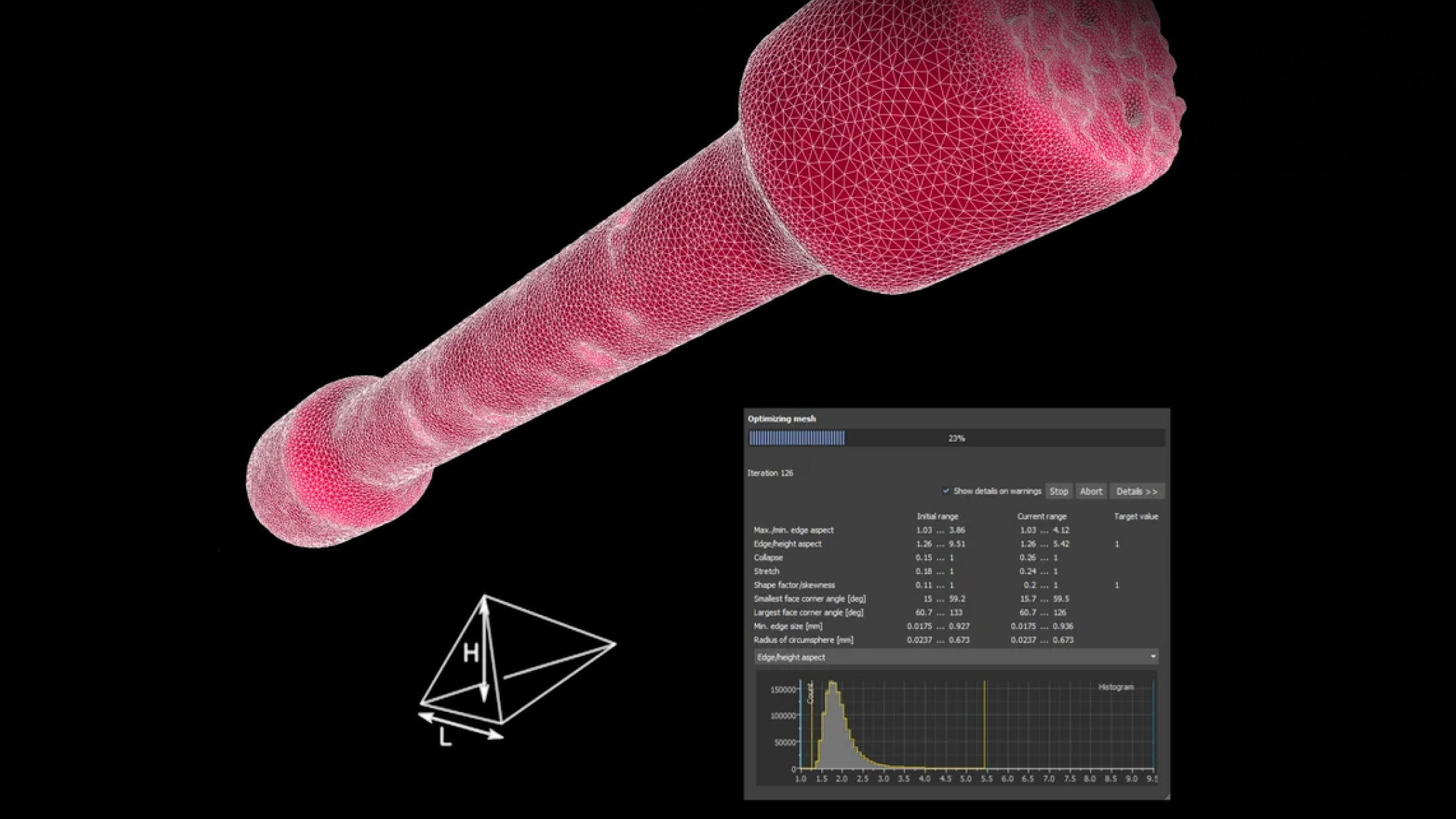
Control and improve the finite element (FE) mesh quality and use histograms to review and assess the mesh quality.
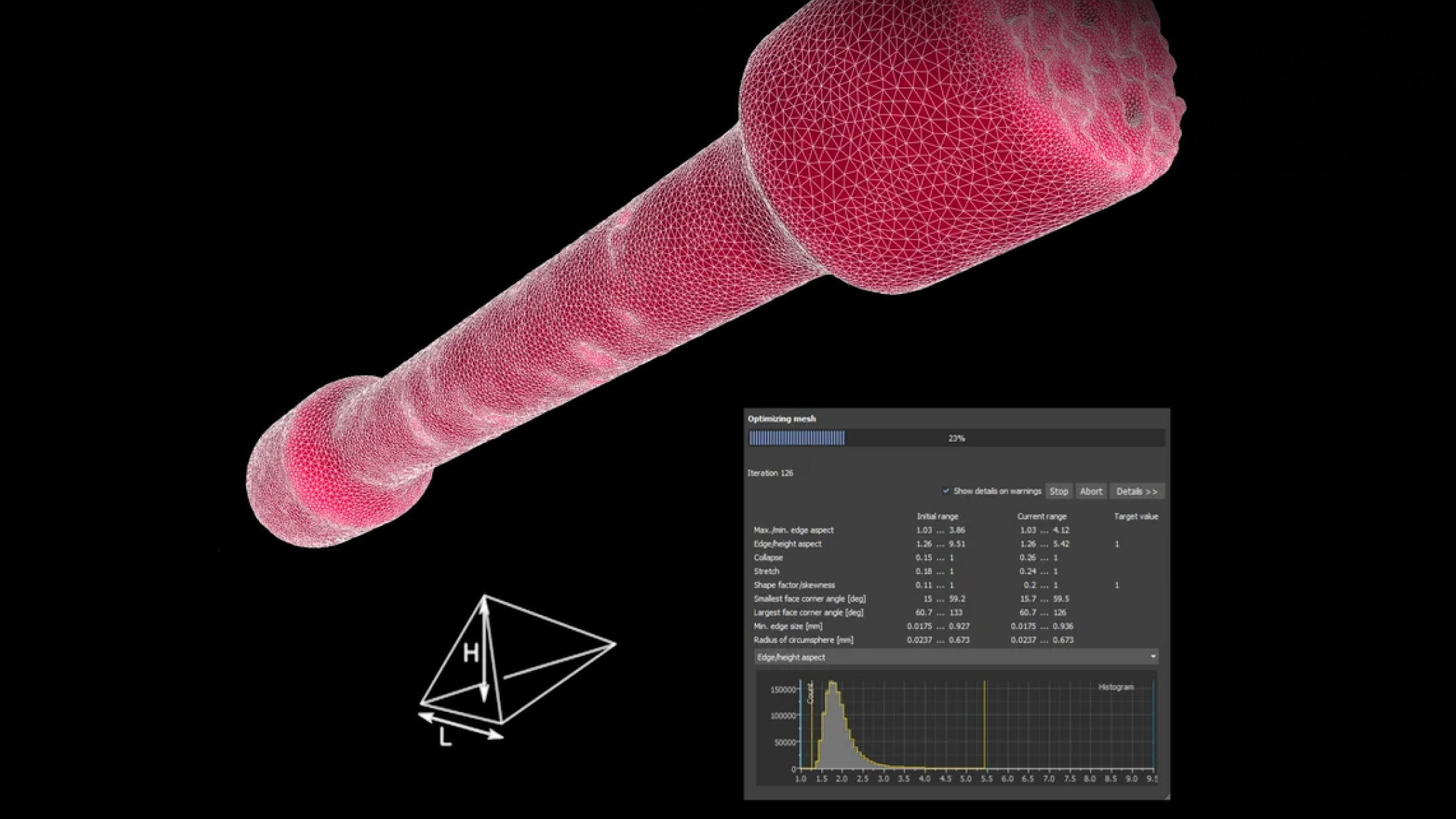
Control and improve the finite element (FE) mesh quality and use histograms to review and assess the mesh quality.
Optimisation of mesh parameters
You can control and improve the finite element (FE) mesh quality according to specific element quality requirements by setting target parameters for mesh optimisation.
Choose from one or more of the following criteria:
- max./min. element size,
- edge aspect,
- edge/height aspect,
- collapse,
- stretch,
- shape factor,
- smallest face corner angle,
- largest face corner angle,
- and min. edge size.
Histograms for each quality criterion and the ability to visualise the criteria in the mesh allow you to review and assess the mesh quality clearly.
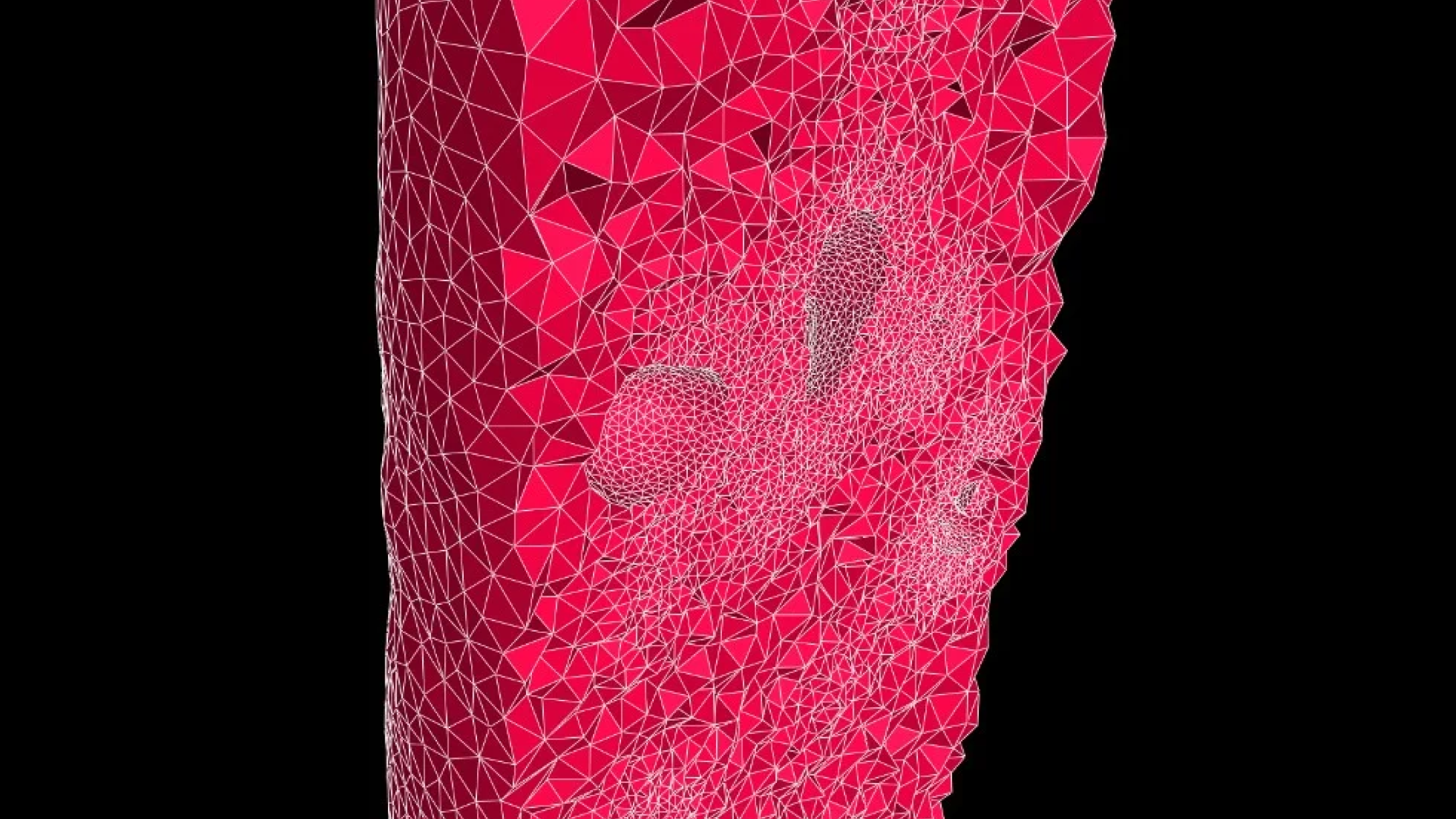
You can locally refine meshes in specified regions.
