Sharp Design for Smooth Comfort
Conventional, off-the-shelf (OTS) orthopedic implants allow medical professionals to choose from a wide range of designs, materials, and manufacturers to treat most common patient needs. However, rapid progress in modern imaging techniques has created endless possibilities in the field of medical implants. Customized implants, for example, can—as opposed to ready-made solutions—mimic variability in the patient's anatomy, which improves overall kinetic function.
Off-the-Shelf vs. Patient-Specific
Patient-specific implants are generally more complex in shape than their off-the-shelf counterparts, and extensive CT scanning can result in a longer manufacturing period of 4–6 weeks. The initial costs may be more expensive, but faster surgeries, shorter recovery times, and the reduced risk of patient infections make them cost-efficient over time.
Furthermore, as patient-specific implants match the anatomy of the individual patient, they are guaranteed to last longer and greatly increase one's quality of life.
For this, let's take a look at a prototype of a craniomaxillofacial (CMF) implant of a zygomatic bone. Because of its complexity in covering the mouth, jaw, face, skull, and associated structures—which vary wildly from patient to patient—the implant needs to be customized to both match the patient's appearance and optimize chewing to ensure a higher quality of life.
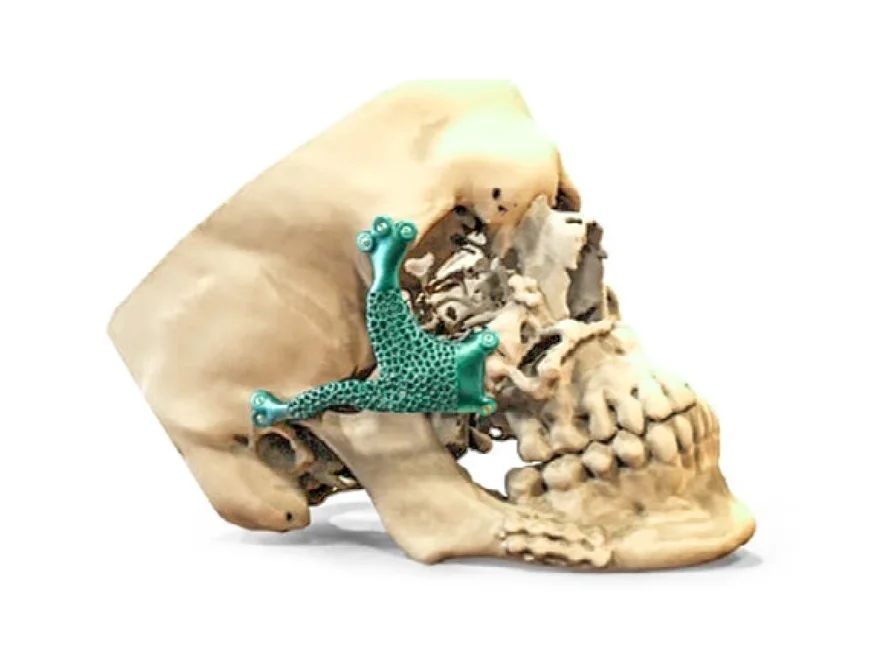
An implant prototype of a zygomatic bone
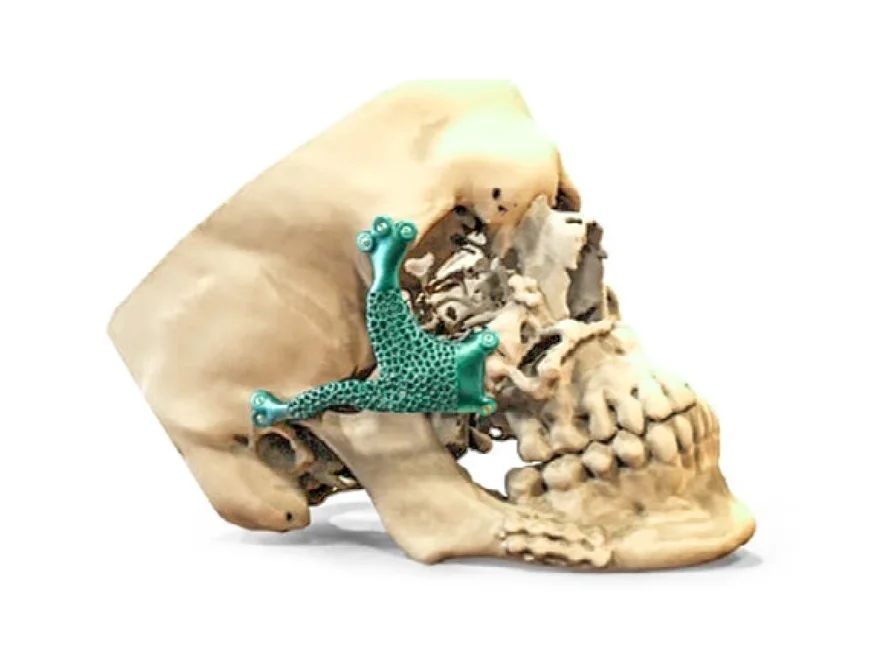
An implant prototype of a zygomatic bone
This is where 3D printing comes in.
Printing an Implant
Based on medical CT scan data, Ortosintese designed a CMF implant to restore chewing function in the right half of the patient's skull while maintaining facial symmetry.