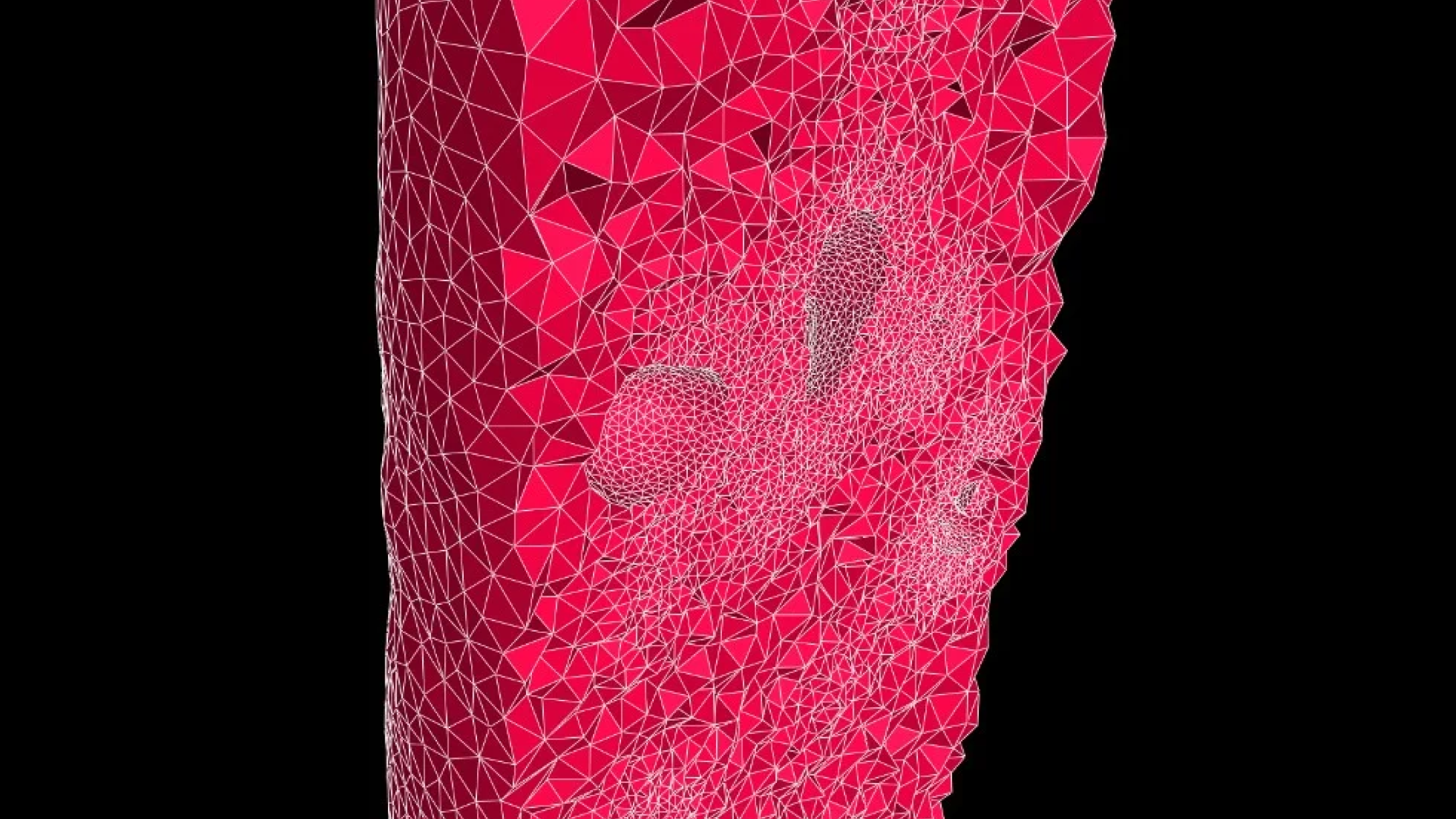
You can locally refine meshes in specified regions.
Local mesh refinement
For increased accuracy of the simulation results, you can locally refine meshes in specified regions while limiting the number of created elements. The familiar ROI tools in VGSTUDIO MAX ensure an efficient workflow.
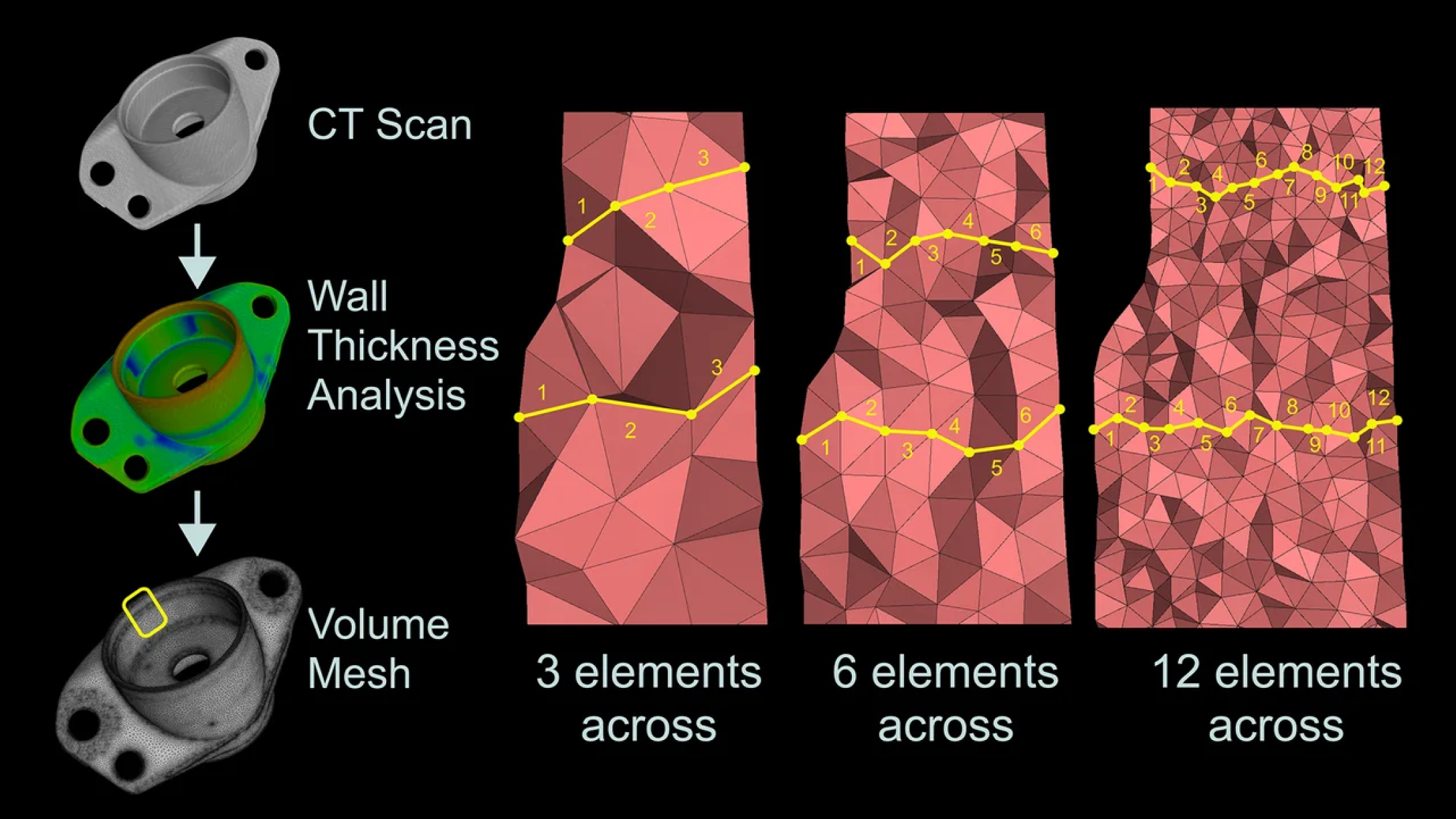
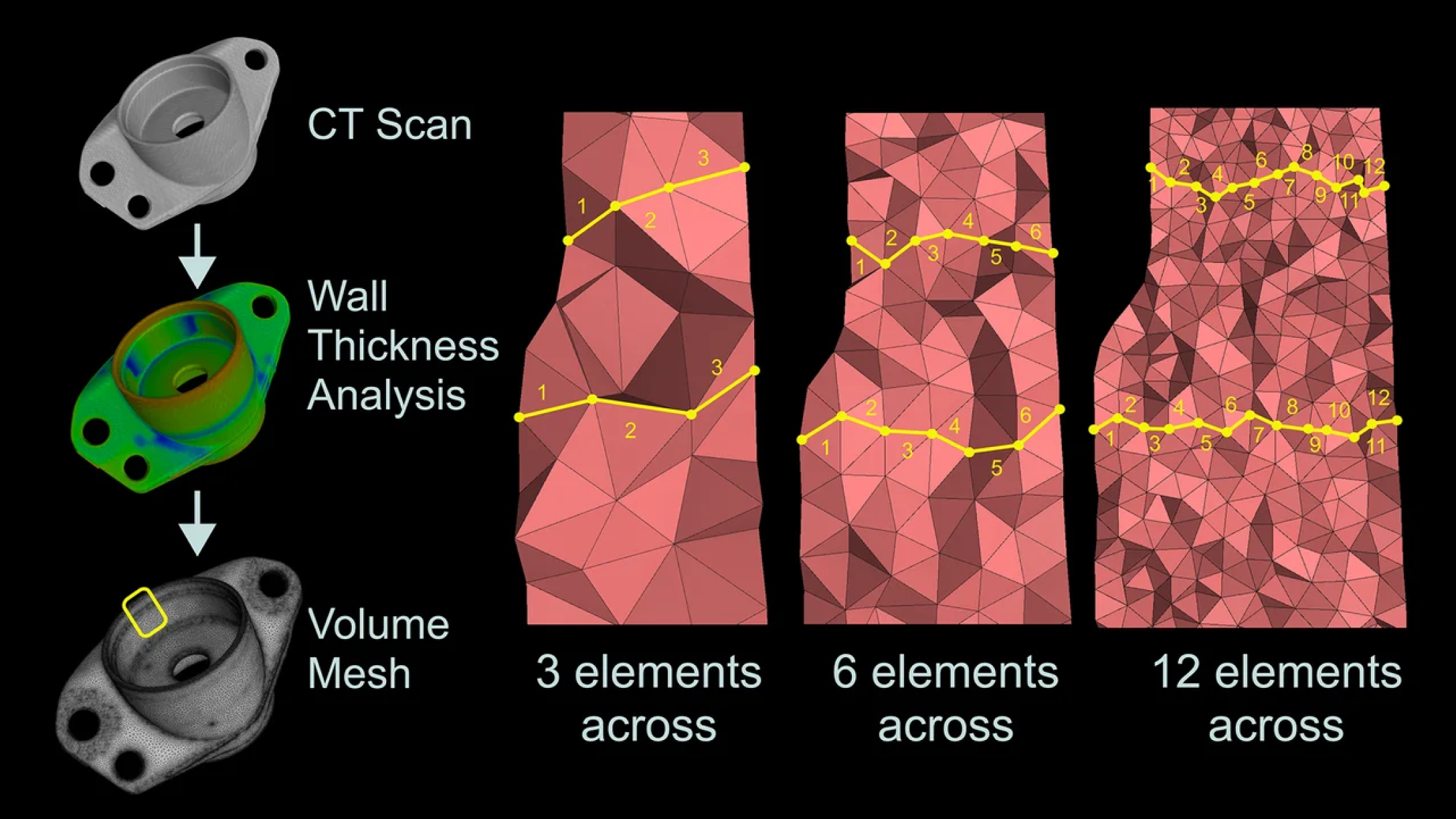
Upgrade in wall-thickness-based refinement
Meshing thin parts of a volume is now more accurate than ever. By specifying the number of tetrahedral elements, you can significantly enhance mesh fidelity.
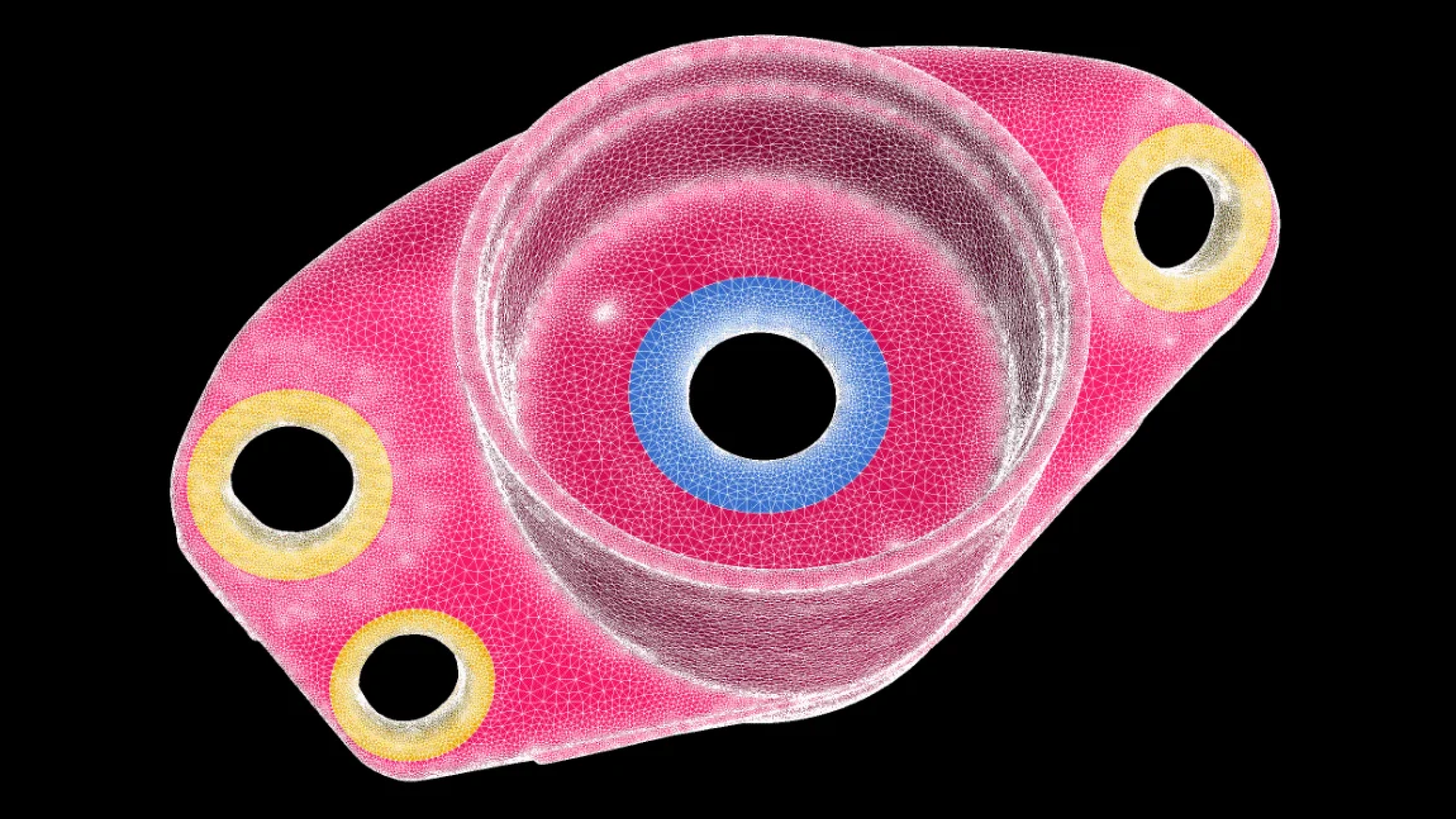
Define and export sets of tetrahedral elements, nodes, or facets based on specified regions of interests (ROIs).
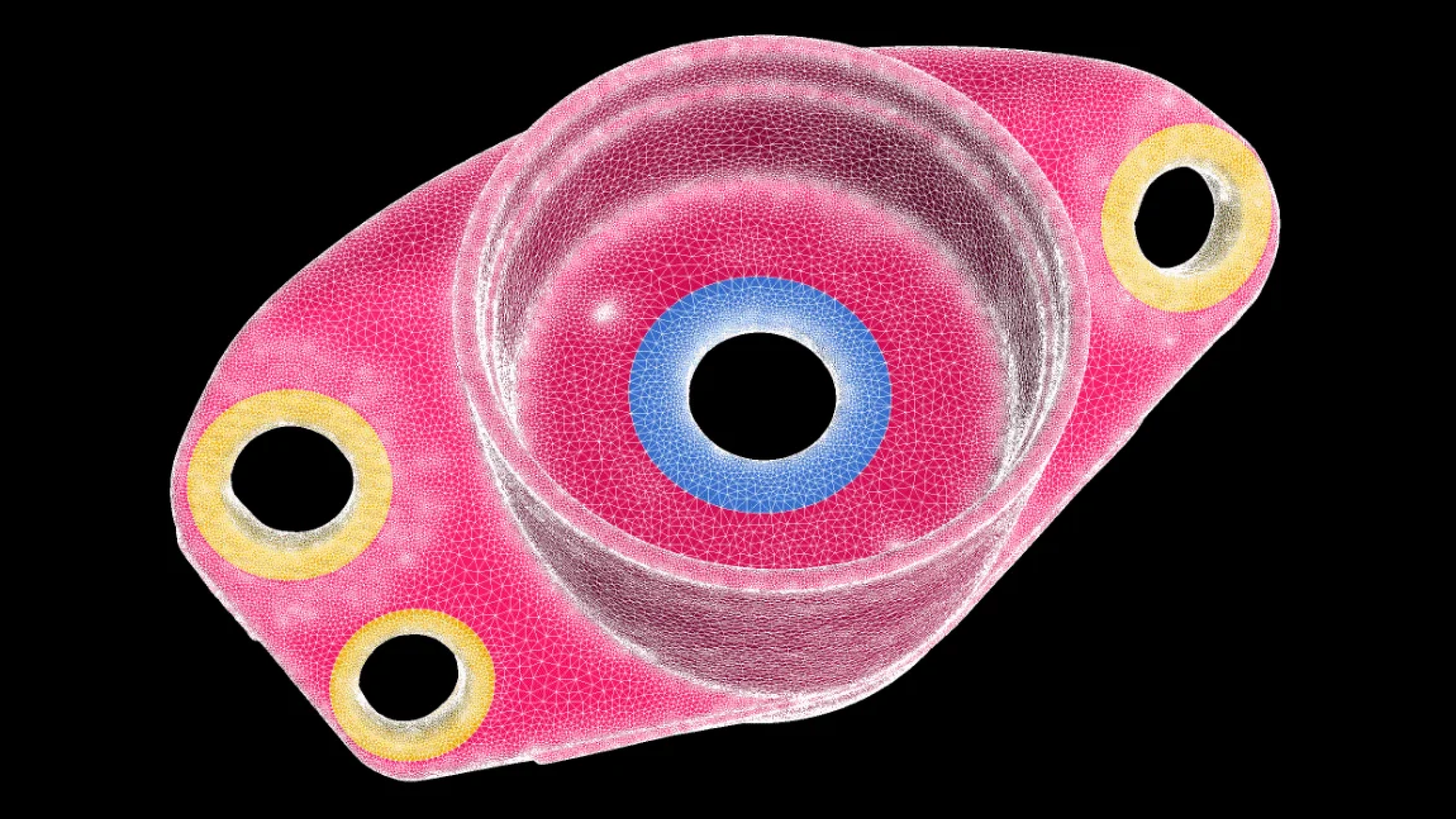
Define and export sets of tetrahedral elements, nodes, or facets based on specified regions of interests (ROIs).