Farcco then 3D printed the implant using electron beam powder bed fusion (E-PBF). Compared to laser powder bed fusion (L-PBF), E-PBF boasts a higher production rate and fewer post-processing steps. (For a quick refresher, check out our story on the different types of 3D printing technologies here)
A GE Additive Arcam EBM Q10plus system was used to print with Ti-6Al-4V ELI powder, a titanium alloy known for its corrosion resistance and high hard-tissue compatibility. Its fracture toughness and bone-bonding ability make it ideal for medical implants with stricter specifications—just like our CMF implant.
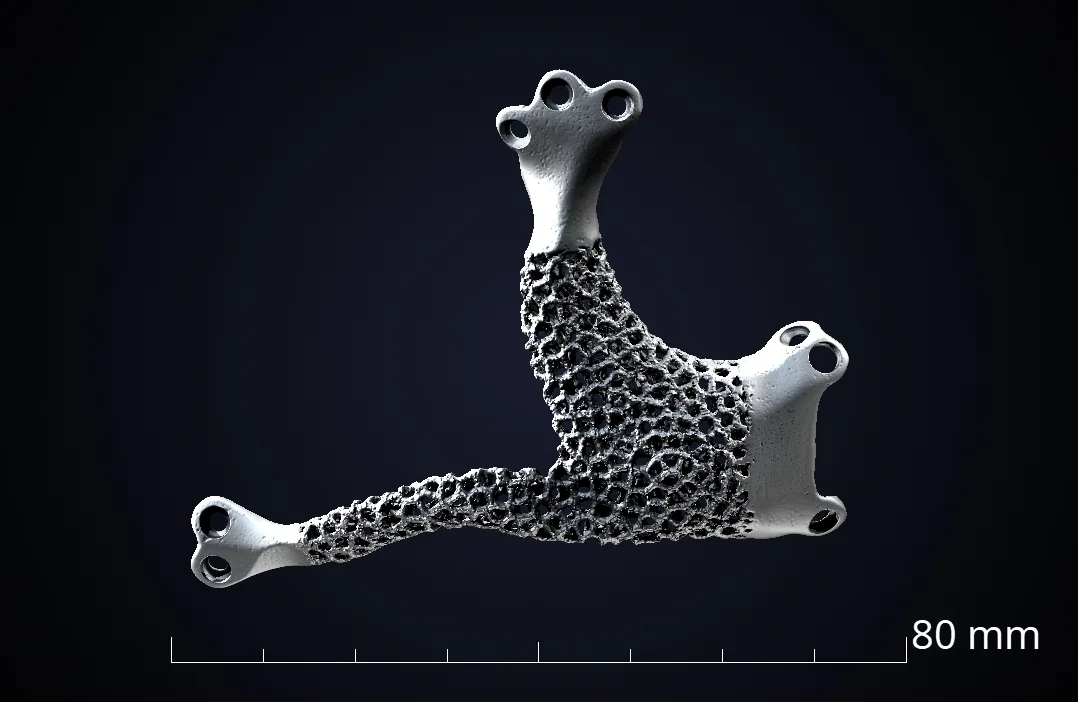
The dimensions of the implant are 72x60 mm; the part was printed using Ti-6Al-4V ELI powder
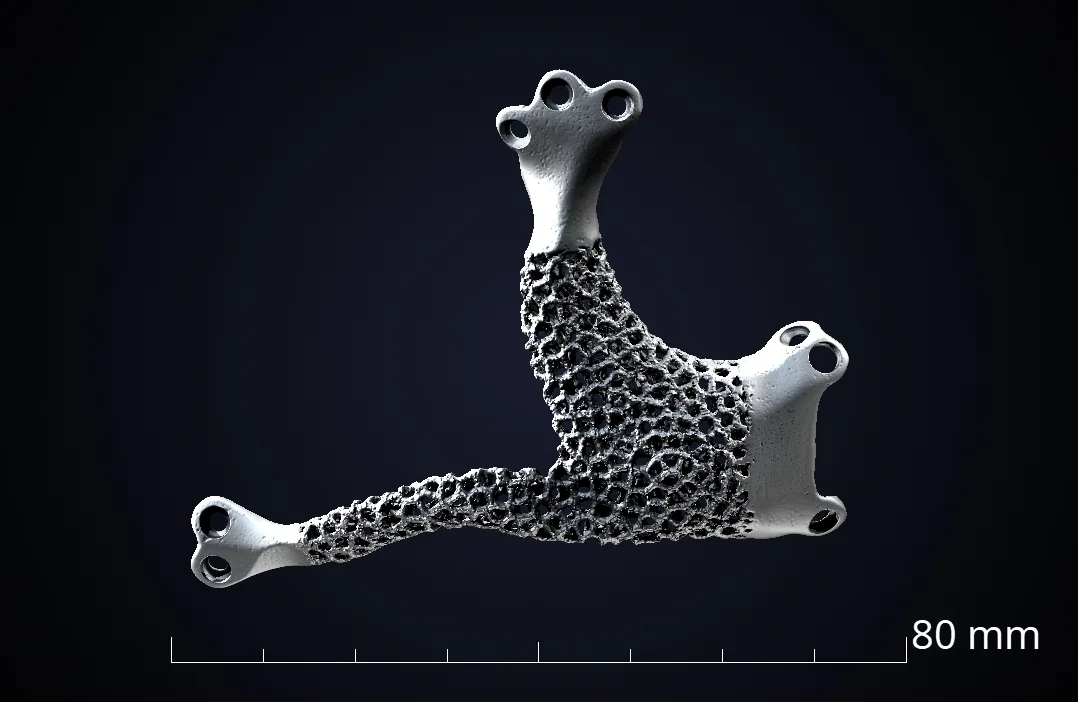
The dimensions of the implant are 72x60 mm; the part was printed using Ti-6Al-4V ELI powder
A high level of quality assurance is needed to match this complex technology and inspect these unique implants.