FE entity sets
To prepare the efficient application of various boundary conditions, e.g., loads, fixations or contacts, in third-party FEM software, the Volume Meshing module allows you to define and export sets of tetrahedral elements, nodes, or facets based on specified regions of interests (ROIs). The created mesh will respect the outline of the ROIs. Defining FE entity sets on the CT data in VGSTUDIO MAX reduces a possible loss of geometrical information and ensures a high degree of geometrical accuracy after exporting it to third-party FEM simulation software.
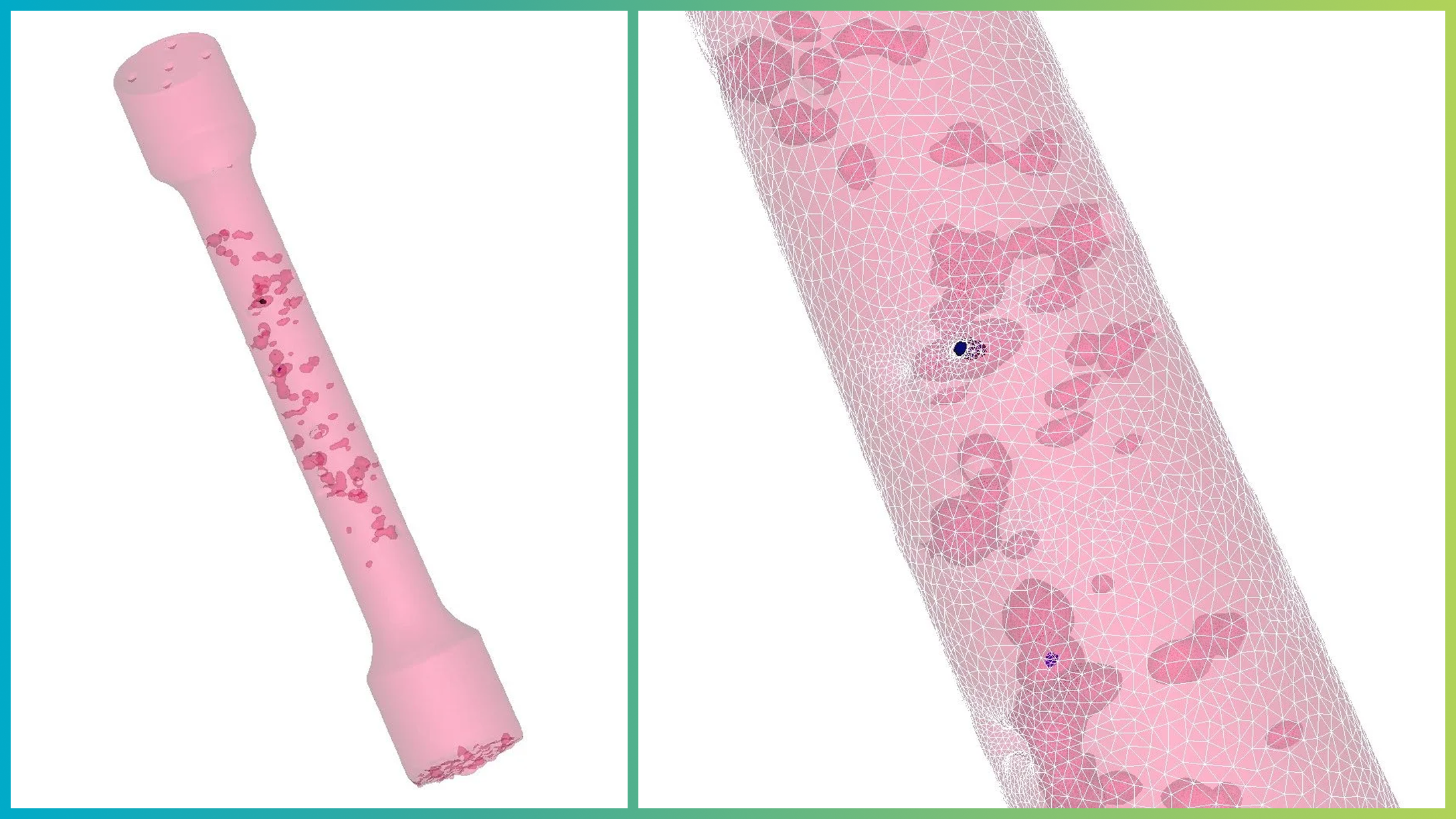
Identify, visualize, and remove unconnected element sets.
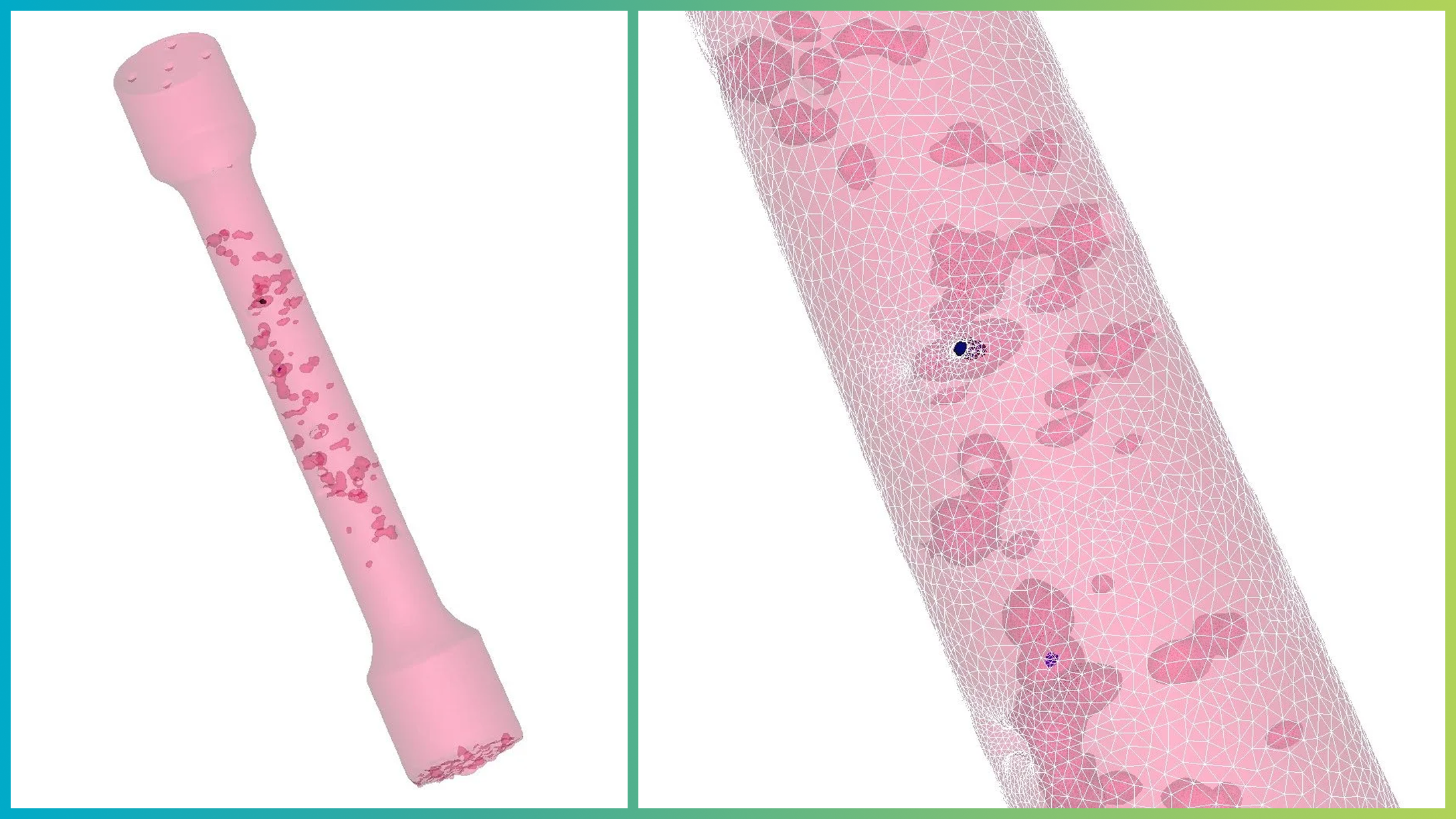
Identify, visualize, and remove unconnected element sets.
Connectivity of the FE mesh
The Volume Meshing module enables you to efficiently identify, visualise, and remove unconnected element sets to create a clean FE mesh without loose particles.
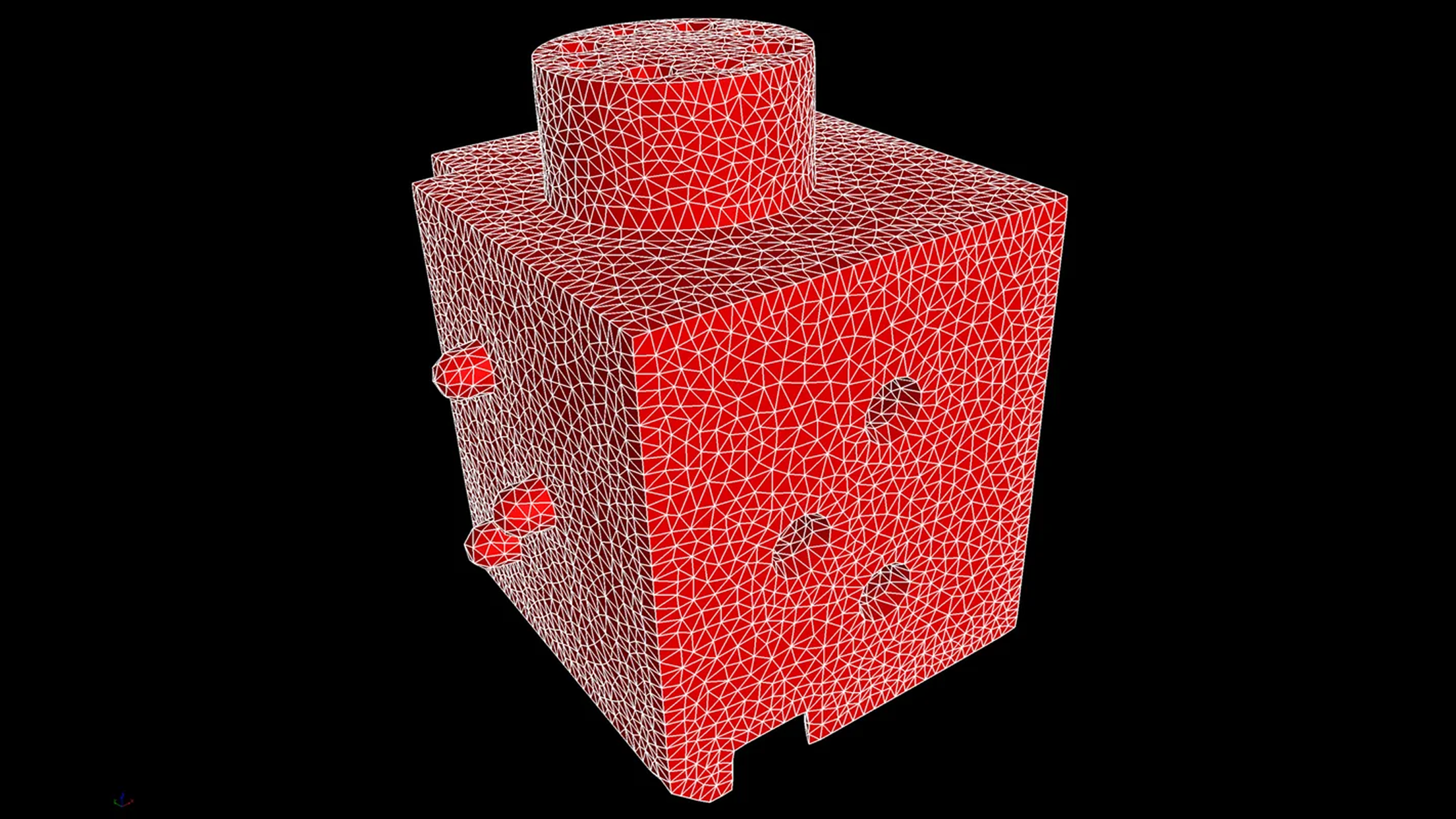
Create tetrahedral volume meshes for components containing sharp edges.
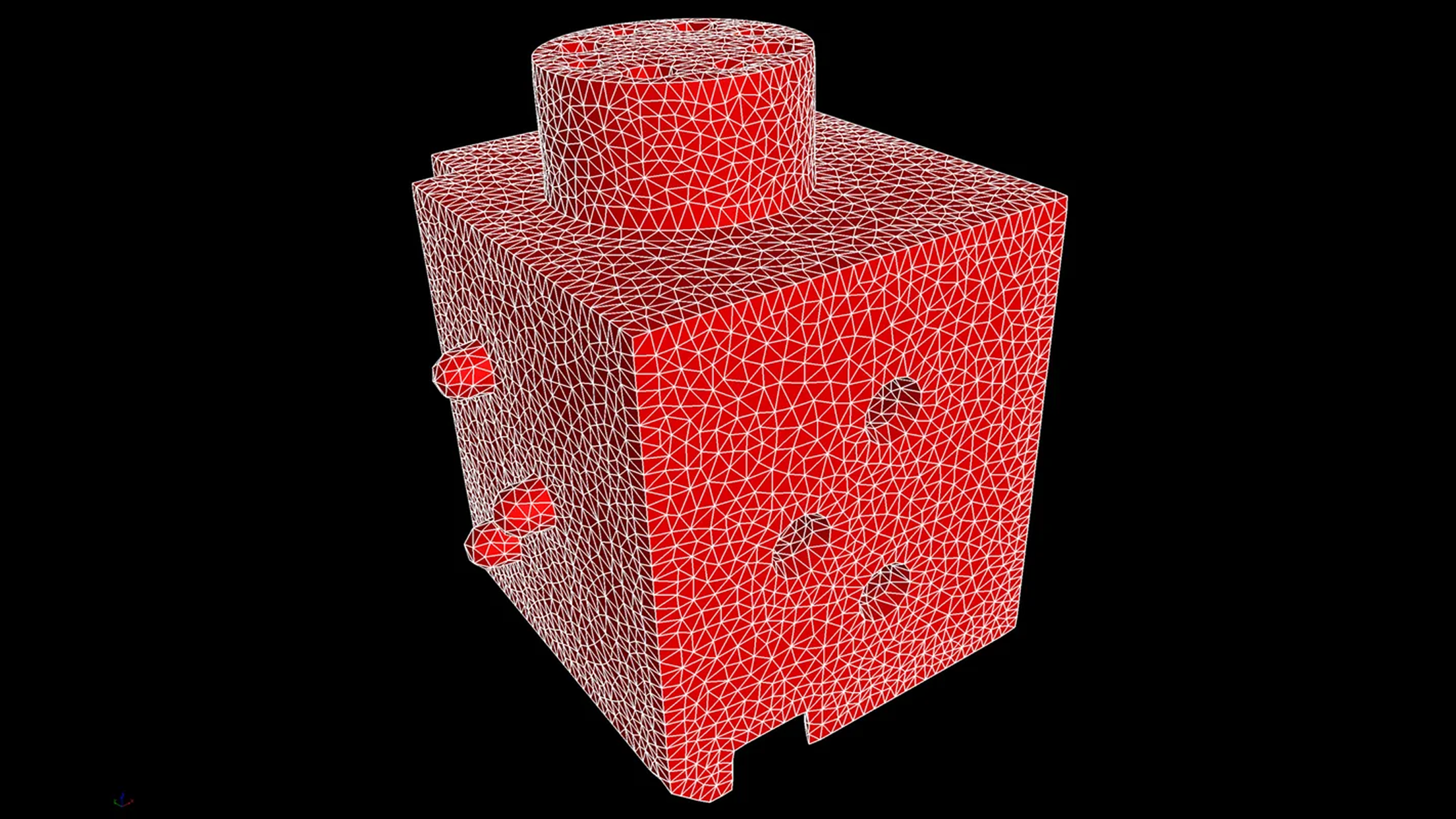
Create tetrahedral volume meshes for components containing sharp edges.
Sharp edges in tetrahedral mesh creation
Create tetrahedral volume meshes for components with sharp edges to achieve a more accurate representation of component geometry with a significantly reduced number of tetrahedral elements. When this option is activated, the algorithm identifies sharp edges in the component and creates a mesh that reflects these edges by aligning finite element (FE) nodes on them.
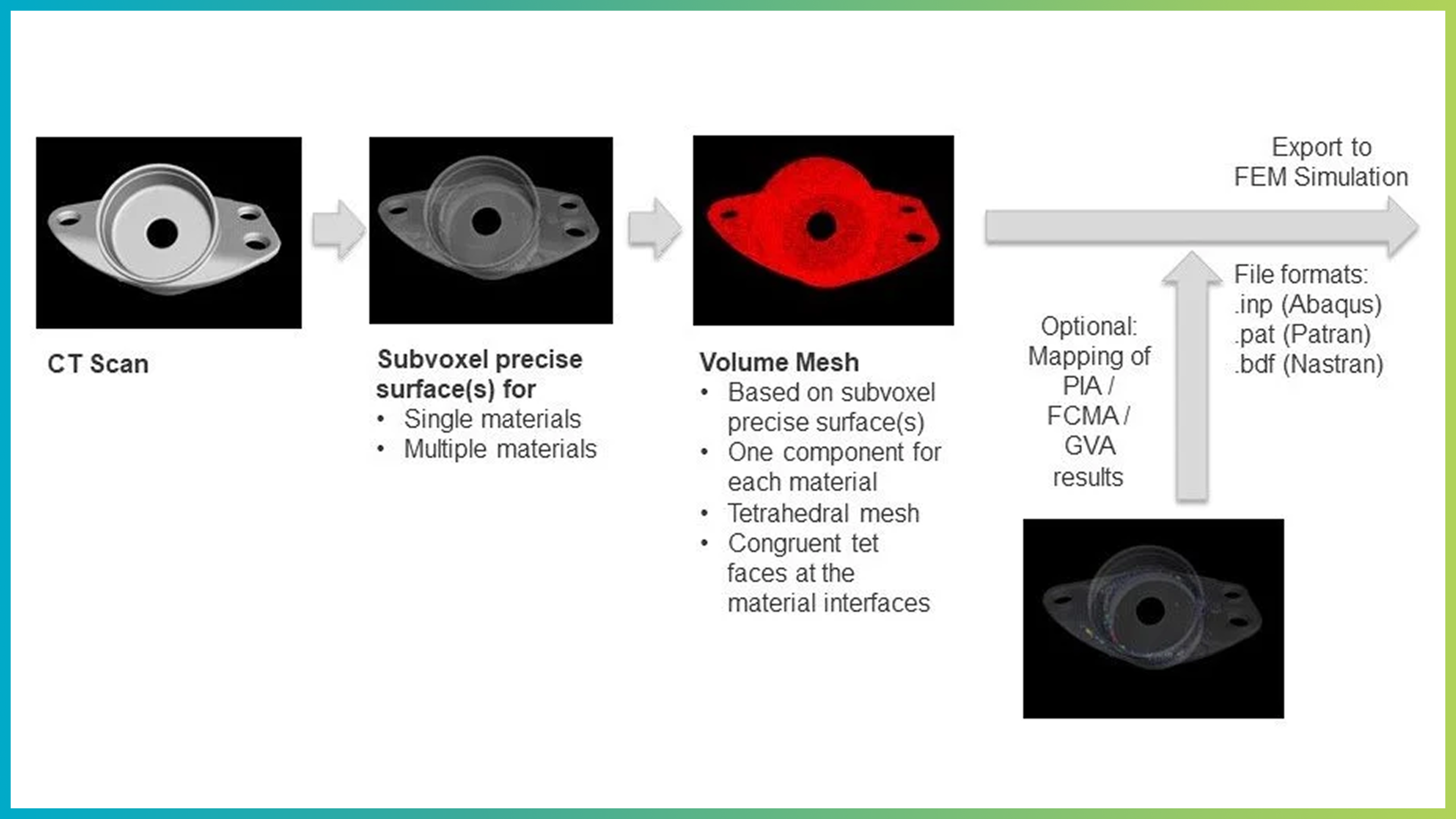
You can easily use microstructural information obtained by a porosity or a fibre composite analysis for FEM simulation.