CT to the Rescue
Waygate Technologies created a CT scan of the CMF implant and used VGSTUDIO MAX to analyze it for overall geometrical accuracy. What is unique about this implant is the lattice structure that connects to the solid areas. It is of the utmost important to ensure its quality.
Lattice Structures in Orthopedics
Lattice structures allow for seamless integration. They take the appearance of a porous grid, comprised of thin struts that overlap each other while maintaining small spacings in between—known as pores. Pore size, strut size, and porosity can all be changed according to individual implant needs, which allows us to design the most effective, patient-specific implants.
Lattice structures have also been shown to offer better patient comfort while reducing occurrences of implant failure. As titanium density is quite high, they also reduce the weight of the implant and make it nearly as lightweight as real bone.
The freedom in design, combined with enhanced mechanical properties, translates to better patient outcomes.
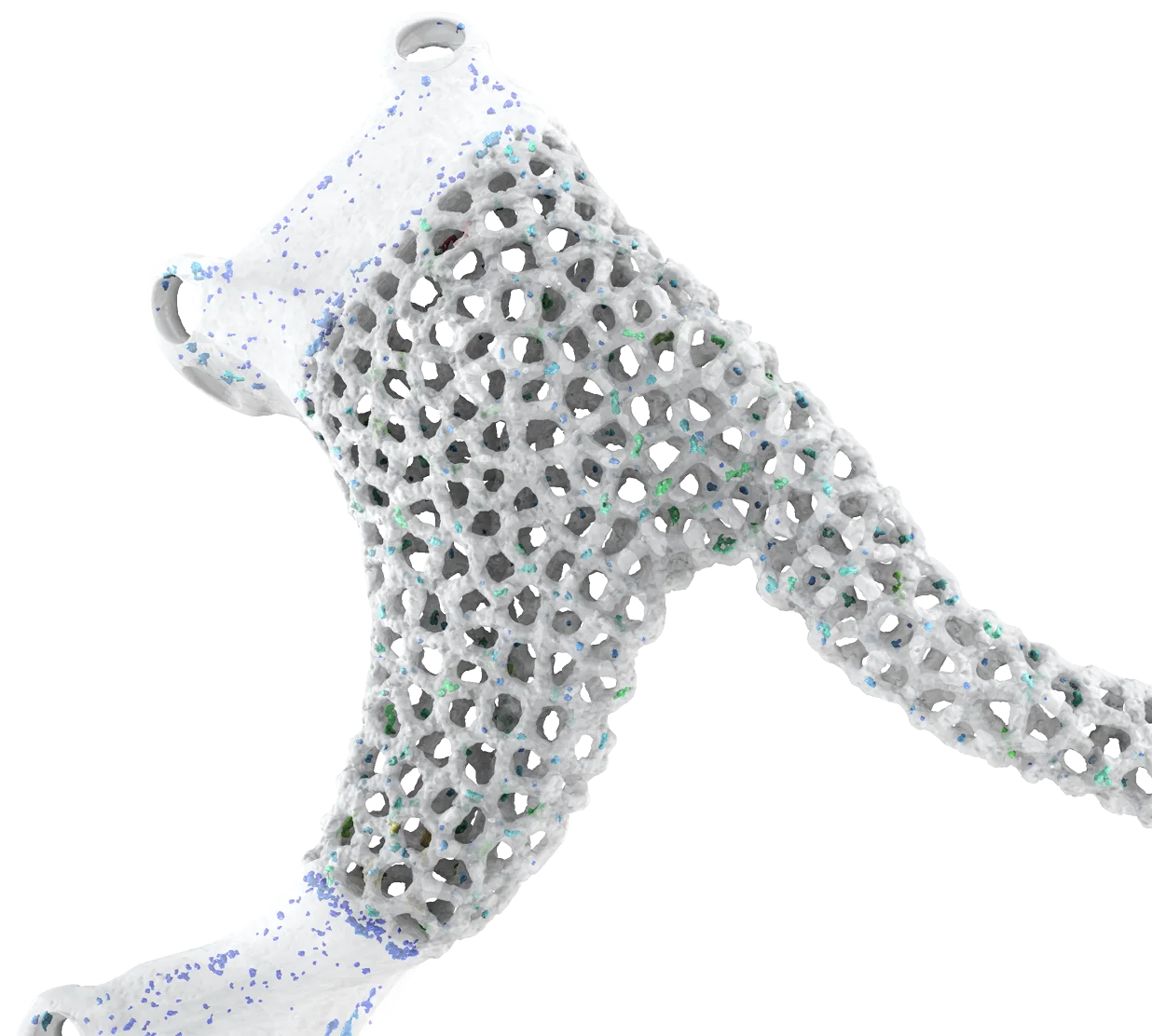
Pores in the implant prototype
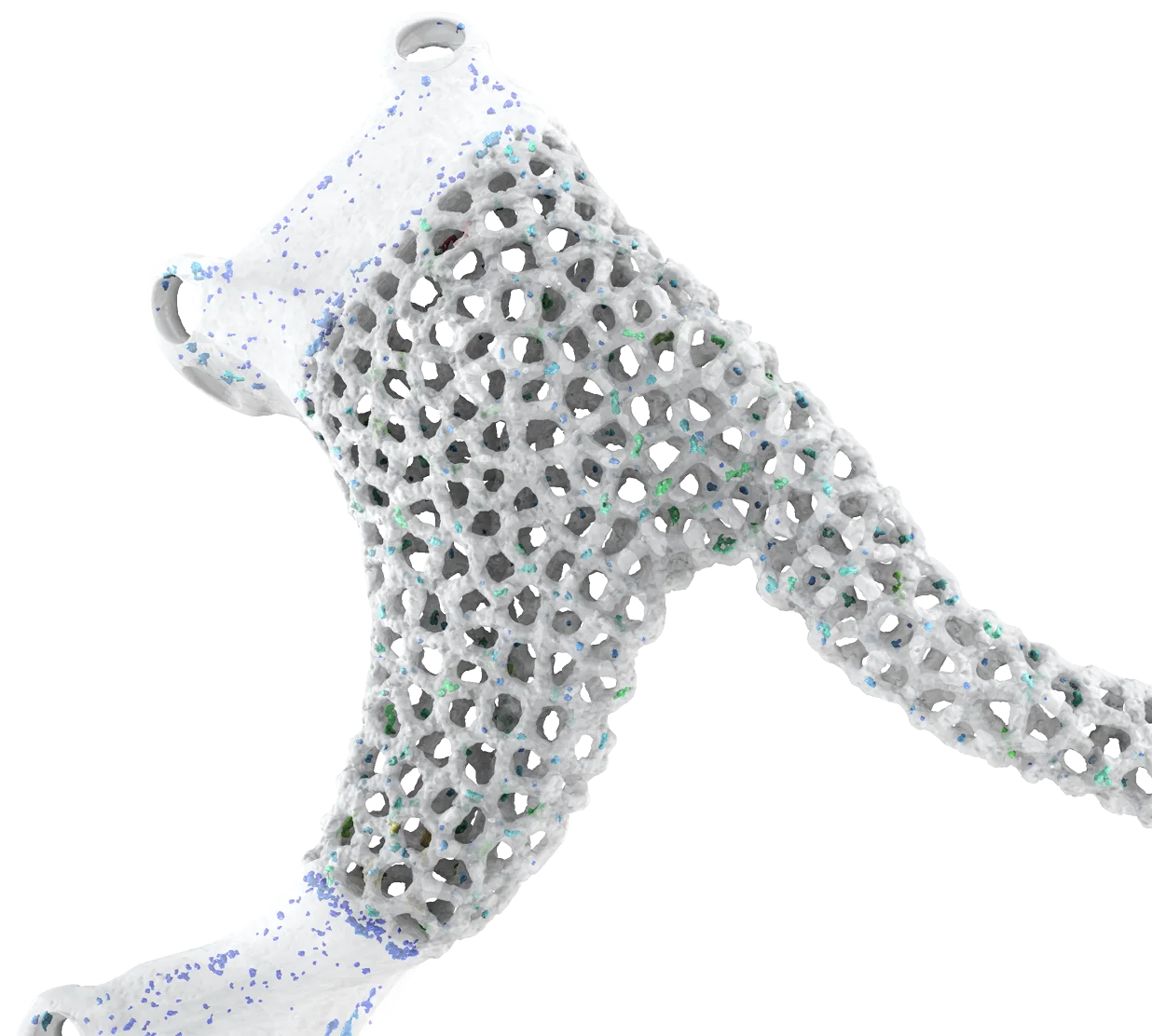
Pores in the implant prototype
Wall Thickness Analysis
A critical aspect of the design is the seamless connection between the lattice structure and the solid areas of the implant. Wall thickness analysis can easily evaluate the connecting regions by measuring the intended strut thickness. This is essential in ensuring the implant has no broken struts and that the final dimensions do not exceed the upper tolerances.