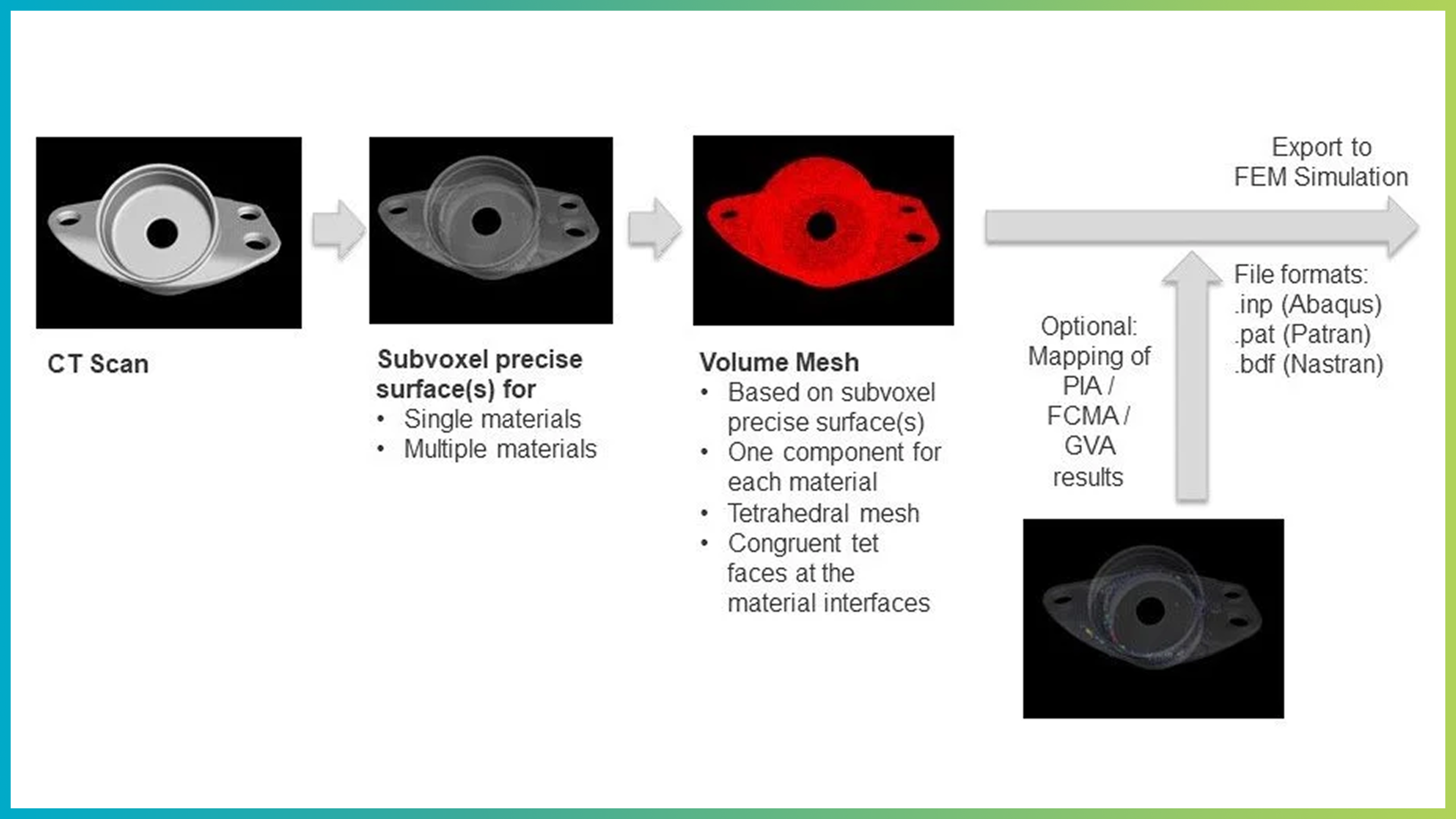
You can easily use microstructural information obtained by a porosity or a fibre composite analysis for FEM simulation.
Loading mesh cells with data from material analyses
You can easily use microstructural information obtained by a porosity or a fibre composite analysis for FEM simulation. Components of the second-order fibre orientation tensor and fibre volume fractions, as well as porosity and grey values, can be mapped on the tetrahedral mesh and exported.
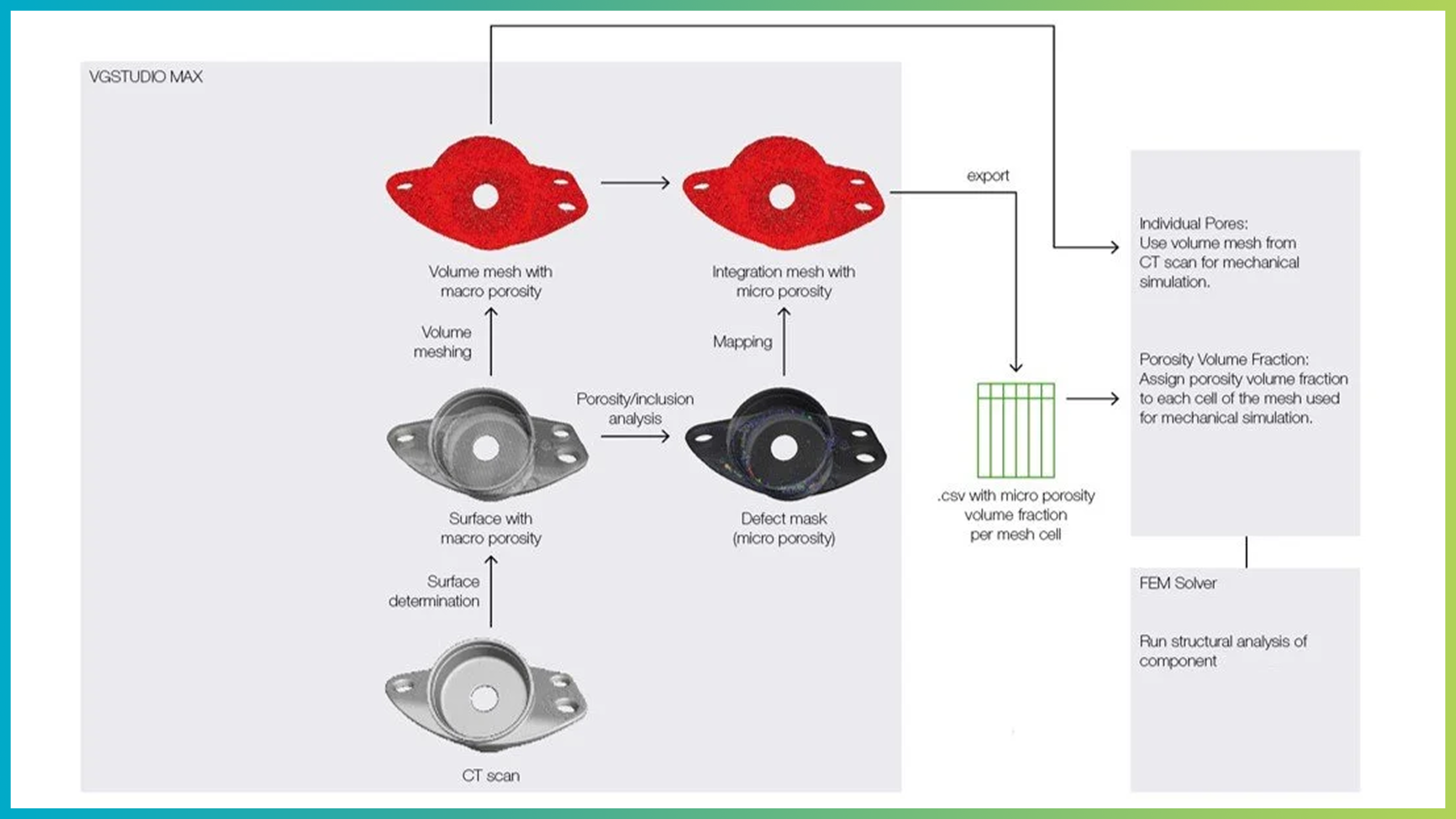
Workflow for including macro- and microporosity in FEM simulations
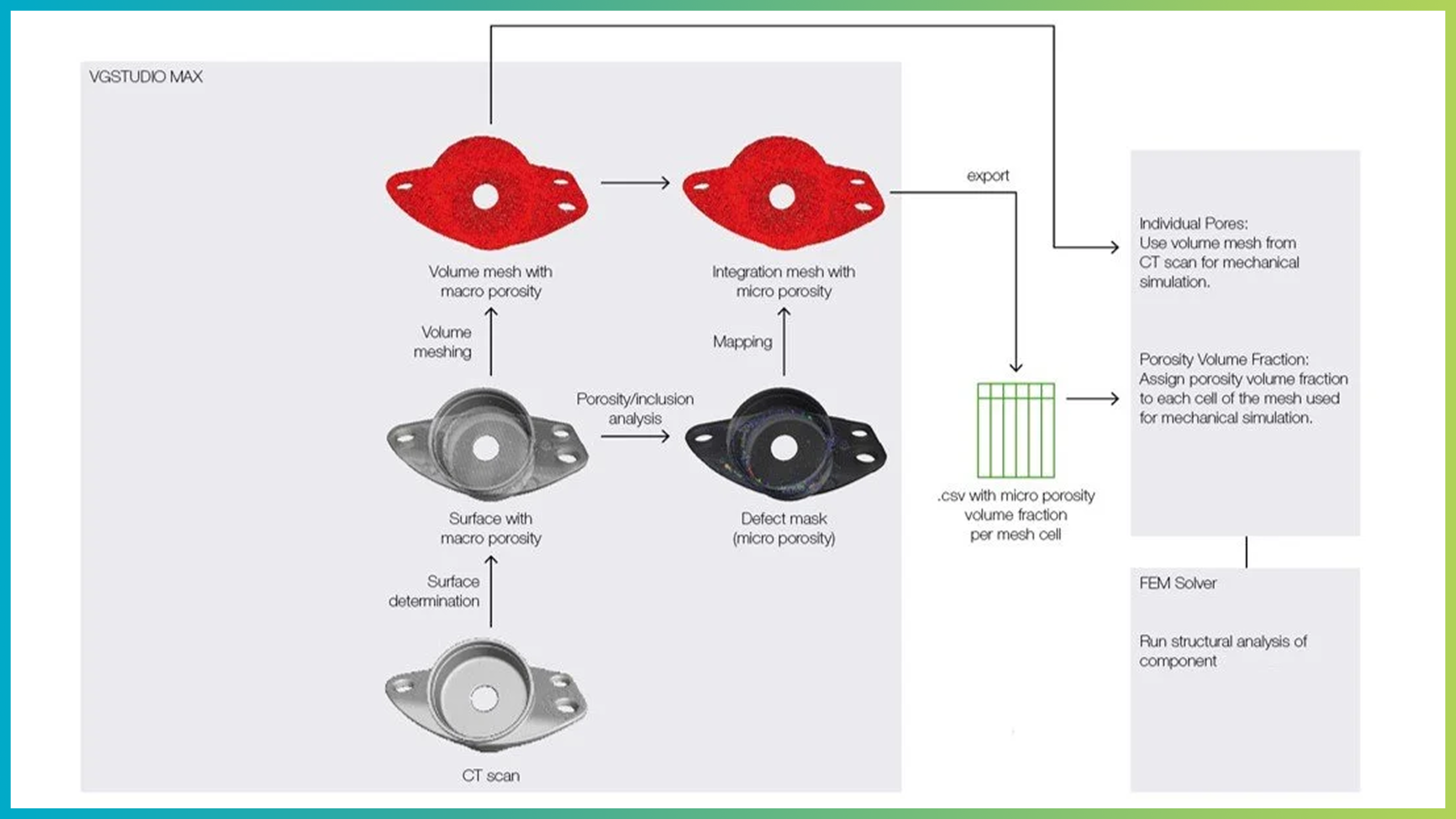
Workflow for including macro- and microporosity in FEM simulations
Distinguishing between macroporosity and microporosity
Macroporosity can be represented geometrically in the volume mesh by treating the border of the macro pores as internal surfaces, which are respected while meshing. Additionally, the microporosity can be mapped onto the volume mesh as a volume fraction of micropores for each mesh cell and exported in .csv format, which can be directly imported into, for example, Digimat for further use in an FE solver.
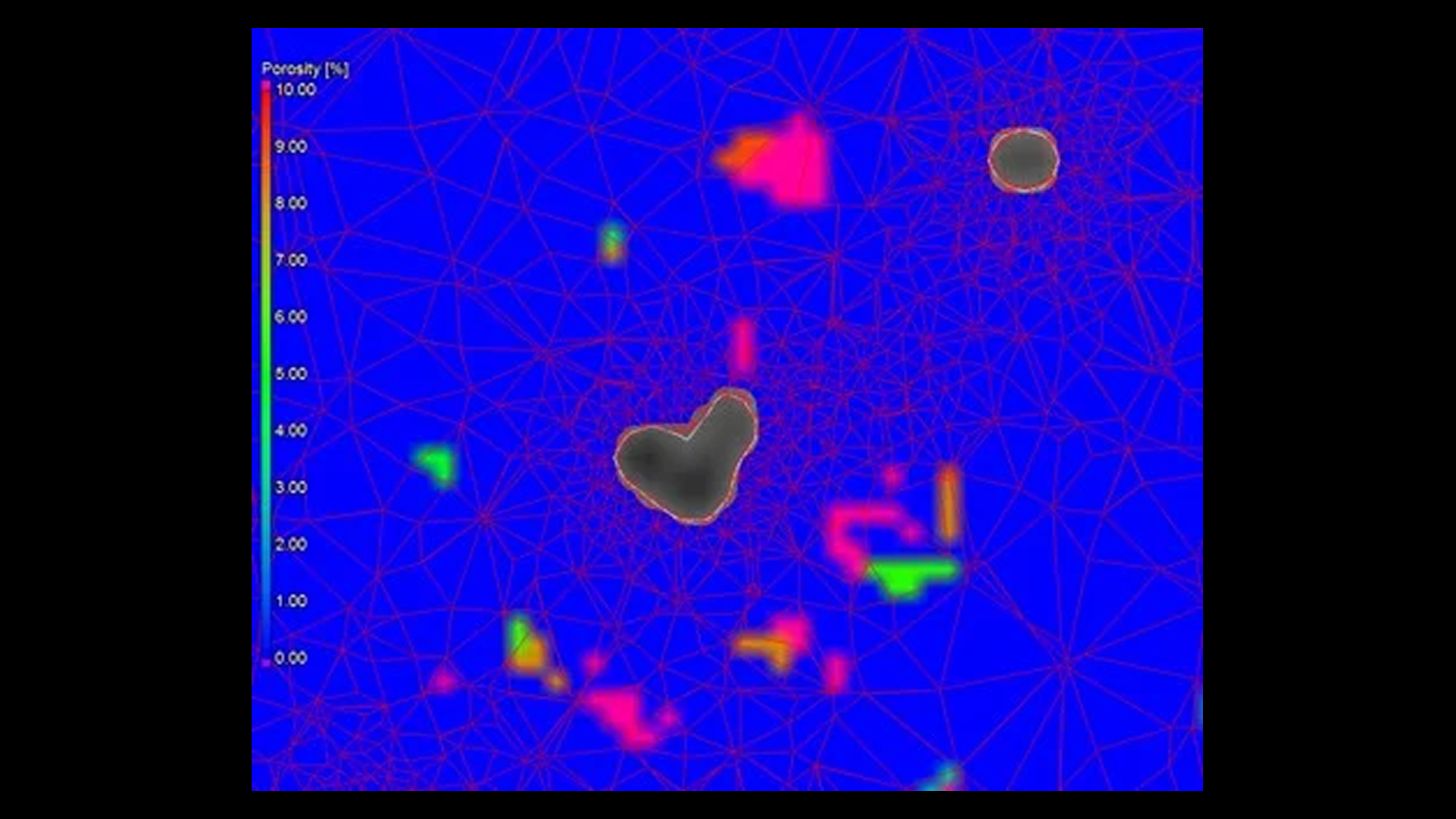
The volume mesh geometrically represents macropores; microporosity is mapped onto the cells of the volume mesh and colour-coded.
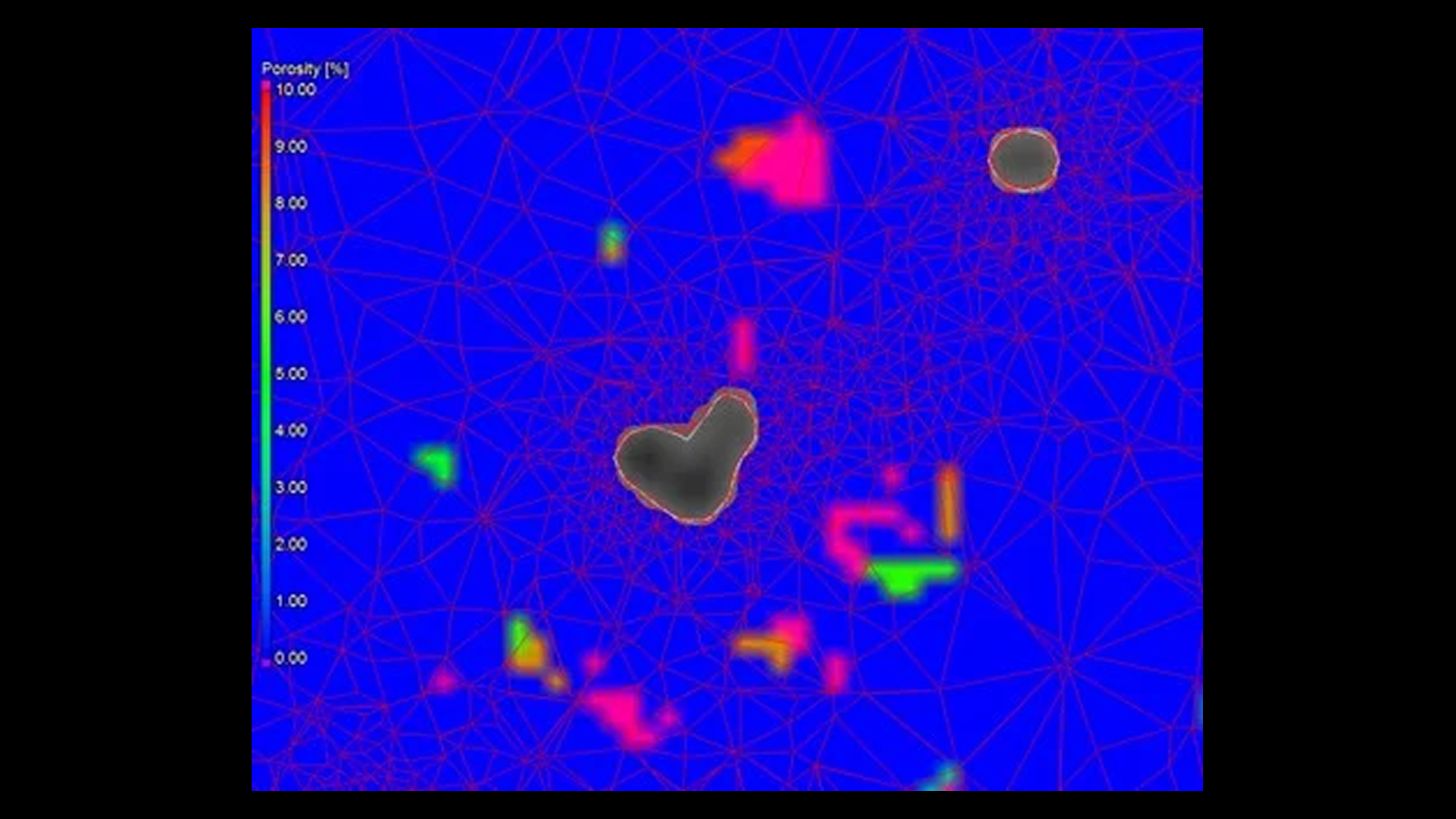
The volume mesh geometrically represents macropores; microporosity is mapped onto the cells of the volume mesh and colour-coded.
Exporting the volume mesh
The tetrahedral mesh can be exported for FE simulations using TET4 linear or TET10 quadratic elements in Abaqus (.inp), Patran (.pat) and Nastran (.bdf) formats.