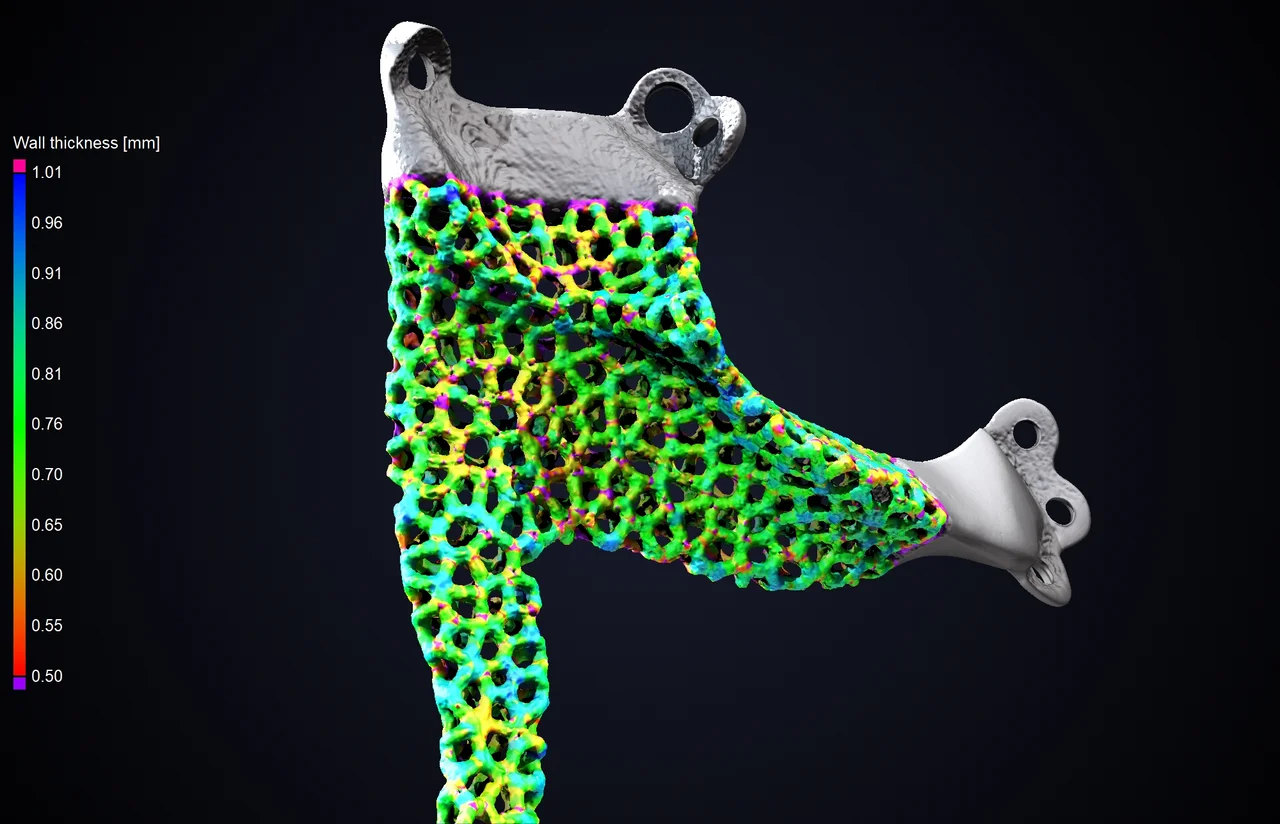
A wall thickness analysis of the implant can offer insight on the strut thickness of the surrounding lattice structure
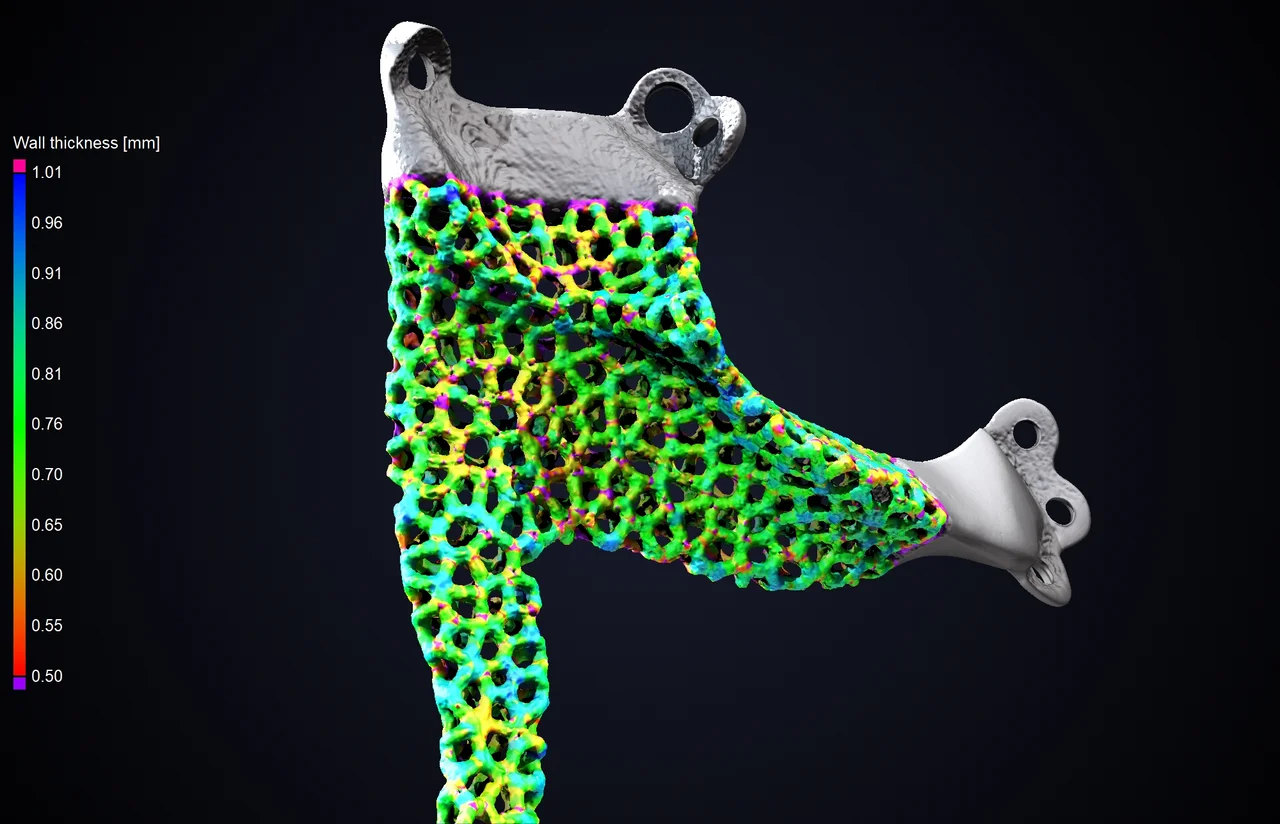
A wall thickness analysis of the implant can offer insight on the strut thickness of the surrounding lattice structure
Porosity/Inclusion Analysis
Aside from the overall geometrical accuracy, the porosity of the implant is another point of interest. A porosity/inclusion analysis can give us detailed information on every pore and detect critical pores based on location, size, and shape. Porosity data is valuable for optimizing process parameters for the E-PBF system.
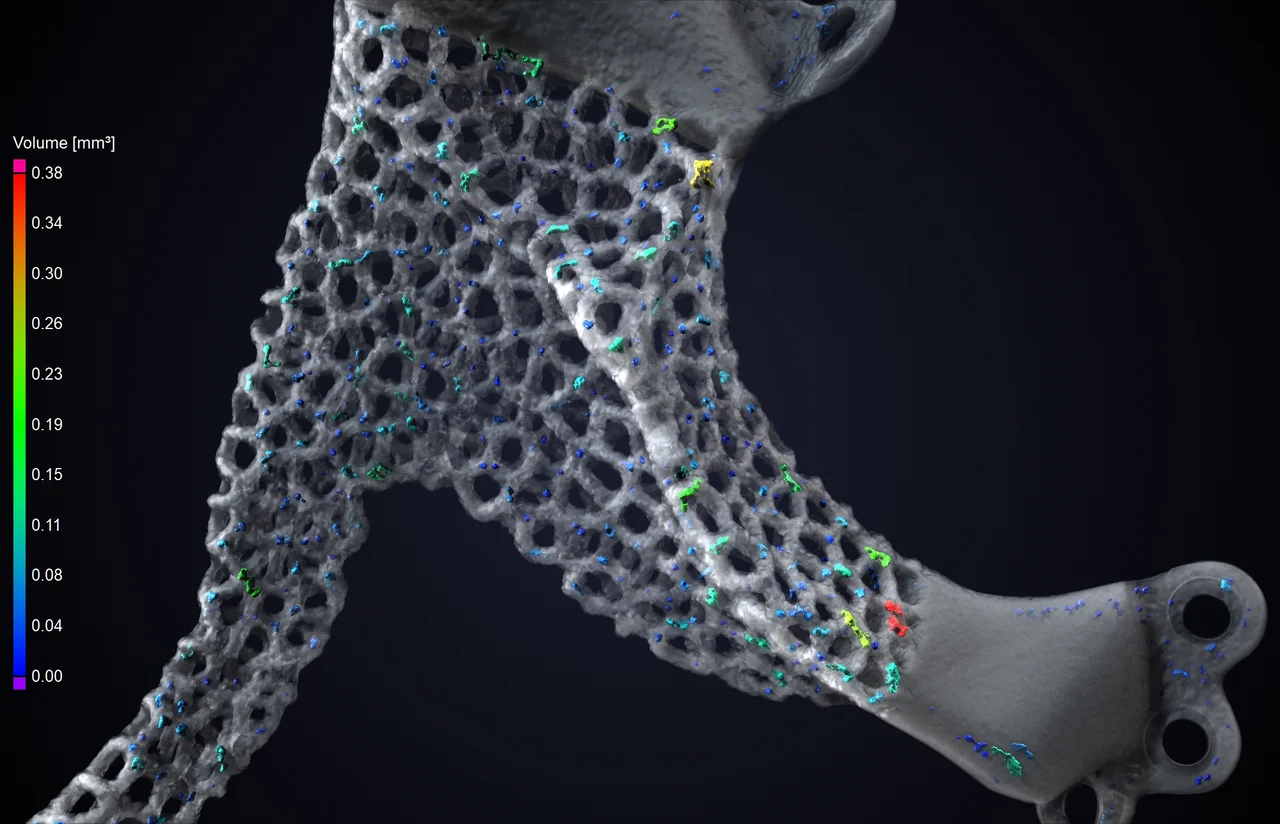
A porosity/inclusion analysis can provide insight on pores as well as detect critical pores in the implant
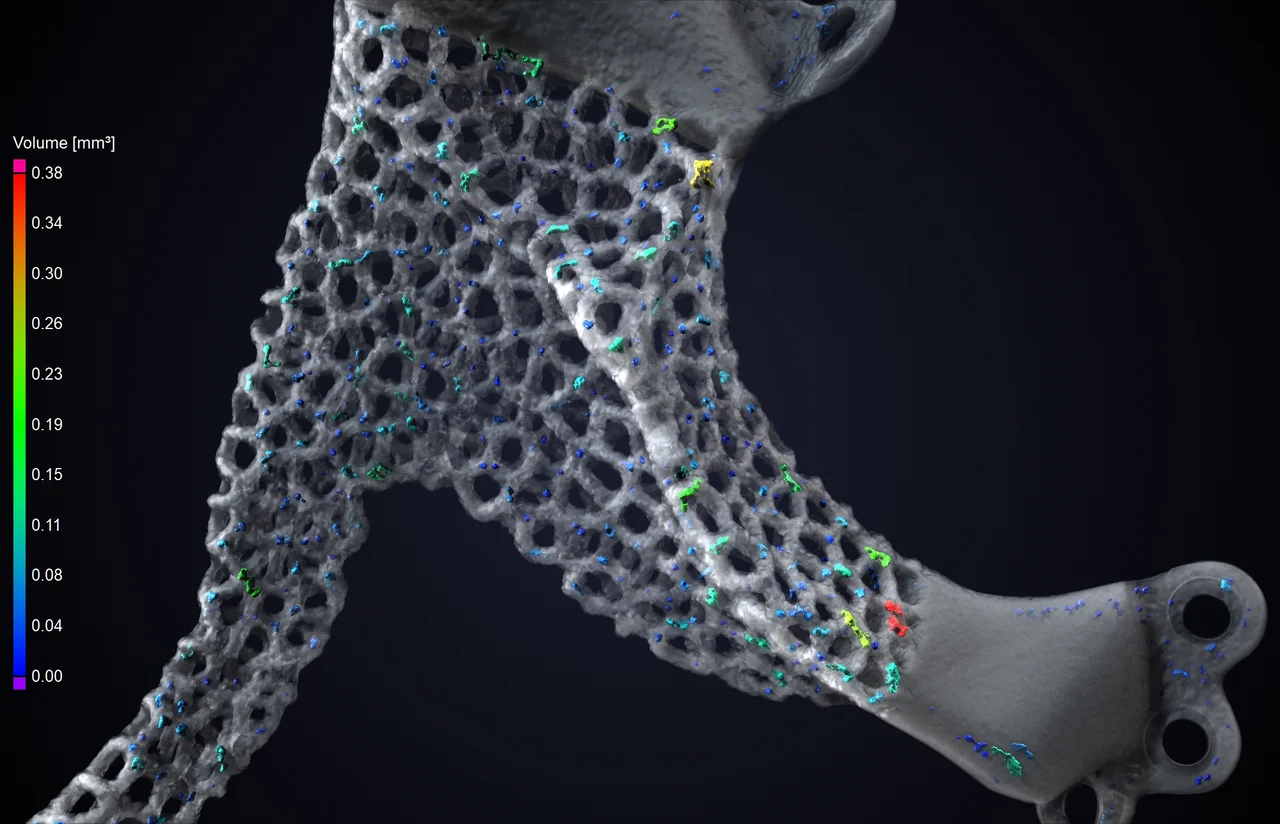
A porosity/inclusion analysis can provide insight on pores as well as detect critical pores in the implant
A porosity/inclusion analysis is also capable of detecting cracks and inclusions in the implant, but none were found here.
And with Our Powers Combined...
We've already mentioned that the lattice structure is an invaluable asset in customized implants. A wall thickness analysis and porosity/inclusion analysis have—separately—shown no critical issues.
But when we combine the analyses, we are able to see critical defects related to defect size and strut thickness of the surrounding lattice structure. This actually identified a few potential critical pores, but they were not classified as critical in their locations.