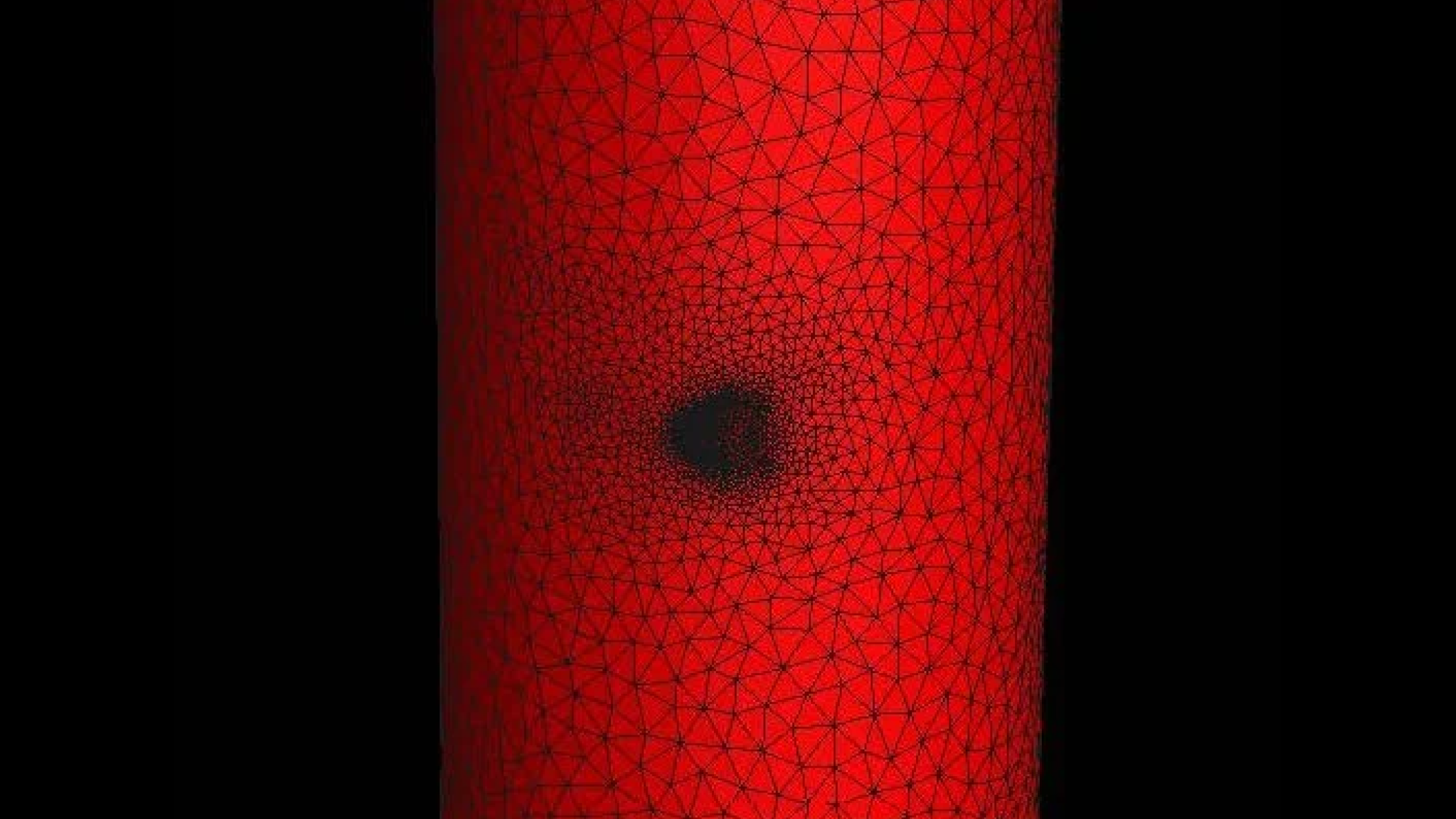
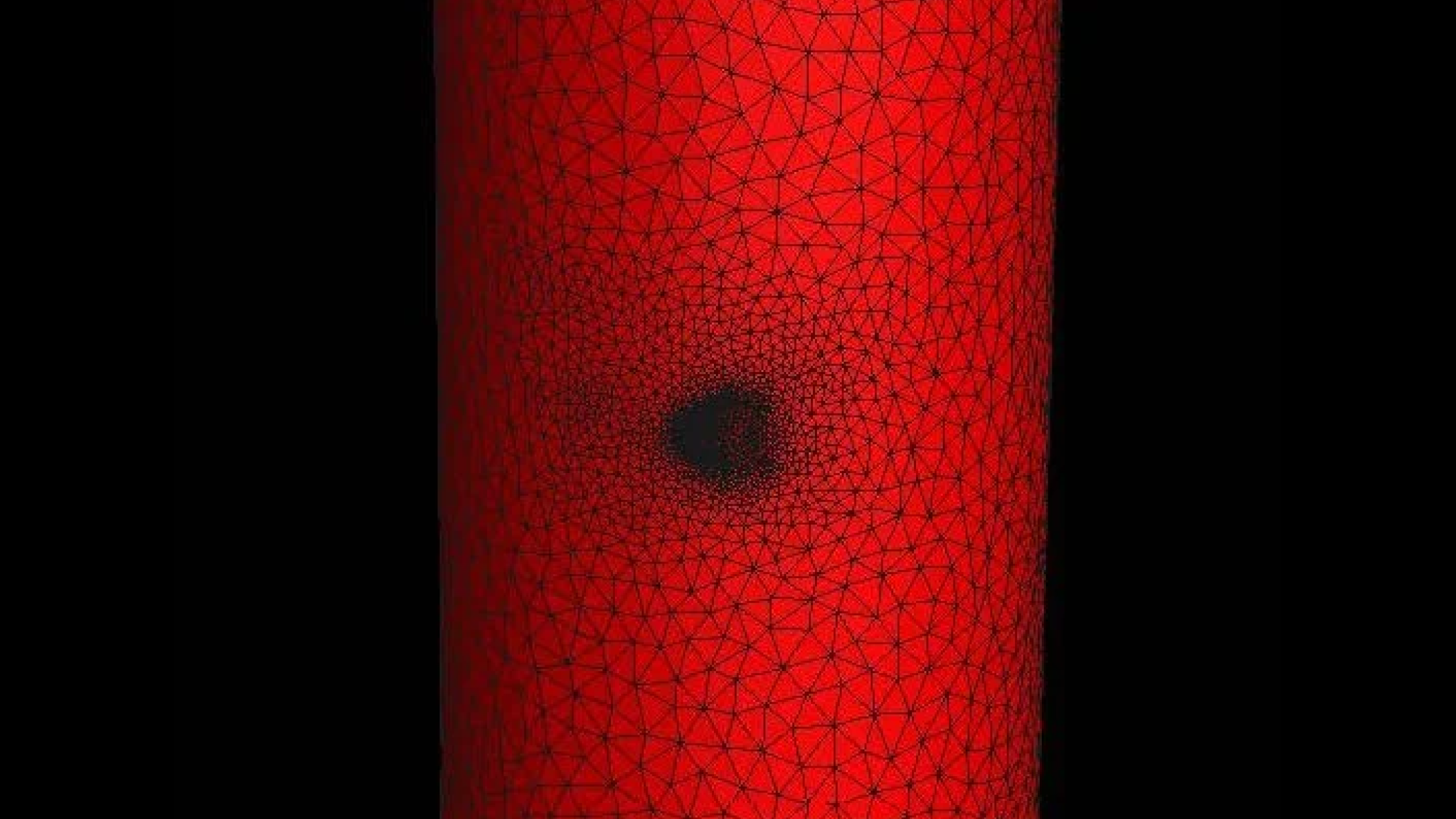
Best volume meshing of CT data among investigated methods according to study
Safran, an international high-technology group and tier-1 supplier of systems and equipment in the Aerospace and Defense markets, benchmarked volume meshing solutions from different vendors to find that the Volume Meshing module for VGSTUDIO MAX 3.4.4 offered the best results among the investigated methods. The company has explicitly examined volume meshing of computed tomography (CT) data as part of a PhD thesis.
Achieve unparalleled precision with subvoxel-accurate surface determination that preserves geometry integrity. Avoid the pitfalls of intermediate surface meshing and ensure your data remains complete and accurate for the most reliable analysis results.
Eliminate the need for manual preprocessing like surface mesh repair. Achieve high-quality meshes with minimal editing required and seamlessly transition from CT scan to volume mesh all within a single software solution.
Enhance your simulations with critical data. Load essential information, such as fibre orientations, fibre and porosity volume fractions, and grey values, to ensure comprehensive and informed simulation results.
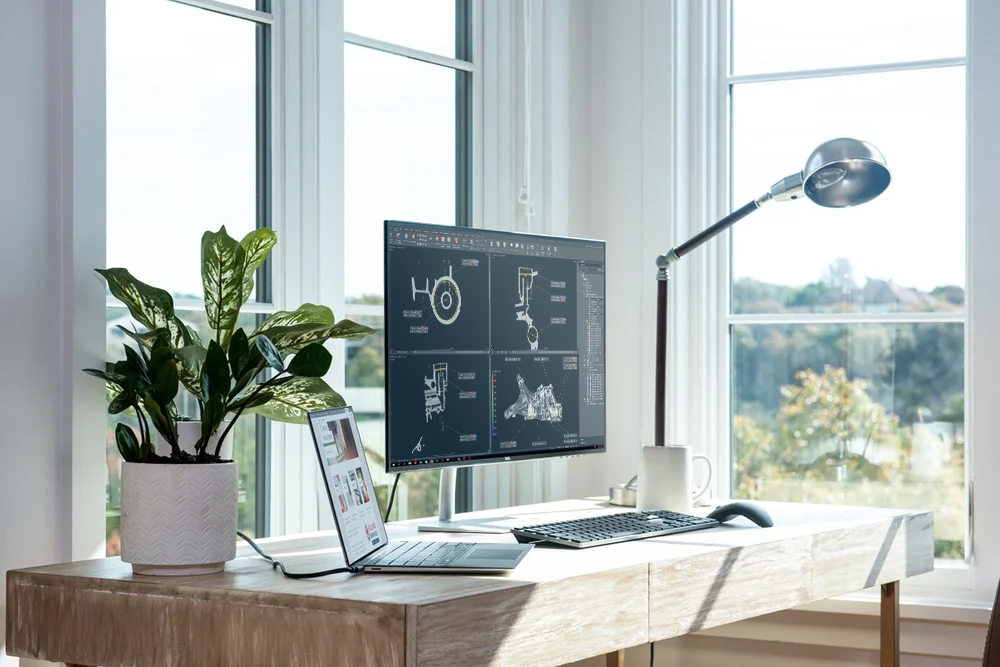
Contact us today—our team is ready to assist!
Request a quote