Did You Know? PIA + Wall Thickness
There is an option to consider wall thickness analysis as part of a porosity/inclusion analysis. This would calculate the relative pore diameter based on the results of the wall thickness analysis. In other words, it evaluates whether the pore is significant in relation to the thickness of the walls.
By combining the analyses, we are able to detect critical defects based on size as well as the strut thickness of the lattice structure.
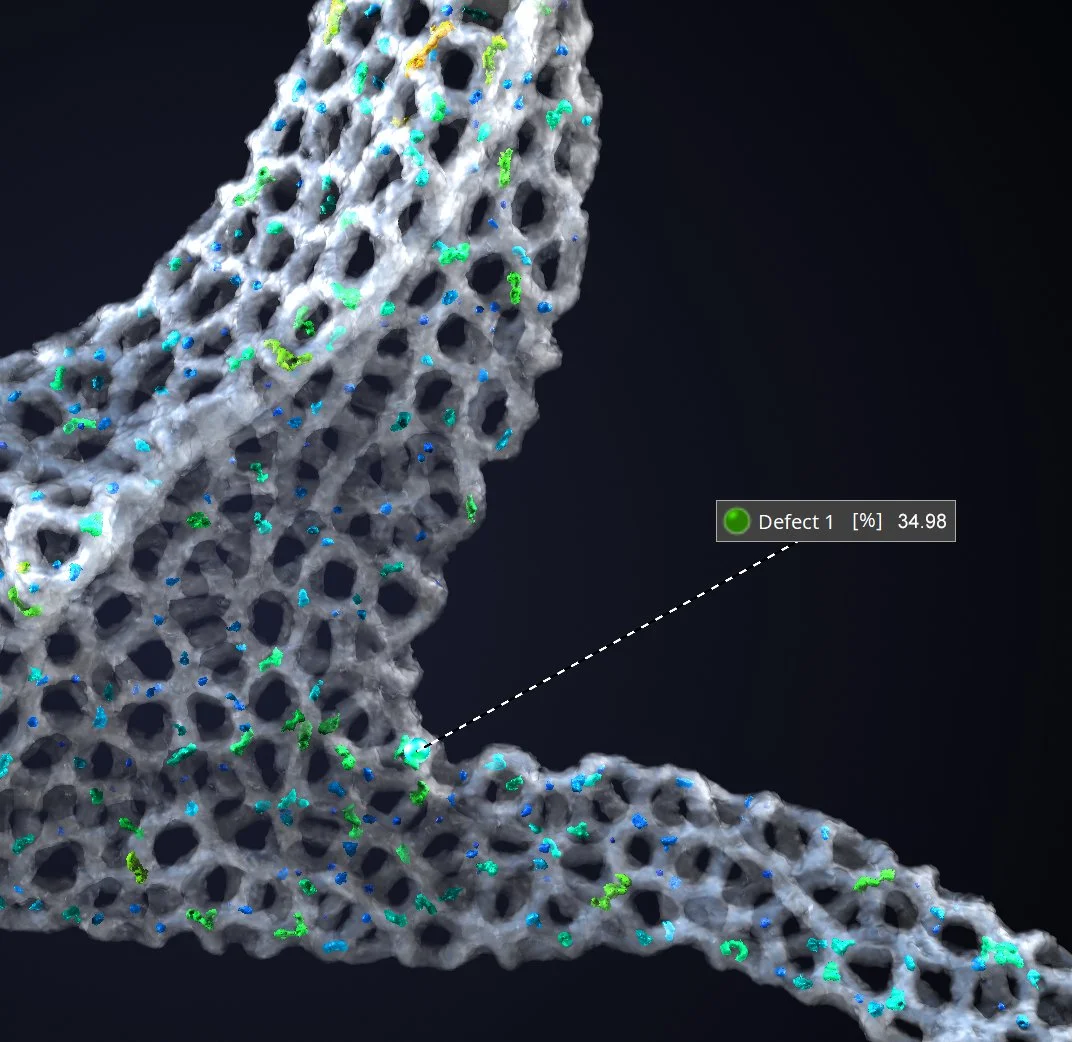
Checking the wall thickness analysis option as part of a porosity/inclusion analysis gives us the relative diameter of the pores
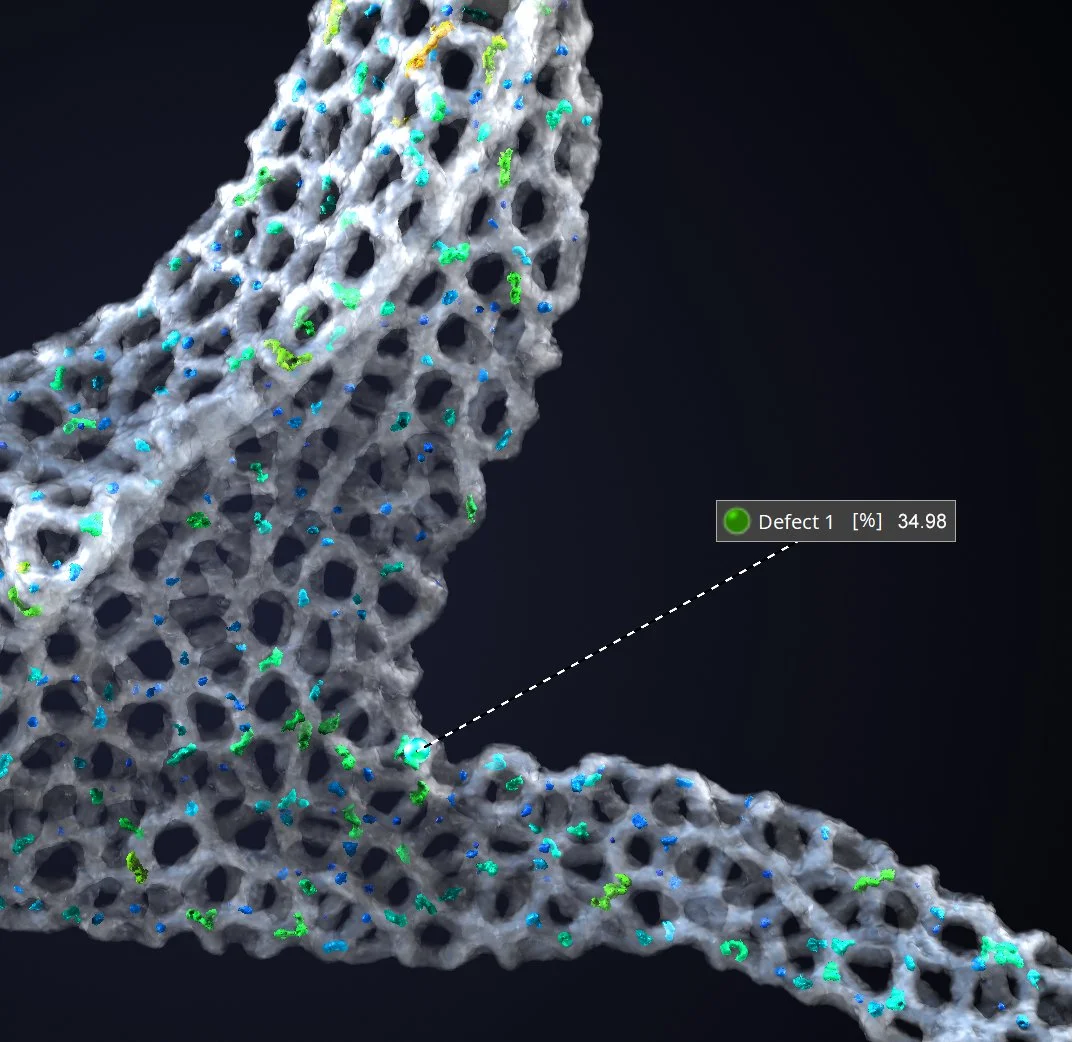
Checking the wall thickness analysis option as part of a porosity/inclusion analysis gives us the relative diameter of the pores
While the patient was later treated with an E-PBF-printed implant—but without the complex lattice structure—this is proof of concept. The insights and results derived from the inspection helped further optimize the implant design, the production and post-processing procedures, and the overall workflow.
The Future of CT in Medical Implants
CT technology has allowed us to design and inspect implants that take into account individual anatomy, medical history, and appearance. While the initial costs of patient-specific implants are more expensive, research has shown that shorter recovery times, reduced risk of patient infections, and longevity actually make them more cost-efficient over time.
Who knows? At the current rate of technological advancement, it is possible that automation can take over a large chunk of the process, making manufacturing even quicker and easier.
Ready to Learn More?
Users of VGSTUDIO MAX can find out more about wall thickness analysis and porosity/inclusion analysis in the tutorials included in the software.